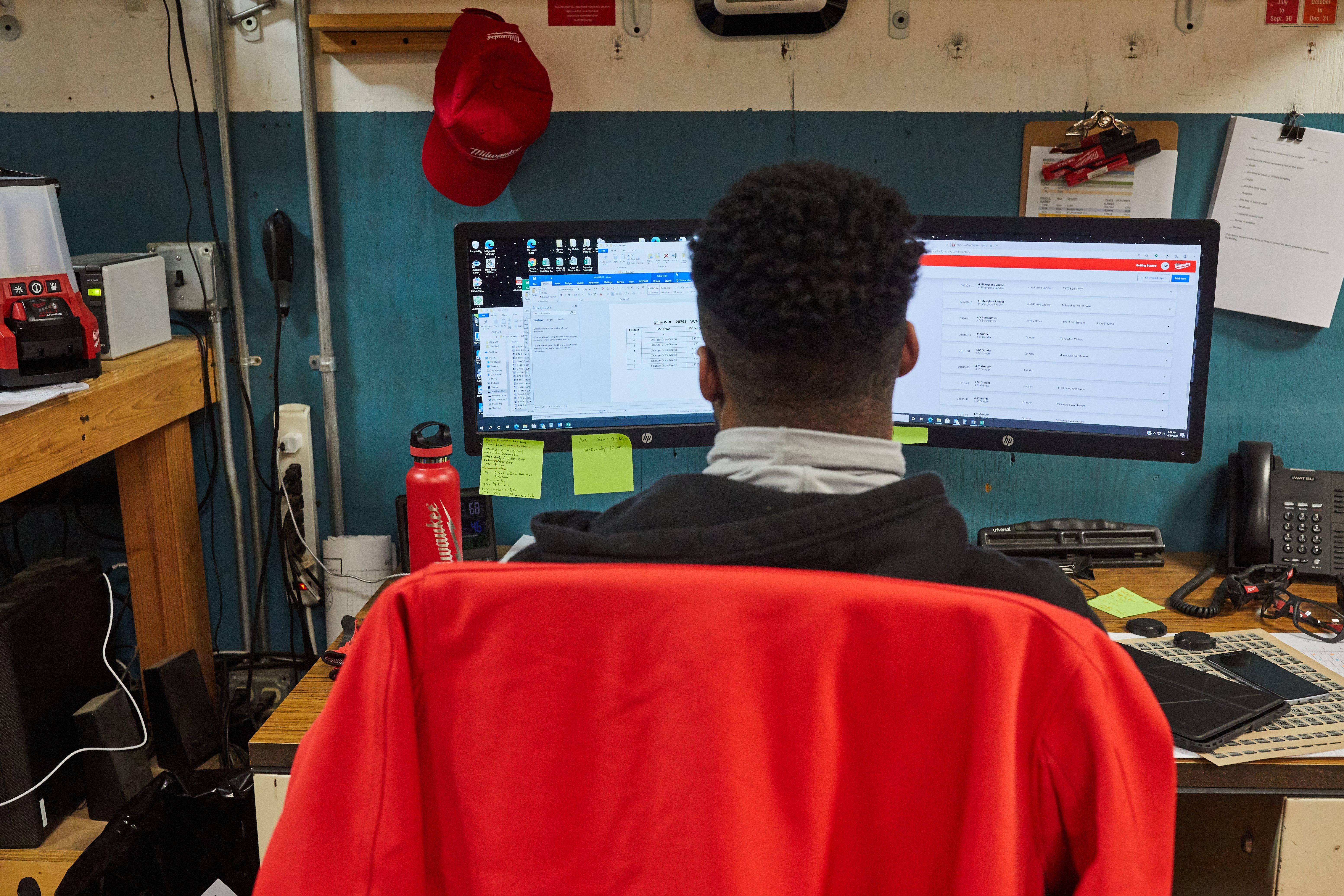
Did you know that, on average, contractors spend 80 minutes a day waiting for materials to arrive? Or that 45% of construction professionals report spending more time than expected on non-optimal activities, with 35% of their time reportedly spent on non-productive activities. That’s over 14 hours per week!
