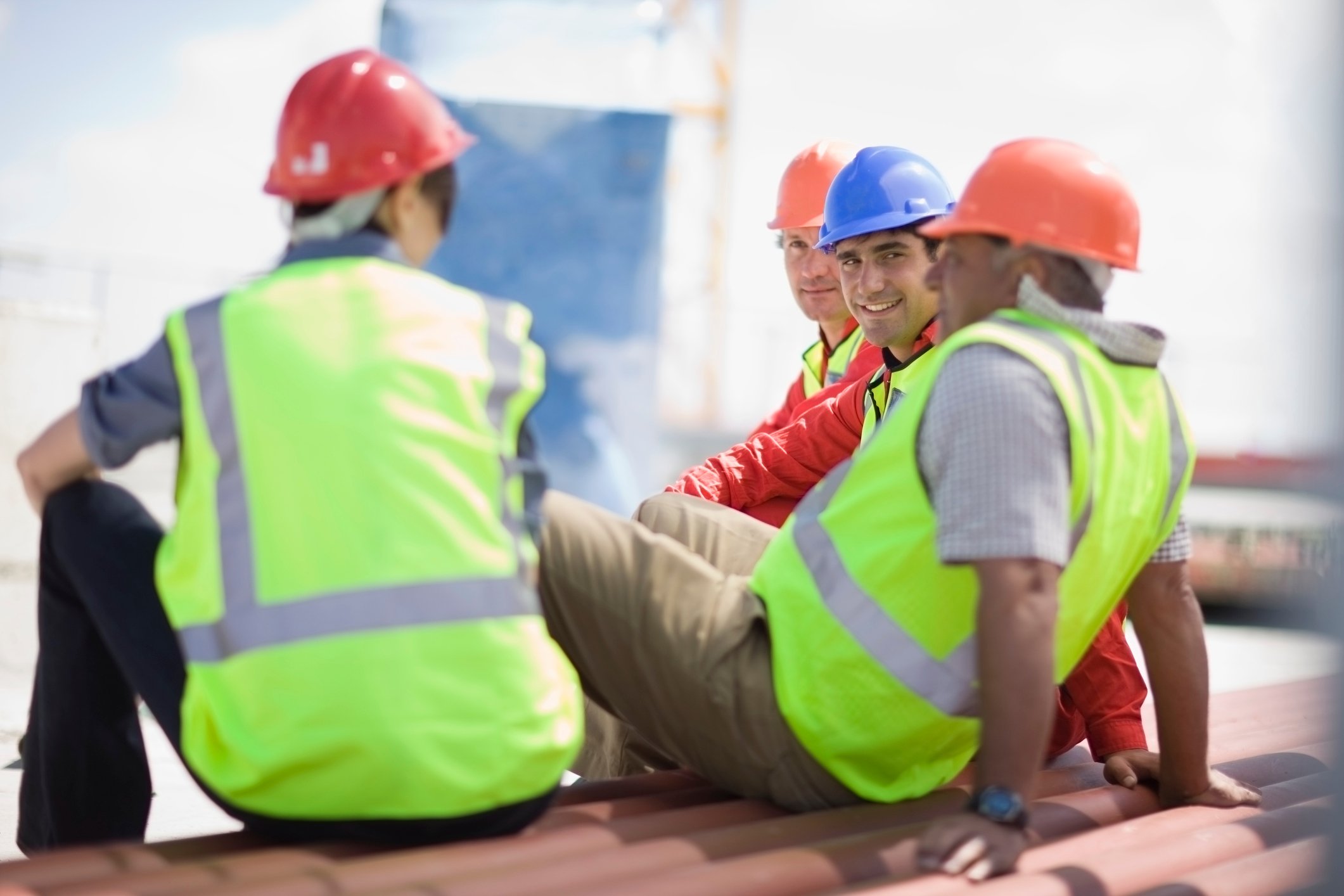
Downtime, in any industry, can be disruptive to work productivity and take a significant financial toll from affected companies. Business, after all, is not as usual when unplanned, external factors disrupt workflows, bring assembly lines to a screeching halt, and force teams to have to rethink processes quickly to make up for lost time.
