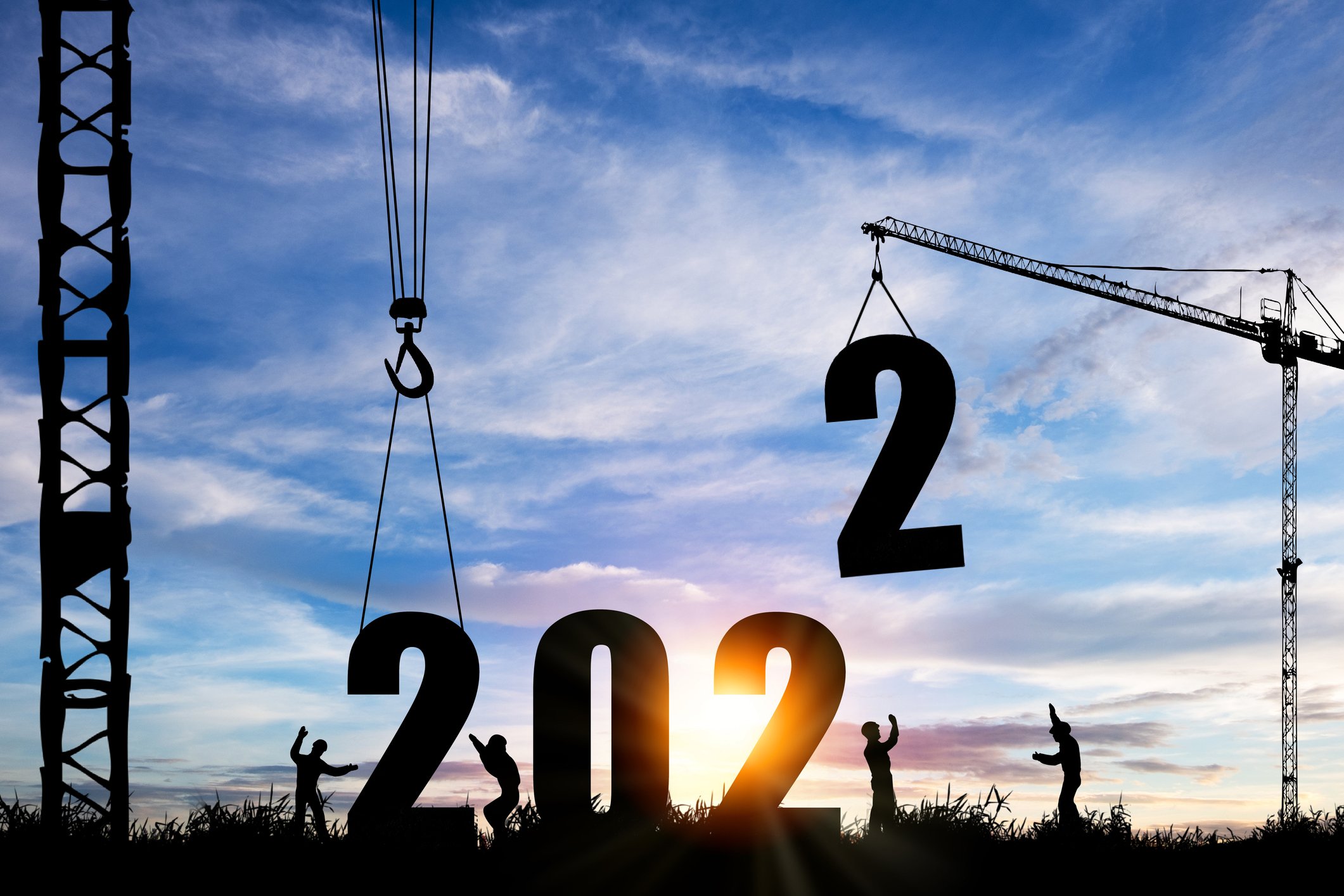
2022 is officially here, and from all of us on the ONE-KEY™ team at Milwaukee® Tool, we wish you a happy New Year! With the start of each year, it’s common practice to commit to realistic, achievable New Year’s Resolutions; these commitments allow you to look inward to find opportunities for growth and promote a continuous improvement mindset.
