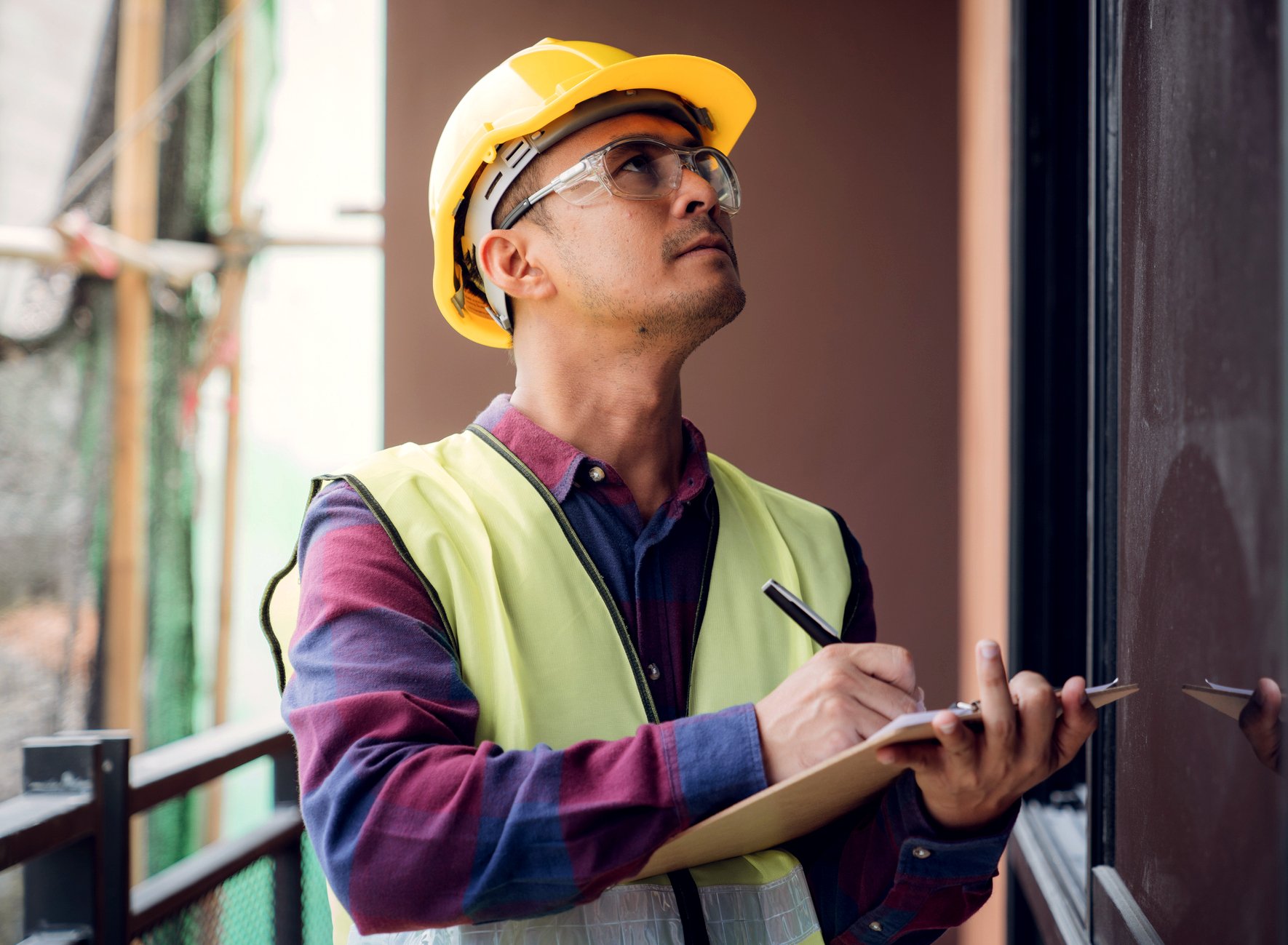
There is nothing more important than safety in the workplace. This axiom is especially true in an occupation as dangerous as construction. Jobsites are kinetic places full of electrical and chemical hazards, heavy equipment, spinning power tools, and precarious heights. If the proper precautions aren’t taken, odds are high that you will get hurt, or worse.