In inventory management, we define “non-productive” activities as things like figuring out where a tool is when it’s not where it’s supposed to be, fixing duplicate entries, etc.—pretty much anything that consumes a contractor’s time that could be better used laying down a subfloor, putting in drywall, securing ductwork, installing an electrical panel, putting in plumbing, and so forth.
These activities, in the moment, are aggravating, but they’re also exceedingly expensive, costing the US construction industry over $177 billion in labor costs in 2018 alone. Construction downtime remains a serious problem that can lead to timeline interruptions, a lot of customer frustration, and, in many cases (upward of 9 out of 10 projects!), unsavory project overruns that negatively affect your bottom line and threaten your ability to bid for and win projects.
In short: Downtime, unaddressed, threatens your organization’s very survival.
So, how do we combat downtime?
Aside from strategic planning that feeds into your team’s roadmap, the digital tools and technology you use to foster collaboration among clients, and break down silos between cross-functional teams, are essential.
Digitizing inventory practices, considering the above-mentioned financial burdens, is of utmost importance, especially when we reflect for example that, from 2018-2019, subcontractor dependance on spreadsheets decreased a measly 1%, according to a JB Knowledge report.
That’s a problem.
Because let’s face it: When it comes to construction management, particularly with regard to inventory, the old ways of pen and paper won’t cut it anymore, especially as labor shortages have become so prevalent. Fewer bodies mean more opportunity for mistakes to be made. 52% of rework, in fact, is reportedly caused by poor project data and miscommunication.
However, a good strategy for inventory can help solve labor shortage problems, helping you empower even the smallest (but mightiest) tool teams to master their logistics chain and make your projects run more smoothly.
And it all starts with piloting a great inventory app. What makes an inventory great?
Attributes of a Highly Usable Construction Inventory App
There are multiple factors that make an inventory app worth piloting. As a simple starting point, you might ask yourself, “Is this app an improvement to what we’re doing now, and how?”
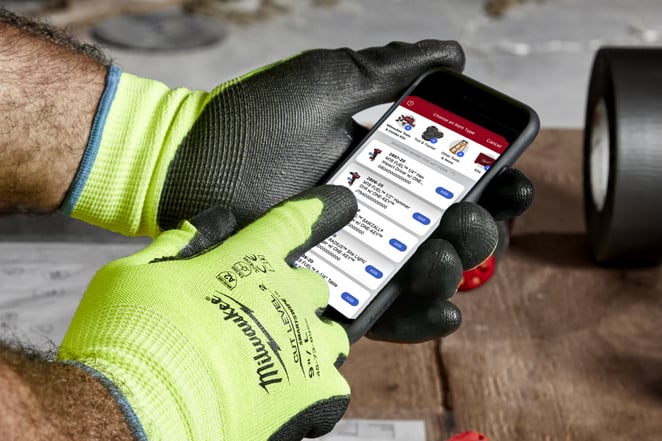
Consider the various features and value-adds that make it better than using manual processes or outdated, legacy software packages that are sluggish, incompatible, or worse, pose a cybersecurity risk.
- Cloud-based: Can you back your stuff up to the cloud so you can easily access it when you need it instead of frantically rifling through binders or computer files? When you make changes, do they sync automatically so you don’t have to worry about finding the right file? Can you make bulk changes to items of the same type across large inventories to help streamline inventory cleanup?
- Unmatched access: Is the app simple to use and, importantly, can you access your inventory from your web browser, as well as your mobile devices like an iPad, or on your Android or iOS smartphone? Does it require expensive hardware, like barcode scanners, or does it have built-in barcode scanning functionality that uses, for example, your device’s built-in camera to save you from these expensive upfront and maintenance costs?
- Robust tracking capabilities: Can you integrate various methods of keeping track of small tools as well as tagging valuable equipment into the app: e.g., equipment tags and barcodes, Bluetooth trackers and tags, GPS trackers, etc.
- Data and software inoperability: Does the app offer an integration with other teams’ software applications or the ability to build one?
Another worthy consideration is cost. Many legacy inventory software programs incur expensive licensing fees in the thousands of dollars each year, which (what’s worse) multiply with additional seats you’ll likely want in order to grant access to multiple team members and keep, at minimum, the people that are on a need-to-know basis in the loop.