What better time is there than the new year to hit the ground running with a streamlined approach to inventory?
In this article, we’ll outline best practices in inventory management, including hardware and recent One-Key software features that can be used in conjunction to promote orderly tool and equipment tracking and management.
What Are the Best Practices of Inventory?
Good inventory management combines organizational skills, pragmatic planning, and a set of tools (we’ll discuss these a little later) that empower a nimble tool room manager to respond to changes with rapid-fire response times.
Here are 3 major inventory management techniques to keep in mind for 2022:
- Optimize your pick & pack process
- Establish your inventory management KPIs
- Secure safety stock
Let’s dive a little deeper into each of these techniques, shall we?
1. Optimize Pick & Pack Process
Creating order from chaos in your inventory starts with simplifying the steps involved with picking inventory off the shelves, packing them up, and shipping them off to the job.
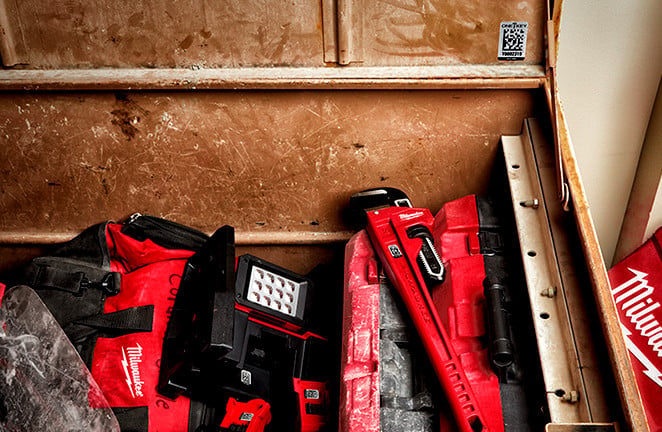
Consider, for a moment, how Amazon has created a “symphony of automation robots and warehouse workers in order to streamline their logistics network and perpetually improve expectations.” Complete with tracking numbers that give online shoppers updates from when their shipment leaves the warehouse to when it’s dropped on their doorstep, these ecommerce optimizations are necessary to deliver 1-day shipping and the positive experience we’ve come to expect.
How can you create a symphony from the tool room to the jobsite and back?
- Optimize storage space and label shelving: It’s important to have a sensible order and organization to how you store inventory in the tool room. How are you storing your tools and equipment? As with the Amazon example, it’s all about optimizing space; organizing where tools are stored in the warehouse and on which shelf based on tool type is a given; add shelving labels that are large and legible enough to read from a distance. Consider, for example, how a Home Depot in your area not only have items grouped by product type, but also how each product category is adorned by a huge sign—e.g., “Electrical,” “Plumbing,” “Hardware,” “Tools,” “Lumber,” etc.
- Optimize your “in-flight” equipment tracking experience: With the One-Key app, we’ve developed tracking hardware and integrative software to assist in creating a comprehensive tracking experience, tracing inventory from the crib to the field and back. Consider, for example, barcoding or applying an asset ID tag to each of your inventory items; then, once you’ve tagged everything you’re sending to the job, add them to a PACKOUT™ and group each item in your PACKOUT in a “tool kit” within the app. This allows you to send everything to the job at once. A Bluetooth® Tracking Tag, or a GPS tracker, can be added to your PACKOUT for greater tracking capacity to ensure the whereabouts of bulk send is more easily visualized in real-time. Once your kit is received at the job, your field ops team can verify what’s on hand and ensure everything is returned with an audit. If they find, at the end of a workday, that an item is missing, if it’s a One-Key compatible tool, they can scan for it nearby—or if a Bluetooth Tracking Tag has been attached to it, they can ring it from the app to see if they can hear it nearby.
2. Establish KPIs
Once you’ve streamlined your pick and pack process, as above, it’s important to start tracking important inventory-related key performance indicators (KPIs) as a way to baseline how your tool team is doing, and where you can improve.
