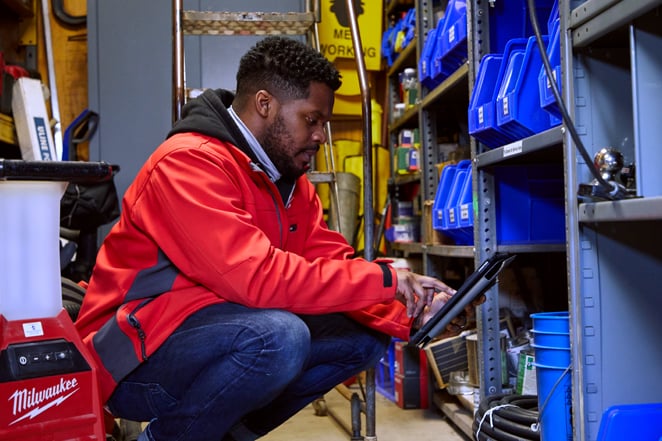
Construction is a logistics-heavy business. Every hammer and nail comes from somewhere, and that housing development project won’t get built unless everyone on the work crew has all the materials and equipment they need to get started.
It’s easy to take for granted, but tracking and managing every physical resource needed to complete any given project on time and within budget takes an enormous amount of careful planning and oversight.
Whether you’re a large enterprise construction company that employs a full-suite of cloud-based software or a small-to-medium owner, the need for an inventory specialist is real. That’s why an asset inventory manager or tool crib attendant is a much-needed hire.
And it’s an important one, among the tech-focused emerging careers in construction. Studies show that in large-scale construction, change orders account for 10-15% of a project’s total cost. What’s more, the National Equipment Register estimates that the construction industry loses between $300 million and $1 billion worth of equipment every year. It’s figures like these that keep inventory managers up at night.
Are there ways to manage resources to reduce those costly mistakes? Can we prevent the loss of expensive assets by keeping better track of them? What does this project need, when does it need it by, and which construction KPIs might be measured to judge the project's success or areas of opportunity? These are the questions that asset inventory managers and tool crib attendants get paid to answer.
Job Description: What Does an Asset Inventory Manager or Tool Crib Attendant Do?
Asset inventory managers (also known as tool crib managers or attendants depending on the organization and its structure) are the logisticians of the construction world. Working closely with construction managers, they craft strategies and processes for marshalling all the resources needed to successfully get a project to the finish line. You may be responsible for setting up a construction inventory or tool crib system to achieve these ends.
Related titles:
- Tool crib manager
- Crib manager
- Tool room manager/attendant
- Inventory management specialist
- Equipment manager
Inventory managers are responsible for directing the allocation, storage, and flow of all the physical assets needed for construction work—everything from building materials, tools, vehicles, and equipment. Without inventory managers, in other words, nothing would ever get done.
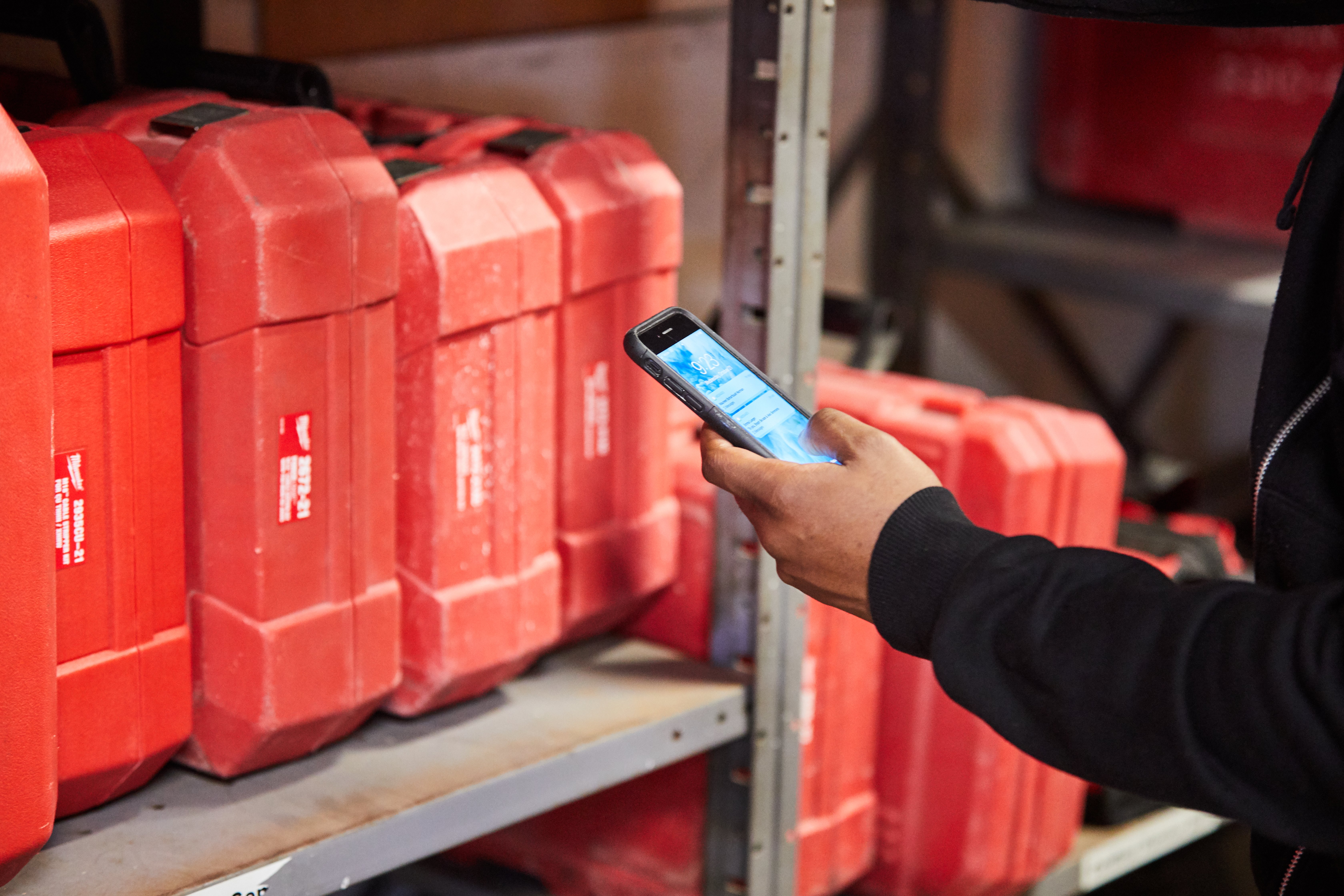