A survey in the auto industry, for example, revealed that the average monetary impact of production downtime was $22k for each minute of unplanned manufacturing workflow interruptions. The IT industry, similarly, can relate to these downtime-related financial stressors; whether they’re due to something as benign as human error or more worrying cybersecurity incidents, the overall estimated cost per hour of enterprise downtime worldwide in 2019 was between $301k and $400k! Some real-world examples: A 12-hour outage back in 2015 cost Apple an estimated $25mil in sales. A briefer 5-hour computer outage in 2016 cost Delta Airlines an even higher $150mil, resulting in 1,000 cancelled flights, followed by refunds and vouchers being issued.
So, what is the cost of downtime in construction? That’s what we’ll be discussing in this article! More specifically, we will:
Project Downtime Meaning: What Is Construction Downtime?
Meriam-Webster defines downtime as “time during which production stops especially during setup for an operation or when making repairs;” or, alternatively, as “inactive time (such as between periods of work.” They offer an example as, “an injured athlete facing months of downtime.”
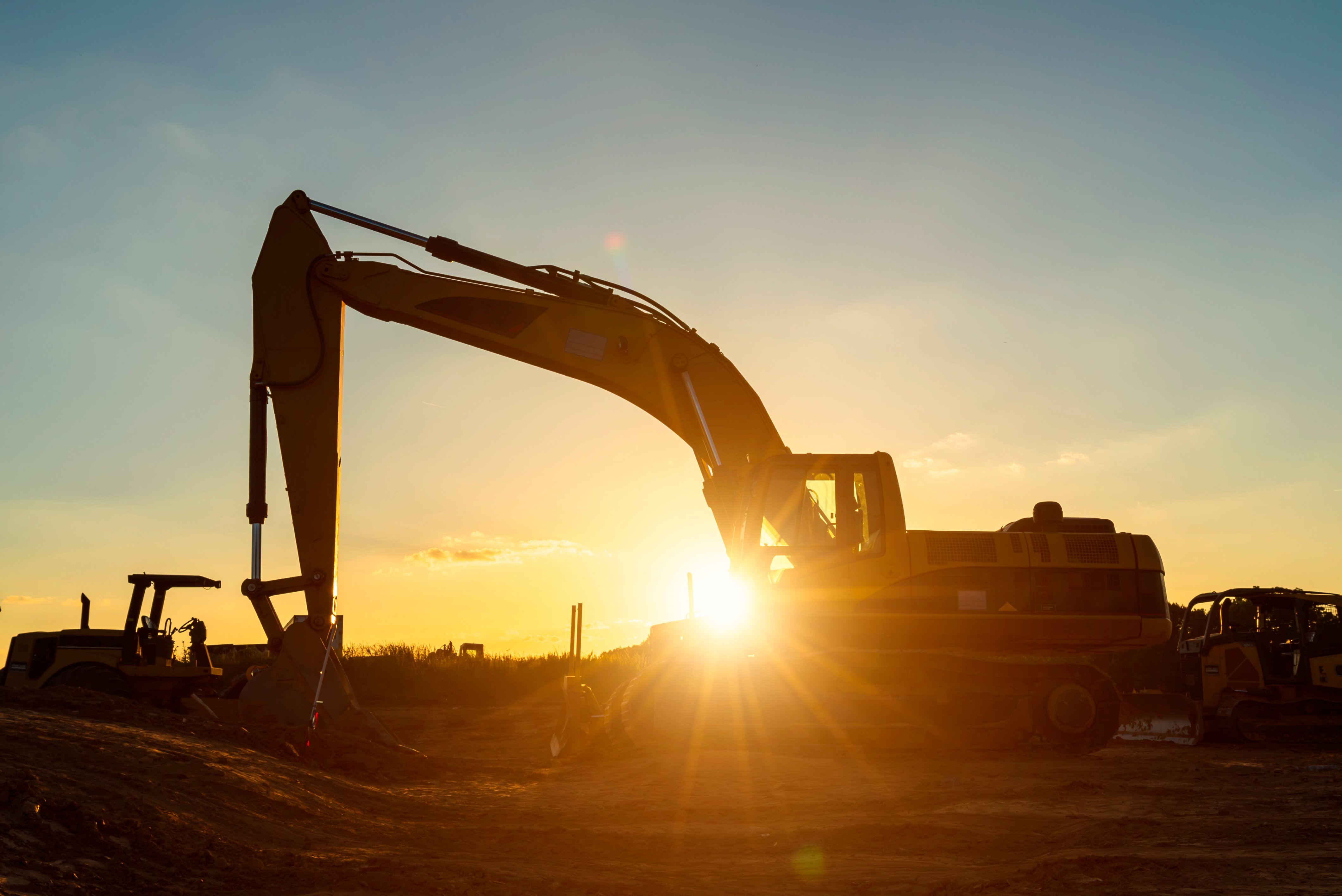
To keep it broad, our construction downtime definition is time during which construction work ceases and leads to loss in productivity due to any internal (org-specific) or external factors. Going back to Meriam-Webster’s definition, sub out “injured athlete” in their example for “contractor/GC;” Example: A contractor faces hours of construction downtime due to equipment failure.