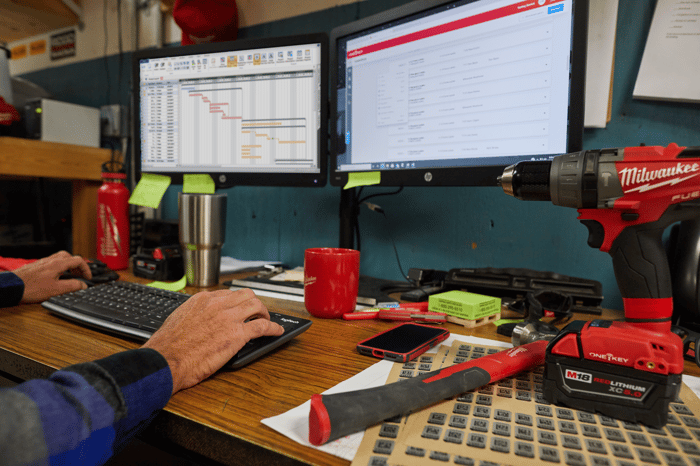
Examples include:
- Asset turnover: How much inventory is working to generate revenue. To optimize tool utilization and limit turnover and equipment failure, consider investing in smart power tools from which utilization data can be accessed to verify whether tools are performing to spec, set service reminders, and be alerted prior to equipment failure.
- Labor utilization: How efficiently your workforce is using your inventory dollars. Similarly as above, M12 FUEL™ innovations like our 1/2" and 3/8” Digital Torque Wrench w/ One-Key can make your team work more efficiently, helping electrical contractors install fasteners 50% faster with accuracy within 2% for torque critical fasteners. Plus, you can generate torque reports to verify a job well done.
- Return on assets: How inventory is working to generate profit.
- Washout percentage: How much money you have to spend sustaining your inventory.
- Fleet age: Average age of the asset or category of asset. Guide: determine whether you should repair or replace tools to help prevent equipment breakdowns.
- Order lead time: How much time it takes from receipt of an order to delivery. As we mentioned about optimizing your pick & pack processes above, determine how your team’s order lead time compares to your baseline performance, prior to streamlining, to decide whether additional optimizations need to be made.