Much of the job of an inventory manager involves using a host of different digital tools and software suites that make the task of managing complex inventories and supply chains much easier. You may also work closely with a construction technologist, a role responsible for researching and implementing various technologies (ranging from cloud-based BIM software to prefab construction and modular construction methods). Whereas they will be in charge (and may likely consult with you) of researching and implementing various construction technologies, you will be in charge of using these technologies (among other things, cloud-based inventory management software, smart tools, tool and equipment tagging and small tool tracking products) to maintain visibility to your company’s inventory and improve its overall logistics chain so equipment-related job uptime is maximized.
Put simply, if you have a knack for computer technology, strong communication, and organizational skills, along with a highly adaptable frame of mind, then this might be the career for you.
We’ll go into greater detail on some of those in a moment. But for now, you’re probably wondering:
What’s the Salary and Job Outlook of an Asset Inventory Manager or Tool Crib Attendant?
According to the Bureau of Labor Statistics, the median annual salary for logisticians in the US is about $76,000. The field is expected to grow by about 4% over the next decade, which is on track with the projected average growth rate for all other occupations in the US. This, of course, does not tell the whole story, as salary information for construction inventory roles will vary widely depending on an organization’s size and internal structure. For example, if we drill down a little further into a given role, here are some of the salaries you might expect:
- The title “Inventory Manager,” for example, nets an average salary of $55,477, according to Payscale.
- Meanwhile, the title “Tool Crib Manager” on Glassdoor pulls in a nationwide average salary of $67,523, though this “average” ranges widely, with some individual companies paying an hourly rate of anywhere between $13 and $27 to an annual salary between around $25k and $40k on the lower end, and $92-100k on the higher end.
What Kind of Education and Skills Will Be Required as an Asset Inventory Manager?
Besides a high school diploma, there’s no concrete education requirement to become an inventory manager or a crib manager. It’s possible to pick up the skills and know-how needed to become an inventory manager throughout one’s experience in the workplace, whether that’s in construction or another setting. That said, many inventory managers do have some college education, either in the form of an Associate’s or Bachelor’s Degree in mathematics, finance, logistics, supply chain management, or business administration.
