7 Strategies of a Successful Inventory Manager & Real-World Examples
The job of a construction inventory manager is an ever critical one.
For example, did you know that, according to a joint Bain & Co./Microsoft survey, 47% of companies expect their supply chain organizations to provide input to most or all major strategic decisions (e.g., merchandising, operations, product strategy).
A recent report from Linesight noted that materials prices, which have been lingeringly high, will continue through 2023, with a possible economic downturn and projections for the industry to shrink by 7% (Linesight report via For Construction Pros).
In this article, we breakdown some high-level inventory management principles, then shift gears to discuss inventory management strategies with real-world inventory strategy examples that should prove inspiring! What’s more, any business—from sole proprietors, craftspeople, and tradespeople looking to level up their business acumen to mid-to-large contractors and construction executives—can study these strategies as scripture.
Let’s go!
Jump Ahead:
- Inventory Management Definition
- Inventory Management Principles
- Inventory Management Strategies
- Collaboration, Intradepartmental, & Cross-Departmental Communication
- Cloud-Based Inventory Apps & Digitization
- Software Integration & Interoperability
- Automation
- Job Costing & Reporting
- Smart Tools
- Inventory Strategy Examples
Inventory Management Definition
Inventory, at its essence, is “a complete listing of merchandise or stock on hand, work in progress, raw materials, finished goods on hand, etc., made each year by a business concern.”
If we know that to be true, inventory management is the verb to that noun, to “take stock” of what you have, to inspect and control the flow of your on-hand assets to the job—from as low cost as drill bits to those high-ticket items like cranes, whose misplacement could set off alarm bells. That said, no asset is insignificant—after all, ensuring you have the right stuff in your PACKOUT™ ahead of the job is mission-critical to keeping a day’s work on schedule, preventing project downtime.
- Related Article: Small Tool Tracking: Think of Hand Tools as Assets, Not Consumables
Outside of the professional trades, this could be e-commerce companies making sure their warehouses have (or suppliers are sending) enough stock on the shelves to meet orders—in manufacturing, it could be making sure enough raw materials and hard-to-find parts, like semiconductors, are sourced accordingly to meet demand.
Inventory management is empowered through the processes, principles, and tools in the hands of a business owner to do just that.
Inventory Management Principles
Here are some of the common inventory management principles that transcend industries.
Just-in-Time Manufacturing (JIT) and Lean Construction
One concept that is often muttered in the same breath as inventory management is just-in-time manufacturing, and, what’s more, this term is often quickly succeeded by lean manufacturing within the same sentence.
Just-In-Time Manufacturing Definition
As the name implies, “Just-In-Time,” or JIT for short, is a manufacturing principle that prioritizes only getting what’s needed to the customer as it’s needed.
The Institute for Manufacturing at the University of Cambridge calls Just-In-Time (JIT) manufacturing not just a principle, but a “management philosophy,” originally referring “to the production of goods to meet customer demand exactly, in time, quality and quantity, whether the `customer' is the final purchaser of the product or another process further along the production line.”
JIT manufacturing concepts, which are believed to be first pioneered by Toyota in the early 1970s (see Toyota example), are similar conceptually to how a grocery store will place orders to their suppliers for only what’s needed on their shelves to avoid spoiled milk and perishables. A similar financial concept, “first in, first out,” prioritizes selling the oldest inventory first, just like how grocers will place older jugs of milk up front and the newer ones behind—only to unwittingly have shoppers pull from behind to get a fresher milk jug (you know who you are!).
A similar principle can be applied to older equipment. While we generally recommend preventive maintenance to predict and avoid unexpected breakdowns and lengthen the life of the tool, a common question arises, “should I repair or replace my tools and equipment,” for which we generally recommend a 50% the cost rule, as well as considering purchasing backups for tools older than 5 years.
Lean Manufacturing Definition and Lean Construction Principles
Lean manufacturing principles are often coupled with JIT. Similar to JIT, Lean manufacturing is a production system focused “relentlessly […] on eliminating waste from the manufacturing process.”