Related questions/definitions:
- What is maintenance downtime? ‘Maintenance downtime’ in construction would be a case during which construction work has to halt because assets are rendered unusable due to planned or unplanned service/repairs.
- What is equipment downtime? Similarly, ‘equipment downtime’ would be the time during which construction work has to halt because critical equipment (such as expensive machinery you have limited quantity of, like cranes, dozers, excavators, etc.) requires planned or unplanned service/repairs or is otherwise rendered unavailable (on another job, in transit, has been stolen, needs to be retired/replaced, etc.).
What Is the Cost of Construction Downtime?
The average downtime cost for a fleet vehicle, necessary to carry critical inventory and materials to the job, is estimated coming in at $448-$760 per day, per vehicle.
It’s harder to calculate the direct financial impact of construction worker downtime.
Though it may be challenging to put a universally accepted, hard and fast monetary rule to it—as in “1hr of downtime costs me X dollars”— experts in construction do consider downtime rates in the 20-30% range to be typical for the industry. That’s a big percentage of uncertainty to plan for! But when you’re combatting real industry-wide problems like a narrowing job pool, the focus needs to be on what you can realistically influence, and that comes down to being proactive with your planning and maintenance, and nimble on your feet so that you can respond to rapidly changing circumstances.
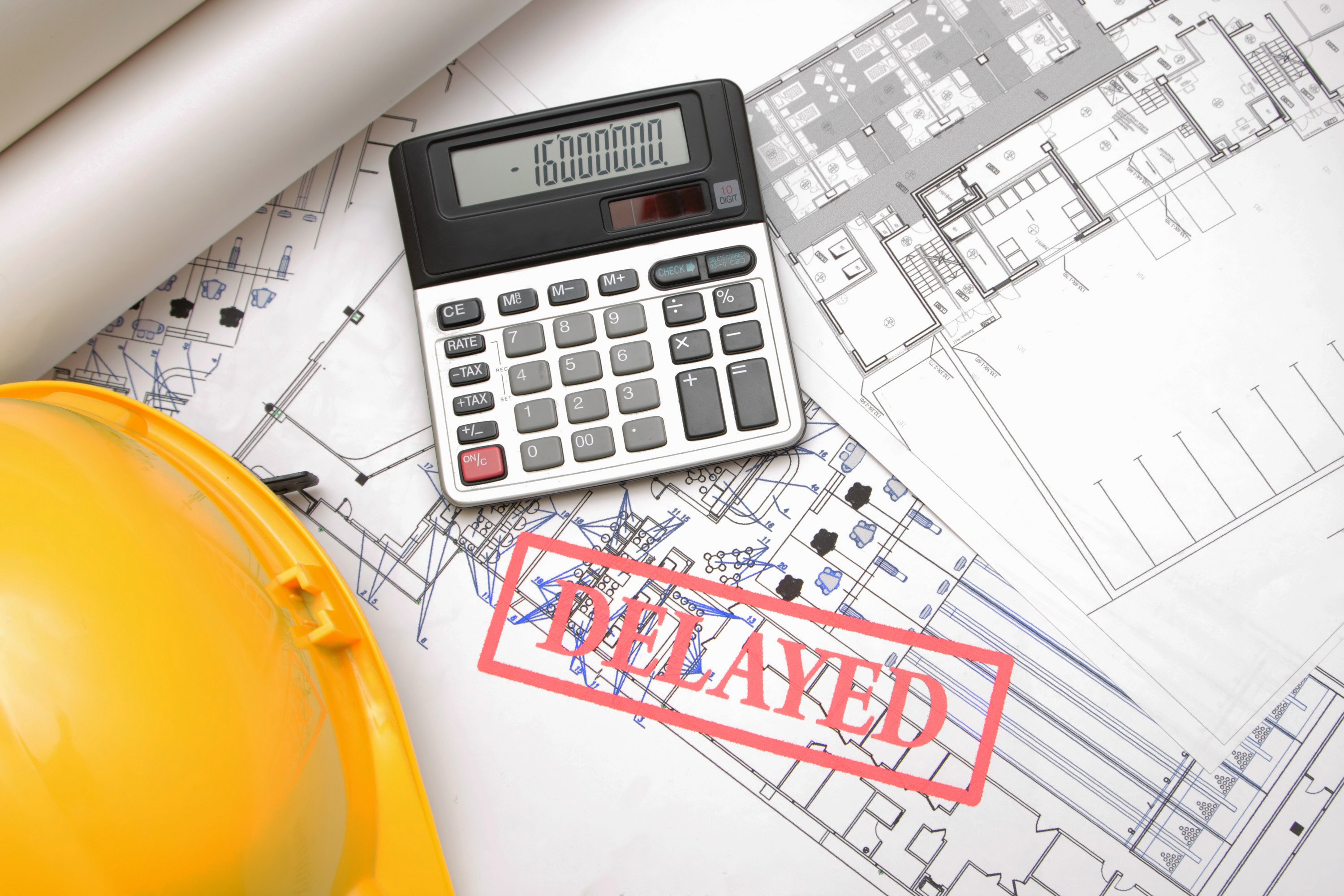