While also not strictly required, some companies will only hire candidates with some form of supply chain certification.
As for skills, inventory managers need to be strong communicators first and foremost. While strong communication is the kind of buzzword (and a soft skill) that gets thrown around a lot for any job, in this case it really is important. The timely flow of select materials and assets relies on how clearly, precisely, and congenially the inventory manager is able to communicate expectations with the various stakeholders involved. It’s not an exaggeration to say that success on a construction project is determined a great deal by the extent to which an inventory manager is able to speak to the various business partners positioned along the supply chain. Communication in this sense isn’t just a practical skill, it’s also a people skill, something that may not leap to mind as important when it comes to the work of construction.
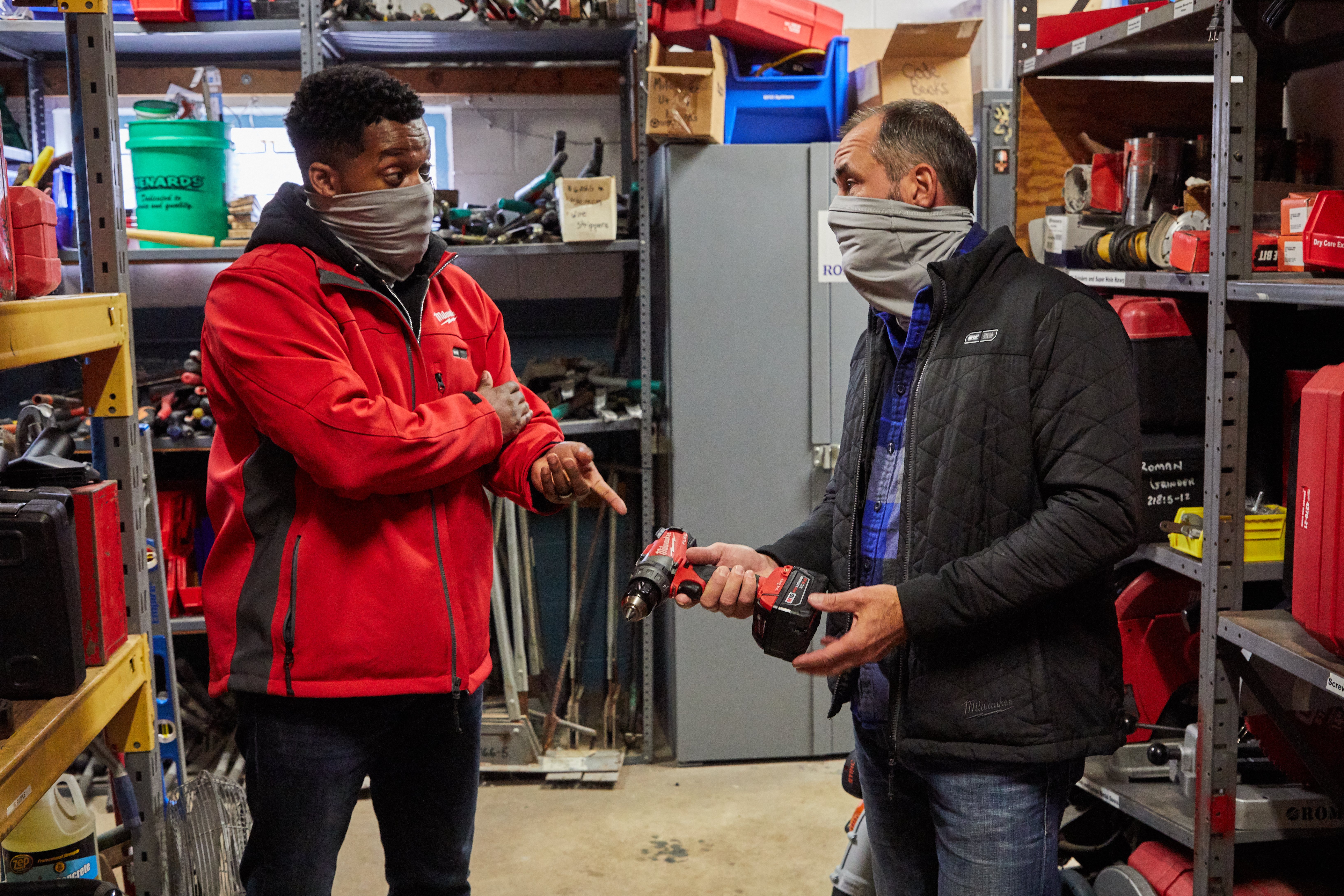
Inventory managers also need to be highly organized. And by this, we don’t mean that you absolutely must be strictly ordered in every aspect of your personal and work life; inventory managers don’t need a tidy desk or have their sock drawers color coordinated to qualify for the job. They do however need to be adept at keeping track of very expensive inventories. This means being well versed in logistics and the various digital tools available to manage and coordinate supply chains across different jobs.