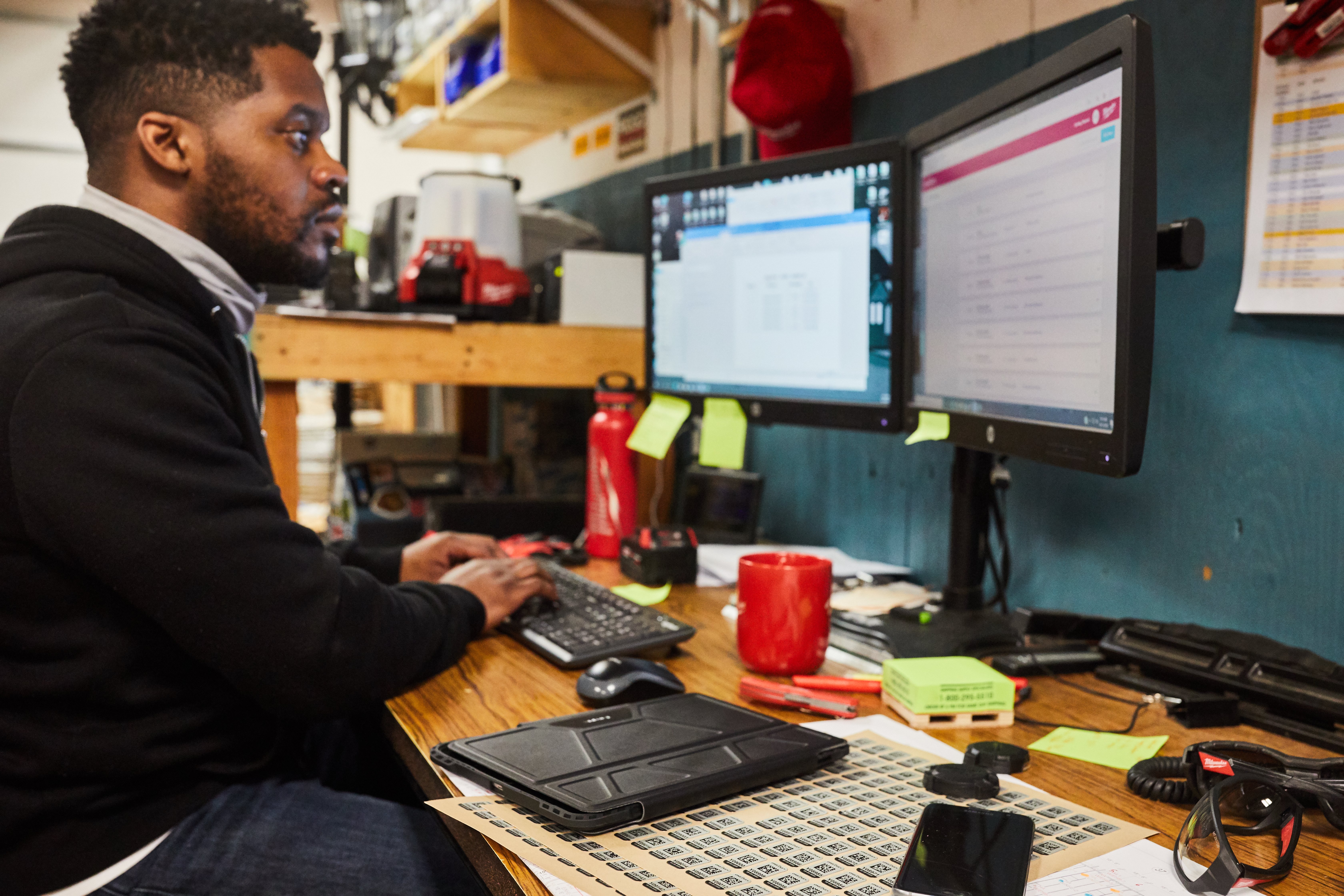
That’s one of the reasons we continue to develop One-Key as a free inventory app, providing incredible value and accessibility to teams who want to not only digitize and track their inventories, but also to delve into data insights regarding their equipment that will help them be more productive.
What Is Milwaukee® Tool Doing to Build the Connected Jobsite?