3. Secure Safety Stock
Finally, it’s important to load your inventory shelves with ample safety stock to ensure you’ve got reserves for a rainy day.
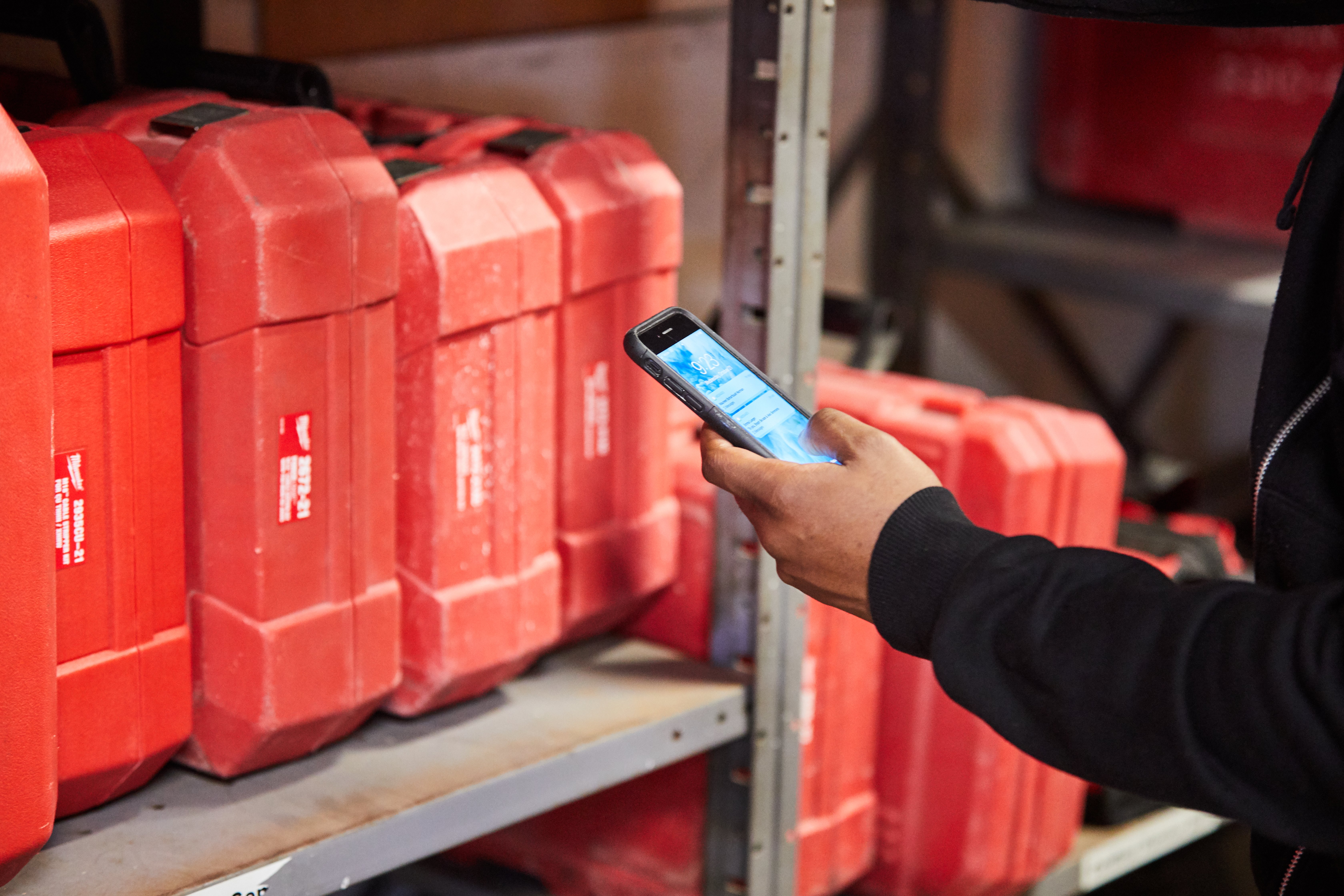
After all, downtime in construction equates to 80 wasted minutes per day caused by contractors waiting around for materials to arrive. Inventory-related lapses in productivity can be partially averted by ensuring you’ve got enough equipment in your fleet to quickly replace items that unexpectedly disappear, breakdown, or end up on the wrong job. Combining ample inventory with an optimized logistics chain, as we discussed above, can help make those downtime incidents far more preventable.
Use a Cloud-Based Inventory Management App to Create an Equipment Ecosystem
As we’ve previously discussed, there are some clear advantages to digitizing your inventory and backing it up to the cloud.
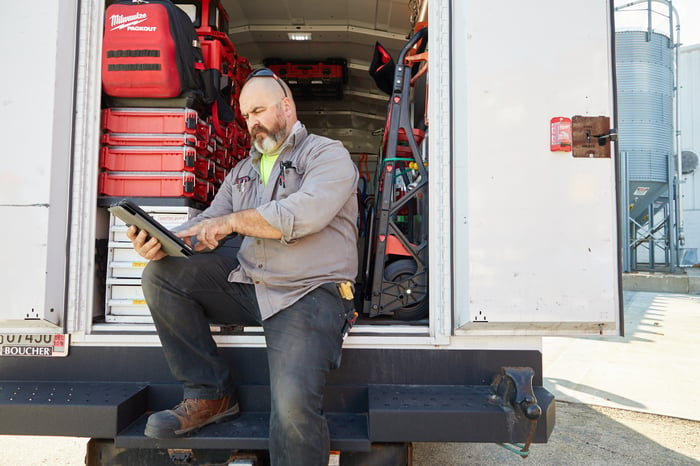
To reiterate, some advantages of a cloud-based inventory system include:
- You can easily access it when you need it, wherever you are, on any device (iPhone, Android-based smartphones, tablet devices, laptops, desktop computers), and give you piece of mind that your changes will sync automatically so you don’t have to worry about finding the right file later.