Speaking of which, technology is absolutely key to the art of inventory management. There’s a lot of options to choose from these days, but pen and paper is not one of them—not at the speed and scale of modern construction projects. In a moment, we’ll take a deeper dive into a few different types of software that inventory managers should be familiar with. For now, it’s enough to say that a baseline of IT know-how is a must. If you’re allergic to computers, you may want to consider a different career path, or get inoculated fast.
Inventory managers also need to have a basic understanding of economics. We all know that the price of goods in capitalist societies rises and falls on fluctuations in local and global markets. A good inventory manager should be attuned to the market dynamics influencing those fluctuations so as to maximize cost savings today and anticipate economic—from the micro to the tectonic—that may otherwise be beneficial or harmful to a project tomorrow.
Last but not least, inventory managers need to be adaptable. No two jobs or supply chains are exactly the same. To stay in the flow, inventory managers need to be able to seamlessly weave from the slipstream of one project to the next.
What Kind of Software Does an Asset Inventory Manager or Tool Crib Attendant Use?
An inventory manager can’t keep eyes locked onto each and every resource under their care at all times. Even if this was somehow possible, the sheer scale of most supply chains is such that it would boggle the mind of the average person, like trying to pick out a single leaf among a cascade of many as it floats downstream and around the bend.
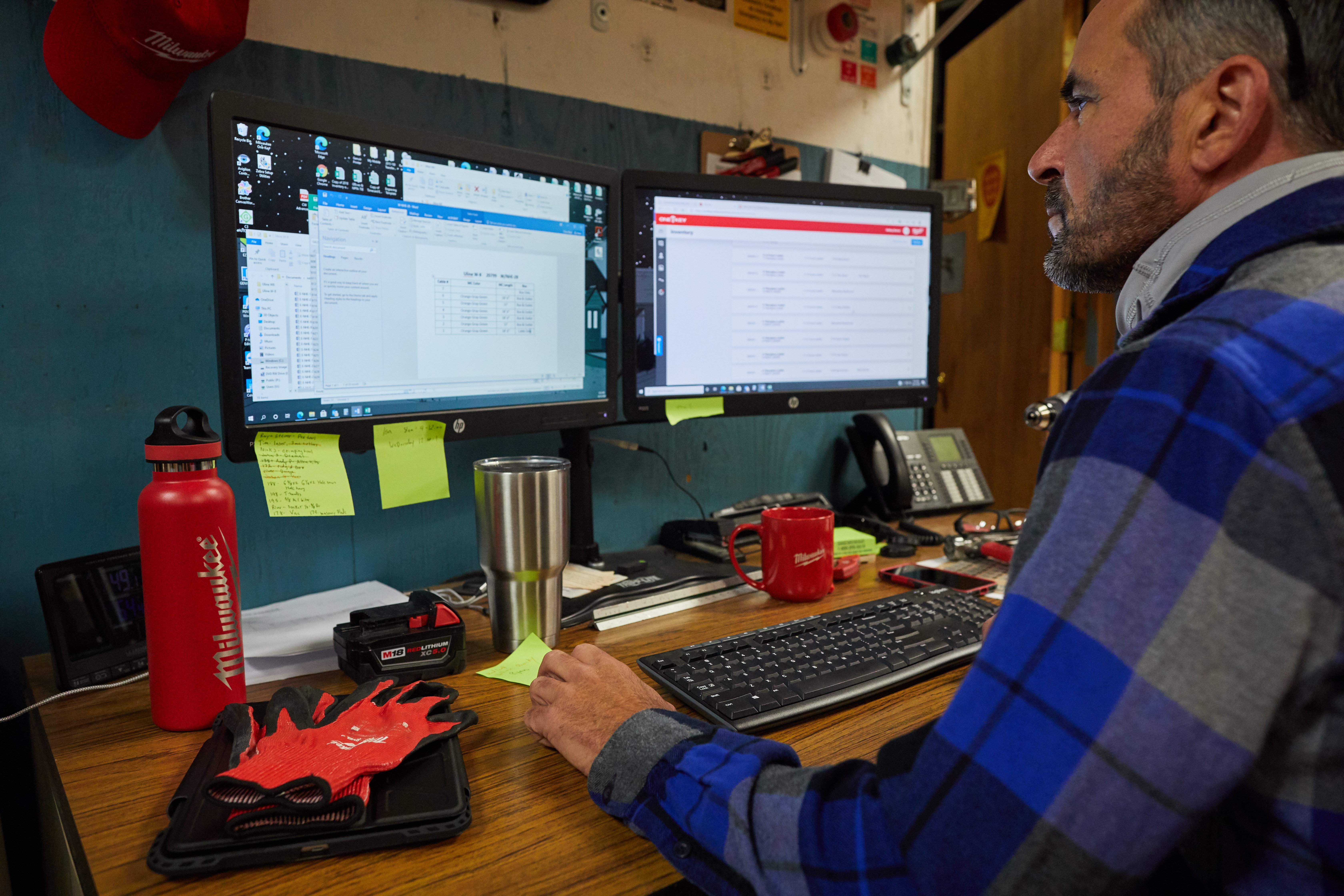
Inventory managers now have more tools than ever to help keep track of and make sense of all the moving parts on and off the jobsite. Let’s take a look at a few of the different types of software that inventory managers need to be familiar with:
Enterprise Resource Planning Software (ERPS)
This is a type of adaptive software used by both small and large-scale businesses to create workflows and manage all kinds of logistics. Of all the digital tools at an inventory manager’s disposal, ERPS is perhaps the most versatile. Enterprise resource planning software provides a customizable framework—based either on-site or in the cloud—capable of