Now that I’ve shared with you the above-mentioned basic tenets that make a highly usable inventory app, I’d like to use the back-half of this article to share 4 fundamental pillars we use when developing the ONE-KEY™ inventory app, in order to:
- share our approach to software development
- shed some light on why we develop features the way we do
- explain how our app fits within the landscape of inventory management
Defining Our Process
What is our process to developing the One-Key app and comping up with new features?
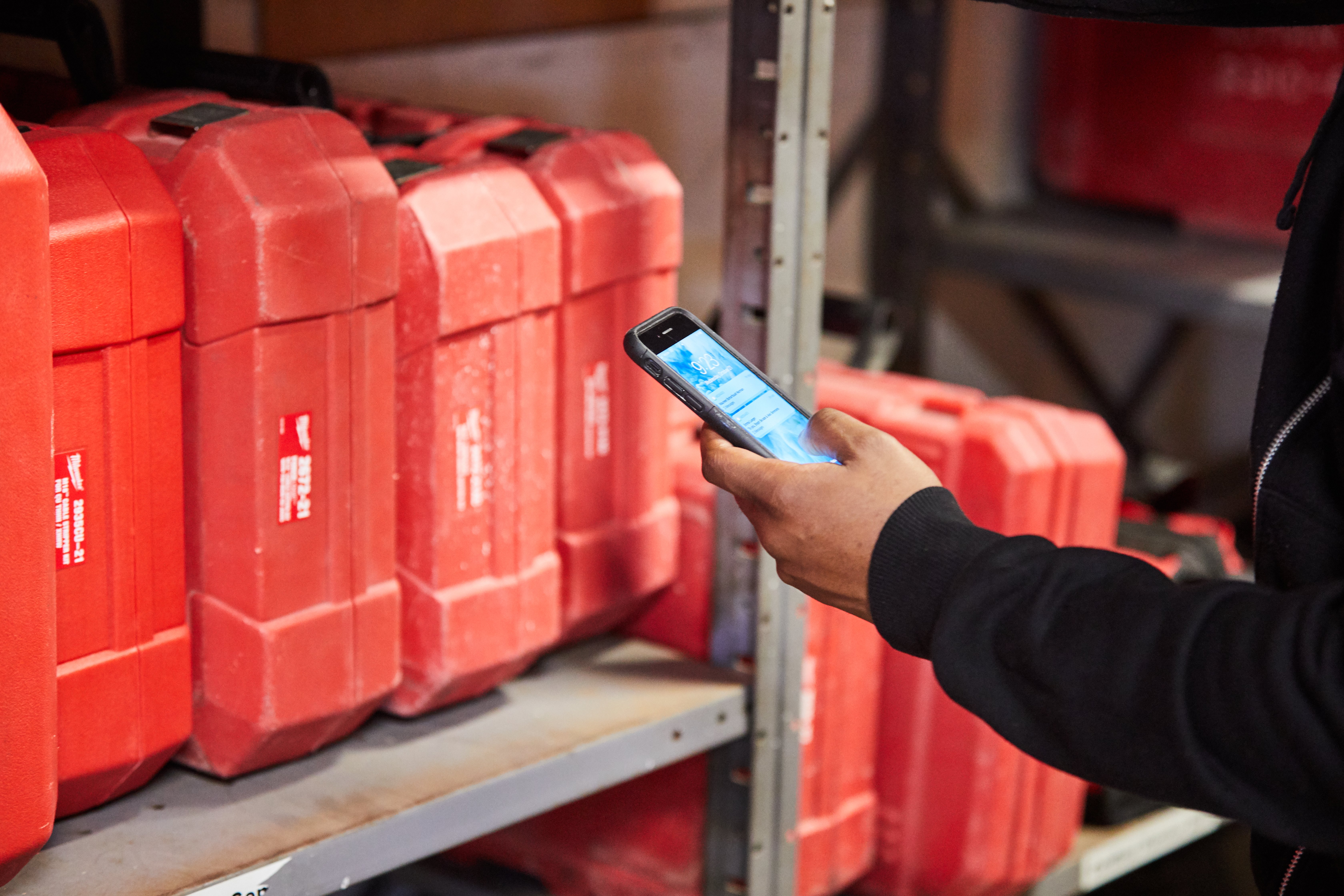
It works twofold:
- Our product management and user experience research teams partner with end users to determine pain points, needs, and opportunities for improvement. This is how features like multi-user admin and tool kitting are identified, put into development, and deployed through additional beta testing to ensure we’re able to tweak functionality to best suit our end users’ needs.