60% of production activities in a typical manufacturing operation, a research study found, are waste, adding no value at all for the customer (Lean Enterprise Research Centre via Lean Production).
Typically, the five lean manufacturing principles are outlined as such:
- Defining customer’s point-of-view
- Mapping the customer’s value stream
- Creating flow, to eliminate lead time – you can use this among your construction inventory KPIs to measure your strengths, weaknesses, and successes
- Establishing a pull system
- Practice continuous improvement
Lean construction, likewise, borrows lean manufacturing practices and applies them to the construction industry. Common Lean construction examples in application include offsite construction companies, which can help construction companies meet deadlines by building prefabricated components and whole modules to be later delivered and installed onsite. Lean construction can help take strain off the onsite team and help with QA and even beat unpredictable weather thanks to these operations taking place in temperature-control, sterile environments.
Safety Stock
Safety stock is an inventory management term that refers to the extra quantify of supplies and resources intentionally set aside as a precaution for unforeseen events, also commonly called “buffer” or “reserve” stock, a cushion that helps prevent you running out of items in your inventory (“stockout”).
Safety stock is important because they can help facilitate critical transfers to keep jobs running on schedule.
FIFO and LIFO Accounting
Investopedia defines FIFO and LIFO as such:-
FIFO, an acronym for “First in, first out,” meaning an “asset-management and valuation method in which assets produced or acquired first are sold, used, or disposed of first.”
-
LIFO, an acronym for “Last in, first out,” meaning “a method used to account for inventory that records the most recently produced items as sold first.”
Investopedia offers the following breakdown of advantages and disadvantages of FIFO vs LIFO accounting and why you might choose one method over the other.
FIFO | LIFO |
Pro: Higher net income compared to other methods. |
Pro: Lower tax liability compared to other methods |
Pro: Higher inventory balances compared to other methods, strengthening an organization's balance sheet. |
Pro: May be easiest to implement if inventory is easily accessible, because it has been recently purchased |
Con: Higher tax liability compared to other methods. |
Con: Doesn’t represent actual movement of inventory (i.e. many companies try to move older inventory). |
Con: May not accurately communicate the true cost of materials if inventory has been stagnant while prices have risen. |
Con: Lower net income compared to other methods. |
ABC Analysis
ABC analysis in materials management and inventory management is an “inventory categorization technique” that typically groups inventory into three categories. ABC is acronym that is generally believed to mean “Always Better Control” (e.g., Intuit, Oracle NetSuite).
These three categories are as follows:
- A Items represent assets in your inventory with the highest annual consumption value. Think those cranes, bulldozers, or the top-of-the-line MX FUEL™ equipment, etc. These items represent your highest priority and rarely, if ever, should experience stockout.
- B Items represent items that sell regularly but not nearly as much as A items. For tool managers, this could be high-use drills/drivers, impact guns, etc.
- C Items comprise your remaining inventory that doesn’t sell much, has the lowest inventory value, and makes up the bulk of your inventory cost. This could be consumables like drill bits.
Summarizing in their Quickbooks blog, Intuit notes that inventory categorization plays an “essential” role in preventing losses from spoiled inventory and can serve as the first step in reducing obsolete inventory, supply chain optimization, increasing prices,” as well as helping with construction forecasting.
Types of Inventory Management Strategies
Now that we’ve covered common inventory management principles, here are 7 inventory management strategies to deliver better results and productivity:
- Inventory Tracking
- Collaboration, Intradepartmental, & Cross-Departmental Communication
- Cloud-Based Inventory Apps & Digitization
- Software Integrations & Interoperability
- Automation
- Job Costing & Reporting
- Smart Tools
1. Inventory Tracking
As we’ve previously reported, contractors waiting around for materials to arrive can be a major productivity staller.
Inventory tracking is critical to avoid these instances.