Perfectly summed up by Dan Corbett, equipment manager for Lancaster Development, quoted in ForConstructionPros, “It’s the collateral damage that really costs you money,” the unforeseen circumstances that lead to lost productivity.” He adds that it’s, “Not so much the repair of a downed piece of equipment” that is financially impactful, but rather, “how that impacts the job.” Think: The hours, days, of work that must be diverted due to generators not turning over, power outages, equipment breaking down and needing to be serviced/replaced, or logistics problems like materials not arriving on schedule.
When it comes to downtime in construction, cost overruns can multiply quickly if, for example, GCs are absorbing those upfront costs often to replace critical equipment (either buying or renting) simply to stay on schedule. If this becomes a common occurrence, looking inward to determine the underlying cause is a crucial first step toward continuous improvement.
While you certainly can’t predict construction downtime, it’s important to be proactive (we’ll get more into this in the next section of this article when we discuss the common causes of construction downtime and offer our suggestions to avoid them to the best of your ability). While it may be difficult, even futile, to worry about precisely estimating downtime costs, as ConstructionEquipment.com points out, it’s better to “Reduce or eliminate down events;” they expound:
Do everything you can to reduce or eliminate reported emergency down events, and you will be doing everything you can to reduce or eliminate the cost of downtime. Focus on the root cause of downtime costs. Eliminate down events.