- Meanwhile, our in-house construction technologists research and investigate emerging technology, like construction automation; offsite construction topics like prefab and modular construction; sustainable construction; wearable tech and safety solutions; building information modeling; and so much more. Then, we collaborate with end users and trade orgs in order to drive innovations we put into our products. These innovations drive our solutions that help improve end users’ ability to complete tasks safely and streamline their processes and workflows, making them more productive.
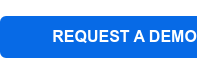
One-Key System Approach: 4 Fundamental Pillars
Similar to the 4 attributes we discussed above that qualify a highly useable inventory app, at Milwaukee Tool we develop One-Key with 4 fundamental pillars:
- Connected Tools & Devices
- Tool & Equipment Tagging & Tracking
- Accessible Software
- Data & Integrations
By focusing on these 4 fundamental pillars, we’re able to deliver unique value:
- Robust inventory management feature set
- Field-to-back office enablement
- Real-time access to data and insights
- Industry’s largest repository of things that end up on a jobsite
Let’s dive into each of these a little bit deeper.
1. Connected Tools & Devices (Professional Tools of Trades)
At Milwaukee Tool, we’re dedicated to helping make you more productive, evidenced with disruptive innovations across our M12™, M18™, and MX FUEL™ battery platforms; but just as we’ve disrupted the corded power tool market with heavy-duty cordless power tools that deliver even more performance, we’re invested in making the now “cordless” job one that is seamlessly interconnected.
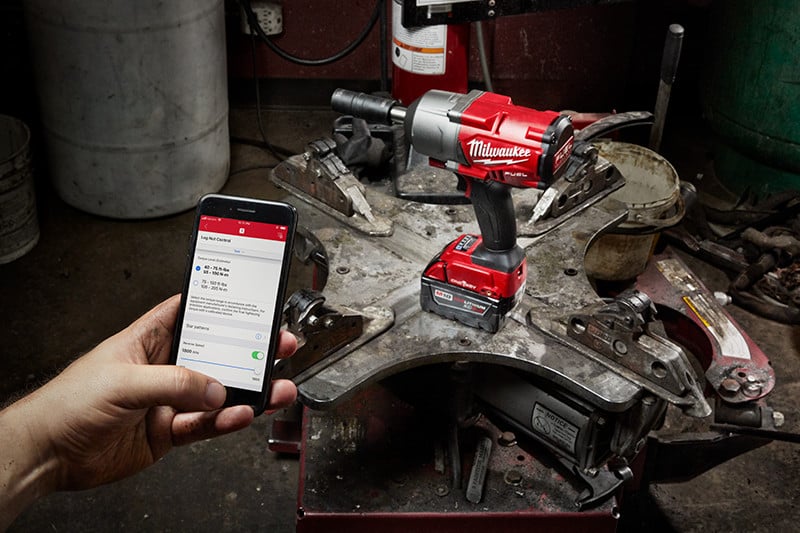
We lead the industry with over 56 compatible smart tools, a list that is continually growing (just wait until you see our roadmap for 2022!).
These connected smart tools offer numerous advantages:
- Dial in performance: You can perform tasks more safely and to spec with task-specific torque targets or optimized for a specific job (like blade, drill bit, and material selection). You can even use the mode library to virtually create endless tool customization options.
- Access tool utilization data: The days of struggling to diagnose issues is in the past, thanks to the copious amounts of data at your fingertips. You can inspect how a tool is performing and know when something is amiss; what’s more, service reminders can be programmed so you’ll be reminded when your tool is due for maintenance.
- Controls for safer use: We’re able integrate smart tech into our power tools to make them safer. Features like anti-kickback control on our drills and impacts, and cut brake on our saws, help prevent injury to user and damage to materials. Tool lockout allows for keeping expensive power tools free from tampering and shut down afterhours.