- Cloud-based apps like One-Key provide contractors unmatched access; with our free inventory management app, you’re capable of storing important documentation, setting important service intervals to remind you and prevent equipment failures, and so much more. Learn more about One-Key inventory management.
- You can leverage data through a broadened ecosystem of software integrations, API, and technology pilot programs.
- Unbeatable construction tool and equipment tracking solution with our industry-leading Bluetooth tracking community, which delivers millions of location updates per day; software features like geofencing and enhanced item locating functionality to help see when items wander or troubleshoot finding items within your vicinity, respectively; best-in-class tracking hardware products that seamlessly interact with the app, like our Bluetooth Tracking Tag (discussed above).
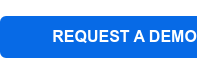
New to Bluetooth® tracking? Learn how community Bluetooth tracking works. Learn the differences between Bluetooth and GPS tracking, as well as the differences between Tracking Tags, Asset ID Tags, and TICK™.
Tips for Managing Your Digital Inventory in 2022
If you’re new to inventory management in the cloud, and One-Key in particular, we recommend learning how to get started with the One-Key app.
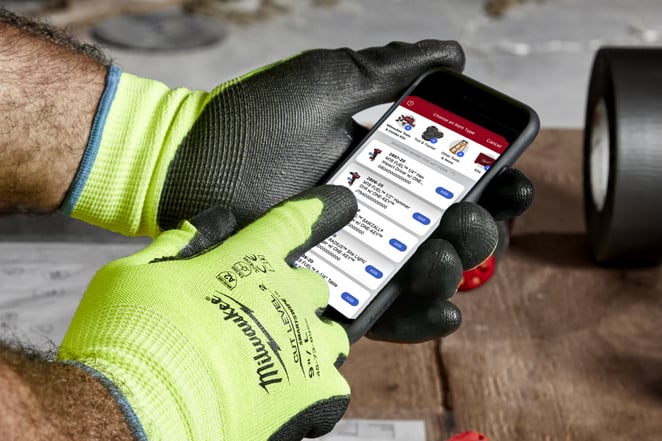
If it’s not your first rodeo, we’ve got two tips for you:
- Have you added your new tools to inventory? If you’ve purchased a new One-Key compatible tool or received one over the holidays, we cannot stress enough the importance of adding your item to inventory. Learn how to add a One-Key compatible tool to inventory on Android and iOS. Additionally, ensure Location Services and Bluetooth are enabled. This will ensure that, should your tool be misplaced, you’re able to receive location updates via the app, and that we can verify the tool belongs to you should it get stolen. Have a Milwaukee® Tool without One-Key or a tool from another manufacturer? Learn how to add other Milwaukee brand tools on Android and iOS. Learn how to add tools and equipment from other manufacturers on Android or iOS. Add one of our asset ID tags or Bluetooth tracking tags to keep an eye on these items (asset ID tags; Bluetooth tracking tags).
- Create order by cleaning up inventory data: It’s always easier on you in the long run when you create consistency with naming your items across your items at initial upload. For example, if you add “M18 FUEL 1/2 Hammer Drill,” ensure each additional item of this kind is named the same way, rather than “Hammer Drill,” “1/2 Hammer Drill,” etc. This ensures unassigned and misnamed inventory items don’t become lost in a crowded inventory, harder to find with each unique search parameter. You can avoid this when initially adding inventory by adding many items of the same kind via our bulk uploader tool, then add additional items of the same kind, later on, from an existing entry in your inventory. If the damage is already done, we recommend spending a slow afternoon scrubbing your inventory (or better yet, assign this task to an apprentice!) for slight variations. If there are quite a few of them, you can revert them to your preferred naming convention in bulk; learn how on Android or iOS.
Finally, here's a bonus gift! We've begun adding mood music to a 2022 Inventory Playlist on Spotify to help you get inspired and hit the ground running with managing your inventory this year.