Cris Lauer Aranda, an Enterprise Account Executive at OSA Commerce and a career veteran SME in the supply chain industry, agrees. “Item-level tracking is very specific,” he says. “There are so many different variables—from the each (the individual piece), the inter-carton, or the case.”
On a jobsite, that could be a misplaced drill you suspect is stolen when really it was just moved. There are so many moving parts, subcontractors working—proper inventory tracking to the field and back to the crib can be symphonic, while poor lines of sight can be like the skipping needle on that ultra-rare Led Zeppelin record.
Barcoding
Barcoding is practiced in warehouses in virtually every industry that manages a supply chain and ships products.
Lauer agrees that barcoding is a mission-critical inventory tracking practice that can “be used at all different levels—not just the item-level or at different locations, but also at workstations around the warehouse, from inbound receiving to staging locations.”
“Barcodes,” he adds, “are especially important to track inventory so you know how much you moved from where and what needs to be replenished.” He says you can and should have a proactive approach to replenishment of stock. “You should never be out of stock completely,” and recommends “setting thresholds within your system to notify staff when a product reaches a certain amount to ensure inventory is replenished before it is out of stock.”
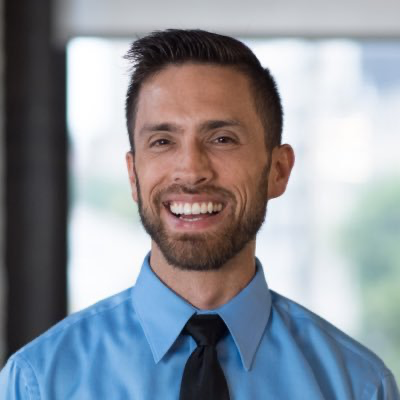
“Barcodes are especially important to track inventory so you know how much you moved from where and what needs to be replenished. You should never be out of stock completely."
Cris Lauer Aranda·OSA Commerce
Tool managers can use either third-party barcodes or Asset ID Tags, a process commonly referred to as equipment or asset tagging, with the ONE-KEY™ app.
The barcoding feature also replaces oftentimes expensive barcoding hardware. What’s more, our product offers construction-grade durability to last the lifetime of the tool and greater functionality (GPS location update with every scan).
Kitting
Kitting and bundling, Lauer confirms, is a process used in distribution centers (DCs).
“You need to be able to track every single piece of inventory within a specific location,” Lauer explains, adding, “so having barcodes to identify not only the location but also the different measurements of a product in those locations, and the different units of measure they’re in dimensions.”
He expounds, “For example, within cases, you can have bags of specific hardware, that then can also be sold as eaches—these units need to be tracked in the inventory system to ensure balancing the P&L and understanding how much product is in your warehouse.”
Tool managers can similarly take advantage of tool kitting in One-Key to better understand what they’re storing and what they’re sending. If you’re sending a bulk gang box full of tools, for example, you can add these items to a “kit,” then add a barcode or asset ID tag to that kit and save yourself a lot of head scratching. That is to say, rather than manually inspecting everything, a simple scan of the barcode will show everything you’ve previously added to this kit. That audit can then be checked against and communicated back to the crib if anything didn’t arrive as expected—or on the opposite side of the coin, at the end of the day it can be used to check against what needs to be sent back.
Equipment Trackers
Equipment trackers offer greater functionality to keep better sightlines to your equipment as you send it to the job. Bluetooth tagging practices include adding trackers with integrated Bluetooth. Products like this include our One-Key Bluetooth Tracking Tag, a multi-award-winning product (see: Chicago Innovation Award, Pro Tool Innovation Award) for its innovations, like an accelerometer to deliver more contextual “last used” location updates, NFC, a built-in speaker, and more.
These added features can be useful to trace an item’s “last used” location information within the last 30 days or to pinpoint an item’s location when you know it’s on the jobsite (but out of sight) or in the crib within 100-ft.