Now that we’ve defined construction downtime in simple terms, and given the basic cost breakdown, let’s:
- get more specific about what causes it construction downtime +
- give you some tips on how to prevent downtime happening at your org.
Common Causes of Construction Downtime
A study conducted by Engineering Construction & Management breaks the common causes of construction downtime into several “factor” categories:
- Site-related factors: These factors, they explain, include “poor working conditions, uncertainties during equipment operation, and location of the site.”
- Equipment-related factors, they explain, are those “related to […] its age, type, quality, complexity, and degree of usage.”
- Crew-related factors, they explain, are those “related with human aspects who are involved with equipment maintenance, operation, and production process.” They expound that factors in this category relate to “skill of operators and mechanics, fatigue, morale, and motivation.”
- Force majeure-related factors: Stemming from a French term meaning unanticipated events, these factors, they explain, are “the events that are unanticipated by project participants, particularly related to natural calamities and events.” Examples they provide include floods, landslides, vandalism, and accidents.
- Company’s procedures and policies-related factors, they explain, refer to a “company’s standard procedures and policies towards equipment management decisions and may include factors such as maintenance policies, replacement decisions, inventory management and control, standby repair and maintenance facilities, and procurement systems.” While not all companies, they explain, can justify the cost of carrying spare parts, influenced by a number of available jobs on hand, such policy may prove problematic should breakdown incidents transpire, requiring repair/replacement costs and loss of productivity due to downtime during unplanned maintenance events.
- Project-level factors, they explain, refer to the “availability of spare parts, resources, and rental facilities, substitute equipment on hand, the location and sophistication of a workshop, and other project-specific requirements.”
We’ve broken the above “factor” categories into common construction downtime causes as they relate to the higher-level categories and we’ll also include “potential solutions” in bold in for each downtime cause.
- Lack of power equipment (project-related factor/company policy)
- Machinery/equipment breakdown (equipment-related factor)
- Waiting (company policy/inventory management and control)
- Inclement weather (force majeure-related factor)
- Accidents to workers (crew-related factor)
- Mismanagement/disorganization (project-related factor)
1. Lack of Power Equipment (project-related factor)
Traditional jobsite power comes at a premium—runs on gas (which adds up, about $50/month, per unit) and comes with costly maintenance, hence having multiples in your fleet isn’t necessarily a luxury everyone can get behind.
What’s more, the power that enables you to get the job done is not without its faults:
- The power you need, typically produced by generators, runs on gas (creating hazardous emissions), and is often unpredictable.
- Old, unreliable corded (and despite the nomenclature, not particularly powerful) power tools that require to be plugged into an outlet using traditional electricity may prove unwieldy in rough-in situations where power is inaccessible and further creating trip hazards and diluted voltage through knotting extension cables.
Possible solutions:
- Replace old, unreliable power equipment. A reliably unreliable source of far too many job day disruptions is the traditional power generator. When running, it creates hazardous emissions that are dangerous to the user and the environment; when it’s not running, giving you problems getting started, that could be several hours of lost productivity. A sustainable construction alternative worth your consideration is replacing your gas-powered generator for a battery-powered generator which, aside from being better for the environment, provides dependable, portable, on-demand power.