2. Tool Tracking
Keeping track of your stuff is a mission-critical part of keeping your construction projects on track and your business afloat. In fact, 50% or more impact on productivity is a result of issues with construction logistics, according to MCAA.
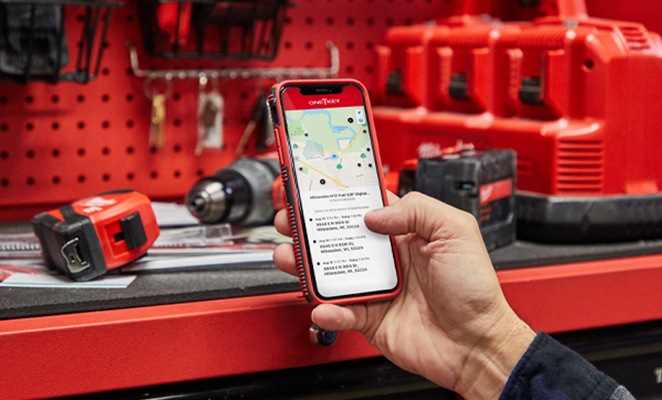
Since the launch of One-Key back in 2015, we’ve progressively developed its feature set and took steps to grow our network in order to make it as robust as possible.
The result:
- We maintain the construction industry’s largest tracking network, delivering millions of location updates per day; more tracking updates, that is, than all of our industry competitors combined!
- We’ve developed unique software features like geofencing and enhanced item locating functionality to help see when items wander or troubleshoot finding items within your vicinity, respectively.
- We continue to research and develop best-in-class tracking hardware products that seamlessly interact with the app.
New to Bluetooth® tracking? Learn how community Bluetooth tracking works. Learn the differences between Bluetooth and GPS tracking.
3. Construction Inventory Software, Accessible from Anywhere
One-Key can be accessed from anywhere.
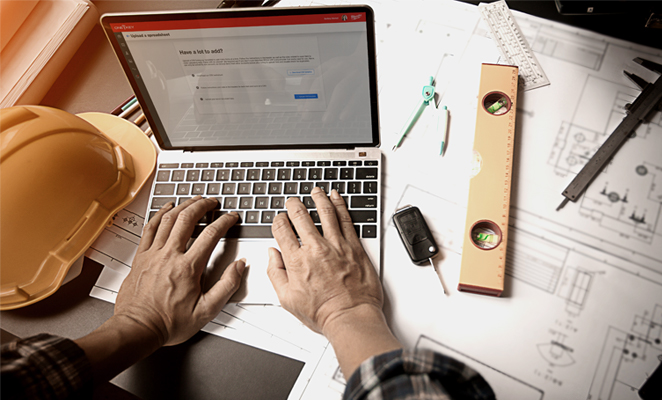
What does that mean?
To start, you can:
On top of this, we develop One-Key specifically for the busy professional contractor with biweekly updates. Unlike some of our competitors who may offer an update once a year or once every 6 months, we practice an agile software methodology, dedicated to getting our features into the hands of real end users as well as continuous improvement to perfect these features for you.
4. Construction Data & Integrations
Finally, on top of creating a highly usable product, we’re also always looking to leverage data in ways that provide value to end users.