supporting a whole host of modular applications for monitoring everything from a business’ supply chain to finances and accounting. The appeal of ERP software for inventory managers is that it creates a single integrated platform where all the otherwise siloed-off elements of a construction project can come together to efficiently communicate and share mission critical data with each other. Besides construction, ERP software is used by many other large-scale industries like manufacturing, aerospace, defense, agribusiness, and healthcare.
Warehouse Management Software (WMS)
Warehouse management software is what inventory managers use to keep track of large inventories of physical material and equipment while idling in storage or in transit downstream to the jobsite. In construction, the purpose of WMS is to design, monitor, and in some cases automate processes that optimize the organization and flow of assets through each stage of a project’s life cycle. Warehouse management software cuts down on potentially costly errors, like the loss or theft of expensive equipment and raw materials. A good WMS program can be run on-site, in the cloud, on its own, or as a module in an ERPS platform.
Supply Chain Management Software (TMS)
Whereas WMS is used for organizing and sorting already cached materials, SCMS is used to keep track of the supply chains through which those materials are first acquired. Supply chain management software helps inventory managers craft procurement strategies, maintain oversight on the sources of materials, and keep track of the important business relationships that make up each link in the supply chain. Run on-site or in the cloud, SCM software is an invaluable tool for making smart choices upstream that will pay dividends in the overall cost and efficiency of a construction project.
The lines between these digital tools can be blurry. It’s possible for instance to have WMS and SCMS applications that run as modules on a larger ERPS platform (there are advantages and disadvantages to this route for those who want to wade into the weeds). For that matter, certain types of SCMS may incorporate WMS capabilities, and vice versa. What specific kinds of software an inventory manager uses may depend on personal affinity, the company they work for, or the demands of a particular project.