Bluetooth trackers utilize the app and our Bluetooth tracking network, the largest in the industry, to anonymously crowdsource item finding by sending location updates when your tracker comes in range with others nearby who have the app installed.
IoT & Digital Twins
Lauer explains what customers need of a digital product is “a single source view of your entire tech stack.”
Integrating seemingly cerebral concepts like the Internet of Things (IoT)—i.e., a network of individual objects of all types, shapes, and sizes that are connected to the internet—and Digital Twin—i.e., virtual representations of an objects or systems that spans lifecycles, receive real-time data, use simulation, and machine learning to help decision making—are ever-important.
One example of an IoT network would be a common piece of advice we give our end users to expand their Bluetooth range:
- Assure tool tracking permissions are properly configured
- Have your nearby coworkers also download the app and ensure they also have their Bluetooth and Location Service app permissions are set properly according to their device OS (e.g., Android, iOS)
- Use Bluetooth trackers and One-Key compatible smart tools
- Set up geofences for any place you have inventory tied up to ensure you’ll be alerted if tools start to wander
The following sections will build on these principles.
2. Collaboration, Intradepartmental, and Cross-Departmental Communication
A key component inventory managers need to focus on improving across their organization, Lauer explains, is “partnership.”
“A good thing for the industry is intradepartmental and cross-departmental communication,” he explains. “Things are siloed, unfortunately. Not only in supply chain/logistics, but in companies overall… when you get down to the boots on the ground, nobody knows what the other hand is doing.”
These silos are the problems to solve, he adds. “If manufacturing isn’t speaking to supply chain, if supply chain isn’t talking to the warehouse, you’re going to have stockouts.”
Indeed, 60% of general contractors see problems with coordination and communication between project team members and issues with the quality of contract documents as the key contributors to decreased labor productivity, according to a joint Autodesk-Dodge Data & Analytics report.
Features like our Multi-User Admin lets tool teams better collaborate with customizable permissions to ensure the right people have the right access to the right actions. Deep Links allow authorized parties contextualize reports and get the information they need faster.
What’s more, integrations help ensure cross-functional teams like design, field ops, project management, etc. can work better collaboratively, assuring their apps of choice sync.
3. Cloud-Based Inventory Apps and Digitization
The speed at which construction is digitized has been slow and disjointed. For example, 19% of UK construction firms say that their projects are entirely paper-based, Autodesk reported.
90.9% of firms report using smartphones on a daily basis for work purposes, JBKnowledge reported, with 62.4% of companies using mobile devices in the field for daily reporting.
Cloud-based inventory apps mean real-time access to inventory resources across all your devices, wherever you are:
- Access to service records and unlimited cloud storage for receipts and valuable documentation – so you don’t have to go digging for it, but rather, it’s there when you need it
- Access to reporting dashboards and customizable reports related to important inventory information, like tool management and alerts
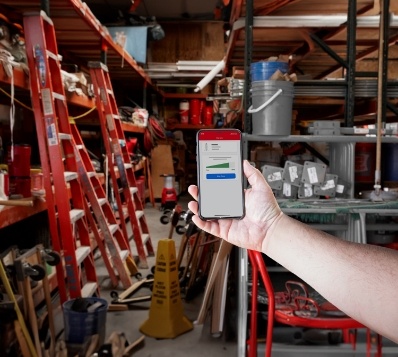
eBook
Cutting Chaos from the Crib
Learn how to make a tool inventory: In this free eBook, get tips on tool crib design, organization, and operating procedures.
4. Software Integration & Interoperability
While the use of cloud-based platforms and mobile apps are on the rise, major work is still needed with regard to how these apps integrate.
For example, according to the same above-mentioned JBKnowledge report, 21.4% of construction firms use 3 or more mobile apps for their projects. 23.6%, however, say “none” of the software applications they use integrate.
Similarly, only 16% of executives say their organizations have fully integrated systems and tools, a KPMG survey found.