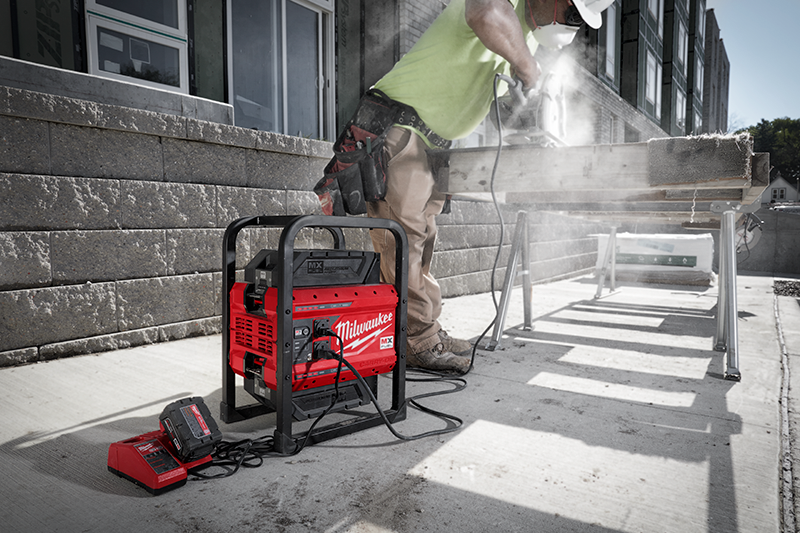
- If you’re using old corded power tools, cut the cord and the trip hazard with high-performance battery-powered tools built for professional trades: M12™ power tools are ideal where portability (without sacrificing performance) is a must, while M18™ power tools are optimized for high-performance.
2. Machinery/Equipment Breakdown (equipment-related factor)
It doesn’t matter if it’s an ill-maintained dozer or an impact driver that breaks down. You can immediately sense the productivity losses when the tool you need to get the job done is not working.
Possible Solutions:
- Maintain, maintain, maintain. To help keep these freak accidents to a minimum, preventive maintenance is critical. It’s important to follow your manufacturer’s guidelines regarding proper usage and maintenance. Some tools like cutting edge 3/8” and 1/2” digital torque wrenches, for example, require being recalibrated to ensure proper functioning. You can also log away important service documentation in your One-Key app or set service reminders to ensure you’re automatically alerted when nearing your scheduled maintenance. That way, you never miss an important date!
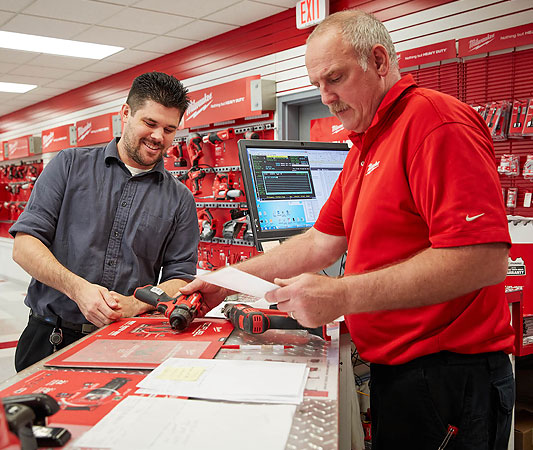
- Know when to repair vs cut your losses and replace lost causes. Sometimes, it makes more sense to repair tools that break down; other times, the possibility of another breakdown far outweighs the price of purchasing a replacement. Knowing when to repair vs replace power tools and equipment is key.
3. Waiting around for Materials or Tools and Equipment (company policy/inventory management and control)
In the example from above related to inventory and control company policies, it was explained that some companies can’t justify the cost of carrying spare parts (or put another way, having an ample supply of each power tool needed at various stages of production. When this happens, issues may arise: tool transfers may be necessary, and with multiple jobs going at once, this may result in a game of tug-of-war for equipment.
Consider, for example, a recent 2019 study into inventory control that viewed "10-12% reduction in labor cost essentially originates from avoiding non-productive idle time or down time of the manpower due to searching for materials waiting for new arrival of material."
Whether it’s limited inventory competing for being deployed at multiple jobs, items that are pulled out of circulation for maintenance, decommissioned items that need to be retired, or misplaced items that need to find their way back to the crib, managing a tool and equipment inventory as a huge job!