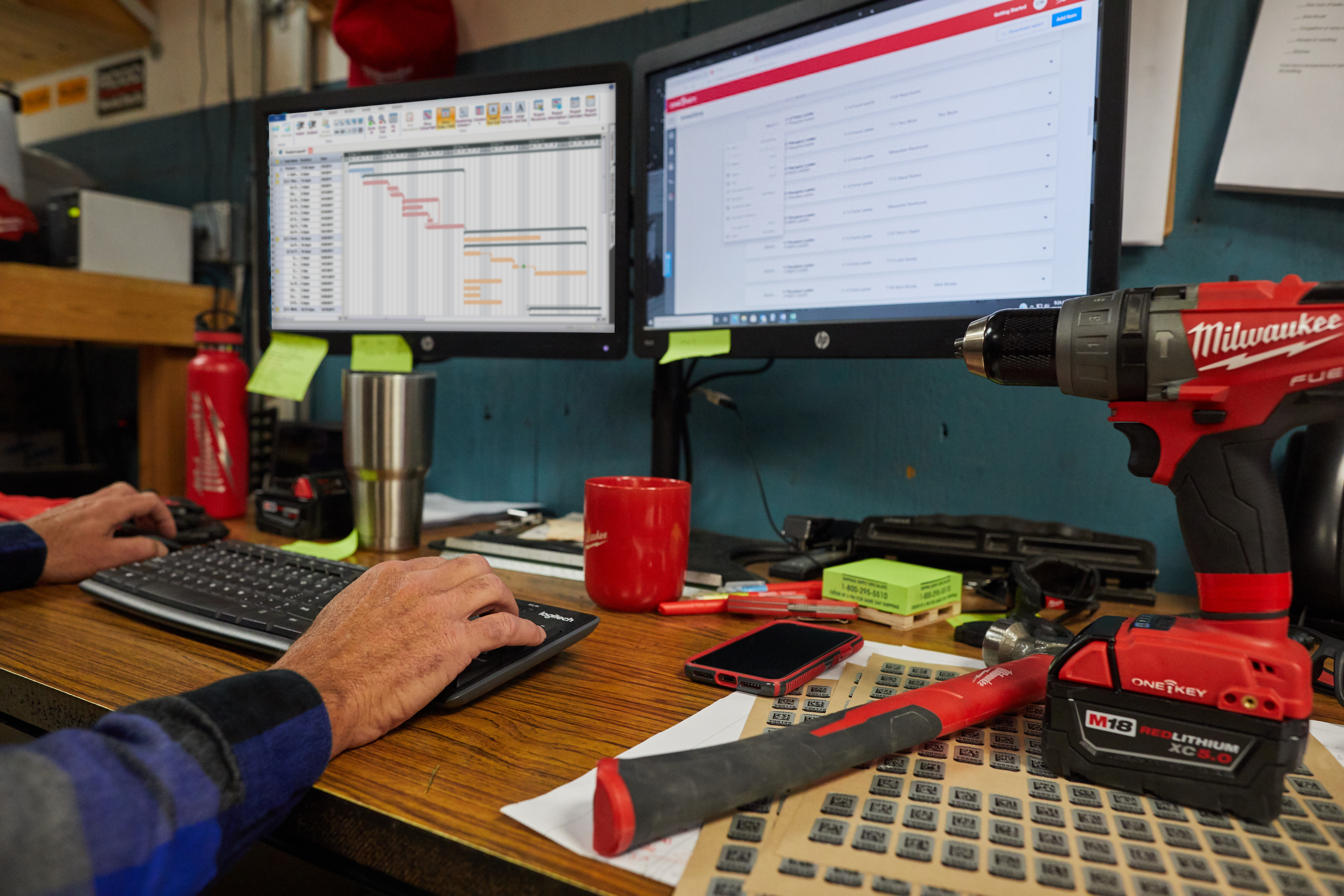
The takeaway for our purposes however is that an inventory manager needs to be adept at using a variety of digital tools to optimize processes, track materials, and fine-tune the flow of assets from the supply chain to the construction site.
What’s the Future of Construction Inventory Management?
Now that you’ve been bombarded with acronyms, here’s one more to round things out:
RTLS, which is short for real-time location systems.
We’ve already described several powerful digital tools that are excellent at providing a birds-eye view of complex inventories and supply chains. But they’re largely limited to capturing the picture in broad strokes. Warehouse management software, for instance, is not able to reliably track the moment-to-moment movements of inventory items.
But guess what can? That’s right. Real-time location systems are capable of providing the user with automatic and highly accurate updates on the changing physical whereabouts of individual assets as they move from storage to the jobsite and beyond. A prime example of an RLTS is Milwaukee’s own ONE‑KEY™ inventory management platform, which uses Bluetooth Low Energy (BLE) to keep close track of tools and equipment, cutting down on costly losses and theft.