Yet another Autodesk + FMI survey found only 18% of firms consistently using mobile apps to access project data and collaborate.
Our 2023 construction industry expert roundup found that integration was going to be a continued problem to solve, with similar remarks echoed at the recent Construction Progress Coalition 2023 iSummit.
Integrations between design teams, project management, and even IT departments already exist for One-Key users, and continued industry integration is part of our DNA.
- Related Content:
5. Automation
Responsible uses of automation (like Toyota defines it,"jidoka,” which loosely translates as "automation with a human touch") that make inventory managers’ jobs a little bit easier go a long way.
Even having automated tasks, like the ability to upload items in bulk, automate changes across items of the same kind, the ability to use existing entries to add multiples, or people from your address book so you can text or email them without leaving the app—these are some of those simple automations.
Furthermore, our smart tools can help automate repetitive tasks to increase productivity, repeatability/accuracy, and prevent repetitive motion injuries.
Adopting more advanced automation, like construction robots to automate dangerous tasks and construction drones to do overhead progress updates, are just a few ways an inventory manager can move construction industry progress and technology forward.
6. Job Costing & Reporting
Job costing is an important process, and describes the proactive steps taken to track the associated costs and revenue of a given project throughout its lifecycle.
With the job costing feature in One-Key, tool managers can calculate construction overhead and set daily and weekly rental rates as well as report out to financial stakeholders.
7. Smart Tools
Smart tools offer inventory managers many advantages, from standard tracking and security (like lockout), but also (on select models) advanced reporting (like on hydraulic tools and digital torque wrenches) and custom precision settings for trade-specific applications with repeatability and accuracy.
We’ve also integrated machine learning to prevent power tool kickback and keep tradespeople safe from kickback-related injuries.
Additionally, new-to-world technologies set us apart and put us in good company among world-recognized brands. Like the industry’s first motorized torque wrench, similar to the loom that made Toyota’s production system and solved wasteful activities by automating previously manual work, Milwaukee® was able to simplify a previously 2-step process—delivering 50% faster electrical installations—while also helping prevent repetitive motion injuries and digitizing the process in real-time to the cloud for installation reporting and quality assurance with proof-of-work.
Inventory Strategy Examples
Now, last but not least, here are some inventory management examples from real-world companies that should prove inspiring.
Toyota
Toyota pioneered what is now known as “Just-In-Time” manufacturing. “The philosophy of the complete elimination of all waste in pursuit of the most efficient methods […] has roots tracing back to Sakichi Toyoda's automatic loom,” Toyota Global’s website reads:
The automatic loom invented by Sakichi Toyoda not only automated work that used to be performed manually, but also built the capability to make judgments into the machine itself. By eliminating both defective products and the associated wasteful practices, Sakichi succeeded in rapidly improving both productivity and work efficiency.
Pictured Above: A Toyoda automatic loom, the innovative technological breakthrough that inspired Toyota's iconic "just-in-time" production system and lean manufacturing principles. Image Source: Wiki Commons
Apple
Apple is synonymous with Steve Jobs, but as Sean Ashcroft writing for Supply Chain Digital points out, Tim Cook, Jobs’ successor, is the “guru behind Apple’s growth.”
The year was 1998. As the story goes, Apple was struggling, on the brink of bankruptcy. Tim Cook, meanwhile, had already made a name for himself in the computer manufacturing industry as a heavy hitter, having worked at IBM for 12 years and holding executive roles at Intelligent Electronics and Compaq.
Inspired by Jobs’ vision for a product that would “shake up the computing world, a design that would be unlike any computer seen before,” Cook, against the advice of his friends and family, left his stable executive role at Compaq to join Apple.
Entering Apple and realizing its supply chain was unwieldy, Tim Cook he oversaw Apple’s shift to just-in-time manufacturing, a process he had previously done at IBM. Cook slashed Apple’s vendors down from 100 to 24, reducing the number of warehouses by half and establishing relationships with contract manufacturers.