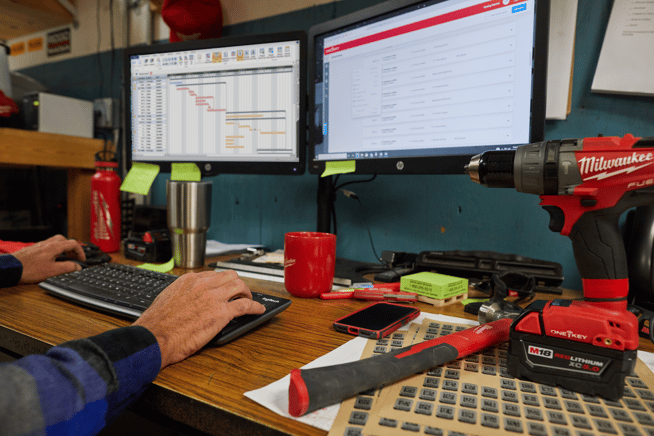
Possible Solutions:
4. Inclement Weather (force majeure-related factor)
Wet soil, especially in the early stages of construction excavation, can make these critical days of building necessary foundation challenging and potentially dangerous to operators.
Weather can also cause damage to construction materials and make for an unpredictable timeline.
Potential solutions:
- Ensure proper equipment for the soil conditions is deployed to the site. Excavator attachments can be used to prevent sticky mud and clay from clogging and clinging to excavators and ensure a smooth digging and trenching experience.
- Heated gear, built to withstand unpredictable cold weather construction conditions, can help keep you warm in extreme sub-zero temperatures and protected with heavy-duty abrasion- and tear-resistant materials designed to maximize durability, flexibility, and performance.
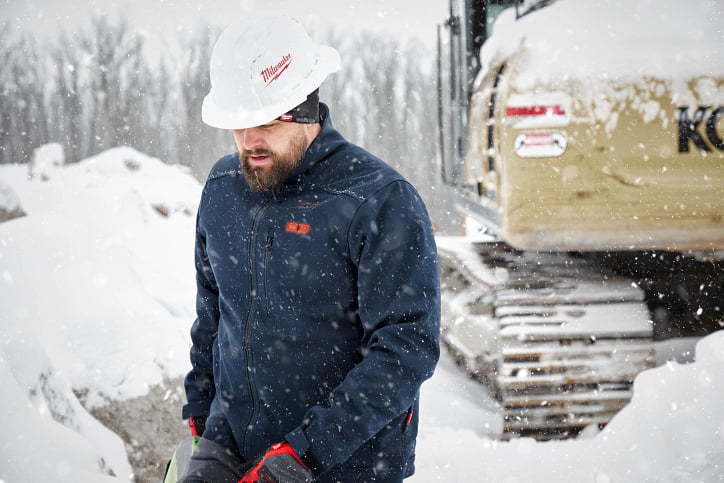
- Prefabricated construction methods (aka, offsite construction), when adopted, can help construction companies more reliably predict completion timelines and cut out the weather-related variables that might otherwise cost you to miss a deadline; materials like walls are built offsite in a factory-like setting and delivered later to the jobsite to be craned in and assembled. Modular construction, a subset of prefabricated construction, is when 3-dimensional “modules” (we’re talking full rooms) are manufactured offsite to later be delivered and installed onsite. With both prefab and modular construction methods, you have more control over the manufacturing process (you’re not competing with project-impacting weather conditions), a better handle on overall quality control of materials (not sustaining defects from weather exposures), and you can use this process to combat inclement weather, choosing your job days based when bad weather clears up.
5. Accidents to Workers (crew-related factor)
Unfortunately, accidents happen. According to the Bureau of Labor Statistics, over 60% of construction accidents occur within an employee’s first year of work.
Construction accidents are also expensive. For example, The total cost of all construction injuries in the United States is more than $11.5 billion, according to the National Institute of Health. According to the Bureau of Labor Statistics, more than 130,000 construction workers missed days of work due to injuries in 2019, decreasing productivity. Workers’ comp claims for non-fatal falls account for $2.5 billion annually, according to Liberty Mutual.
The good news, the Occupational Safety and Health Administration (OSHA) offers safety training for individuals and organizations. They estimate companies save $4-$6 for every $1 invested in safety programs.