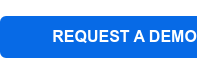
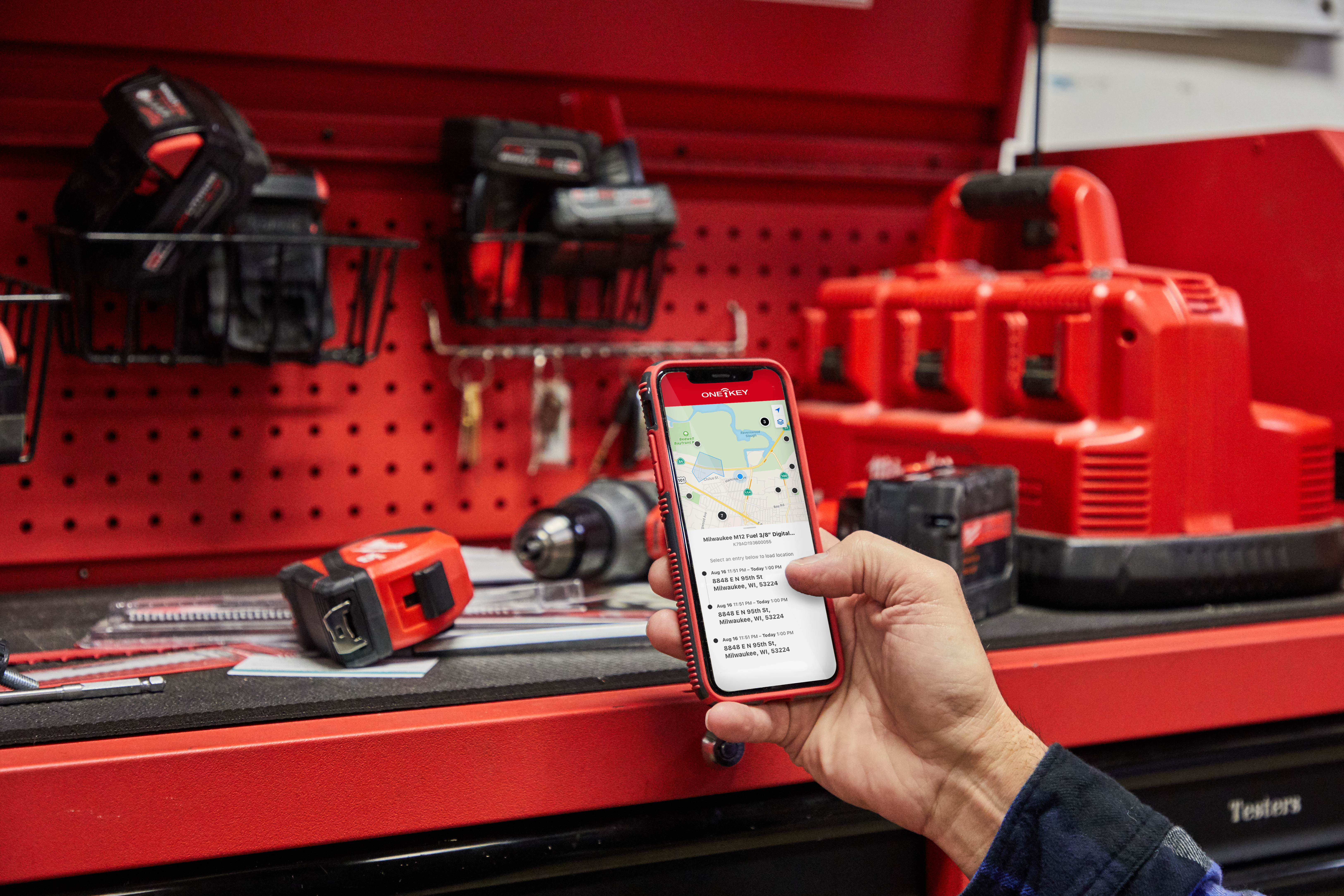
While real-time location systems are no replacement for a tricked out ERPS platform, they can, however, sharpen an inventory manager’s already keen understanding of the big picture that’s constantly unfolding around them.
Construction is a logistics heavy business. Every hammer and nail comes from somewhere. In today’s exploding global market, knowing how to build and maintain the best supply chains is a full-time job in itself. And as inventory management technology continues to grow more sophisticated in the coming years, so too will the demand for the expertise to use it.