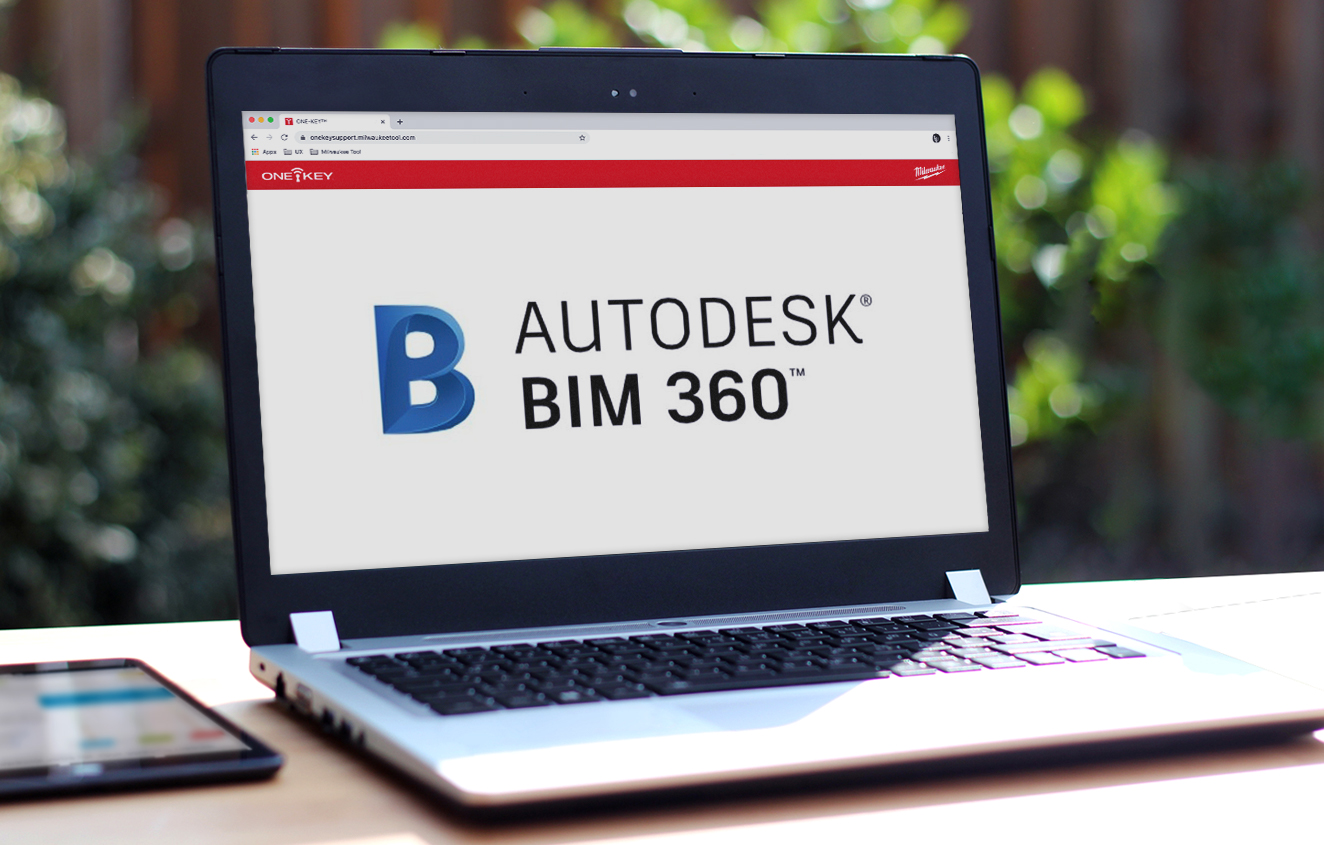
In short, we aim to:
- Broaden our connected ecosystem through integrations with industry leaders that help provide end user value by reducing manual inputs and errors, and synchronizing data.
- Enhance product solutions through deeper integrations with leaders and developing our open API in order to, for example, streamline workflows on the jobsite and complete install confidence.
- Innovative technology partnerships through our open API and pilot programs with contractors.
Bottom Line
According to a report, within 10 years, full-scale digitization could lead to savings between $0.7-1.2 trillion (13- 21%) in the design, engineering, and construction, as well as $0.3-0.5 trillion (10-17%) in the operations.
What’s more, despite being among the least digitized industries, in 2019, the USG + US Chamber of Commercial Construction Index found that 70% of contractors believe advanced technologies can improve productivity, schedule, and enhance safety.
The tides are changing.
And there is tangible value to digitizing the built world. In an industry rife with labor shortages, costly overruns and mistakes leading to even costlier rework loom. But through digitization, data-insights can help empower. Knowledge is power!
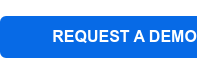
Wrapping up: the 4 attributes that make an inventory app great that we discussed include, generally that it:
- Is cloud-based
- Provides unmatched access
- Provides robust tracking capabilities
- Provides data and software inoperability
The 4 fundamental pillars of One-Key:
- Connected Tools & Devices
- Tool & Equipment Tagging & Tracking
- Accessible Software
- Data & Integrations