Potential Solutions:
OSHA offers guidance to avoid the “fatal four,” the events accounting for 60% of all construction-related deaths:
- Preventing falls—OSHA recommends wearing personal fall arrest equipment; installing/maintaining perimeter protection; covering and securing floor openings and labeling floor opening covers; and using ladders and scaffolds safely.
- Preventing “struck-by” incidents—OSHA recommends to never position yourself between fixed objects, and also recommend wearing high-visibility clothing, such as high-vis safety vests.
- Prevent caught-in/between incidents—OSHA recommends to never enter an unprotected trench or excavation 5 feet or deeper without adequate protection in place, and also recommend to make sure the trench or excavation is protected either by sloping, shoring, benching, or trench shield systems.
- Preventing electrocutions—OSHA recommends locating and identifying utilities before starting work; looking for overhead powerlines; maintaining a safe distance away from powerlines; to not operate portable electric tools unless they are grounded and double insulated; using ground-fault circuit interrupters for protection; being alert to electrical hazards when working with ladders, scaffolds, or other platforms.
Whether it's hiring a safety manager or deciding which construction safety KPIs make the most sense for your company, construction safety is critical.
6. Mismanagement/Disorganization (project-related factor)
Too often teams get siloed, communication becomes disjoined, and the data you do have is a flurry of information of which you don’t know is the most pressing.
Potential Solutions:
Wrapping It Up: Avoid Downtime by Being Proactive and Embracing Real-Time Collaboration
Some downtime on the jobsite will be unavoidable; but it’s how you quickly you’re able to adapt to these events that will determine if the collateral damage it causes is lasting and financially crippling. Planning for the factors you can realistically influence will ultimately the down events you experience:
- Adopt eco-friendly power equipment and cut the dang cord already!
- Don’t put off maintenance. That’s asking for trouble! Also, know when it makes more sense to send tools in for repair or when it’s time to cut a tool loose.
- Use heated protective gear for harsh weather conditions when you have to work; if you can, adopt offsite construction methods (prefab/modular) to offset these weather-related incidents.
- Encourage your team to wear protective equipment and take OSHA safety examinations. Better yet, make it one of their objectives for the year!
- Adopt cloud-based software to get everyone on the same page. Make sure that software supports integration (or ask your provider to build a critical integration for you!). This will ensure your teams do not become siloed.
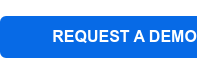
TL;DR
Project Downtime Meaning
- What Is Construction Downtime? Our construction downtime definition is the time during which construction work ceases and leads to loss in productivity due to any internal (org-specific) or external factors. Two related definitions:
- Maintenance downtime’ in construction would be a case during which construction work has to halt because assets are rendered unusable due to planned or unplanned service/repairs.
- ‘Equipment downtime’ would be the time during which construction work has to halt because critical equipment (such as expensive machinery you have limited quantity of, like cranes, dozers, excavators, etc.) requires planned or unplanned service/repairs or is otherwise rendered unavailable (on another job, in transit, has been stolen, needs to be retired/replaced, etc.).
What Is the Cost of Construction Downtime?
- While it’s hard to quantify monetarily, experts in construction generally agree that downtime rates in the 20-30% range to be typical for the industry. Downtime of a fleet vehicle may be $448-$760 per day, per vehicle.
A study conducted by Engineering Construction & Management breaks the common causes of construction downtime into several “factor” categories:
- Site-related factors
- Crew-related factors
- Force majeure-related factors: (unexpected circumstances)
- Company’s procedures and policies-related factors
- Project-level factors
Stemming from these factors, we define 6 common causes of construction downtime:
- Lack of power equipment (project-related factor/company policy)
- Machinery/equipment breakdown (equipment-related factor)
- Waiting (company policy/inventory management and control)
- Inclement weather (force majeure-related factor)
- Accidents to workers (crew-related factor)
- Mismanagement/disorganization (project-related factor)