Thanks to Cook’s contributions, Apple can now ship 72 million iPhones and is among the world’s biggest companies.
Amazon
Amazon grew from what seemed like a 90s pipe dream, when Jeff Bezos left his lucrative hedge fund job to sell books online, to the behemoth most of us are afraid of but yet can’t escape.
Part of Amazon’s warehouses’ successes are the symbiotic use of human and robot “pickers,” an example of how companies can use automation to streamline their operations.
Bottom Line
The construction industry, and pretty much any industry that relies on raw materials, is expected to see headwinds. How you respond to these headwinds and manage change is the only path forward. Above all, partnership and open communication between your team, as well as your customers, is key. What’s more, managing trust as a fundamental tenet to improving the customer experience is how you can set your business apart and overcome any unforeseen challenges.
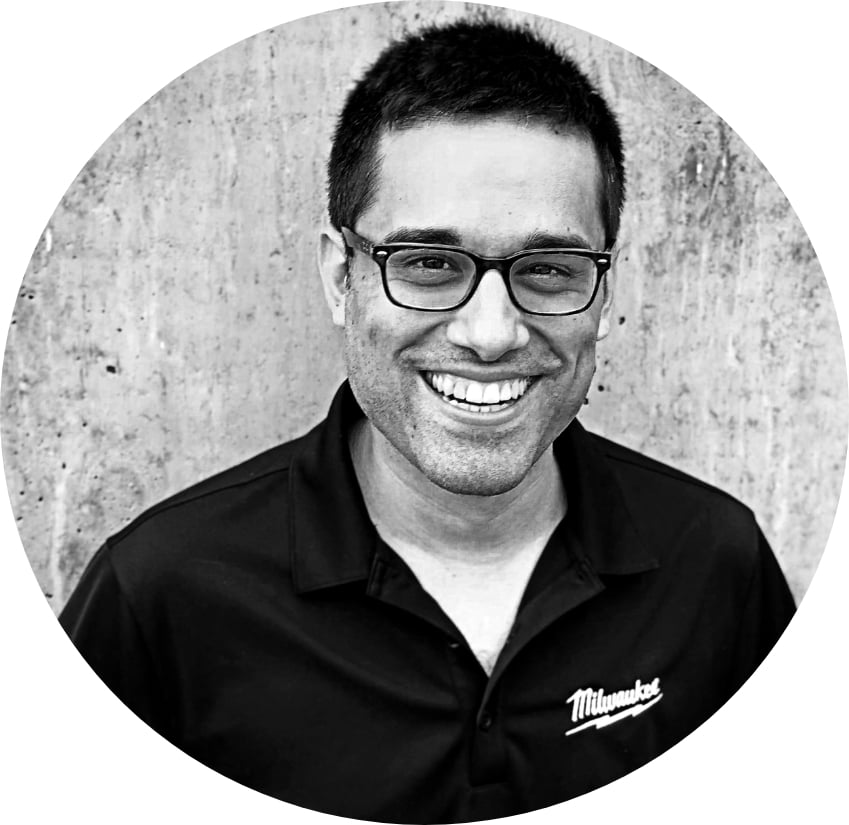
About the Author
Lucas is Content Marketing and SEO Manager for Milwaukee Tool, where he and his team raise awareness about the company’s digital products and educate users on best practices through a variety of content vehicles. More Content By Lucas MarshallSubscribe to Our Blog
Sign up to receive ONE-KEY™ news and updates.
Recent Articles
Essential Strategies for Balancing Work and Life in Construction
Editorial Note: This article was brought to you courtesy of Rose Morrison, managing editor of ...
Maximizing Efficiency: Do Roofing and Scaffolding Specialists Need Construction Software?
Editorial Note: This article was brought to you courtesy of Rose Morrison, managing editor of ...
11 Advancements Women in Construction Have Made So Far This Year
Editorial Note: This article was brought to you courtesy of Rose Morrison, managing editor of ...