The latest numbers from the Bureau of Labor Statistics (BLS) tell a story of deadly seriousness: In 2019, there were 1,102 fatal construction injuries in the United States, a more than 6% increase from 2018. Put another way, construction accounts for almost 21%—or about one in five—of all workplace related deaths in the US. And that’s just the fatal incidents. That same year, there were 79,660 non-fatal injuries on construction sites in the US alone. In some years, construction has even experienced a shocking 71% more injuries than all other industries combined.
In an industry as expansive as construction, there are many different career paths one can take, each with varying levels of risk and hazard. Whatever the job may be though, the statistics above make one thing abundantly clear: Whether you’re a skilled tradesperson in the field or a project manager in the back-office, safety needs to be your number one priority. It’s so important in fact that there’s an entire profession devoted to ensuring that workers are safe and healthy on the job.
If you’re either new to construction or looking to change careers within the field, if you have a sharp eye, are meticulously detail oriented, and passionate about saving lives, then you might want to consider becoming a construction safety manager. In this article, we will provide a detailed job description, describe the salary and job outlook, discuss relevant skills, lay out the education requirements, and offer some insight into the future of the profession.
Explore our full List of Careers in Construction!
Job Description: What does a Construction Safety Manager Do?
The short answer is that a construction safety manager is the person who oversees the safety, health, and well-being of construction workers on a jobsite. The long answer is that there’s a lot that goes into the short answer. It’s not enough to wear a stern expression, wave a hand, and tell everyone in a commanding voice to “be safe out there!” If they’re to be effective, construction safety managers need to be prepared to perform a wide range of duties in the course of their work.
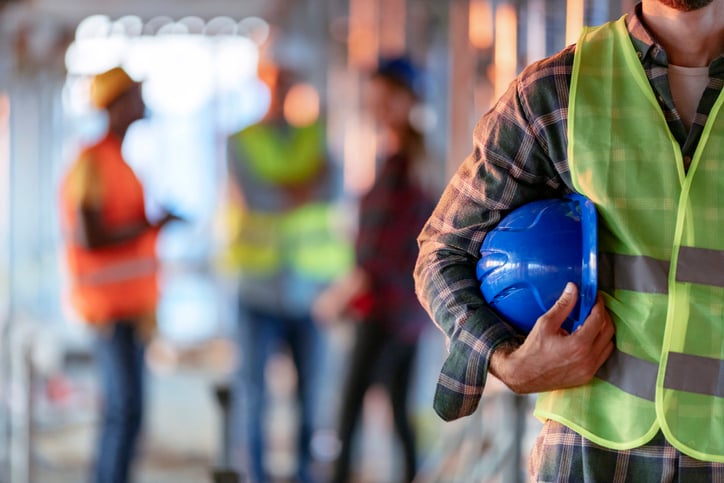
According to the US Department of Interior, common safety manager duties and responsibilities stipulate that the Safety Manager:
- Provides appropriate safety and health, accident prevention, and investigation training for managers and supervisors.
- Assists management in the annual inspection of workplaces to assure safe and healthful conditions for workers. Prepares appropriate notices for management to issue for abatement of any identified hazards.
- Provides promotional materials and develops and administers recognition systems to promote safe and healthful work performance.
- Assists management and supervisors in investigating accidents and developing measures to prevent recurrences.
- Supports the Safety Management Information System (SMIS) by recording all accident reports in a timely, complete, and accurate manner.
- Assures that claims for injuries and illnesses posted in SMIS are posted in the Occupational Safety and Health Administration log.
Source: U.S. Department of Interior
But while the above list of responsibilities is more or less relevant to construction, a safety manager’s duties in our industry are even greater and serious in our industry. Construction, after all, is a complex and moving target. To hit the mark every time, safety managers need to maintain a strong base of knowledge about workplace safety standards, building, and environmental codes. They also need to be adept at crafting safety plans, policies, and procedures tailored to the specific project at hand. Finally, safety managers also need to be proficient at safety training and conducting inspections of tools, materials, and equipment.
In case you were still wondering, we are now at the beginning of The Long Answer to the question of what a construction safety manager does.
Stay up to date on safety standards
You’ve probably heard of OSHA, or the Occupational Safety and Health Administration. This is the governmental organization that sets and enforces a baseline of safety standards for a broad swath of private and governmental workplaces. Established by an act of Congress signed by President Richard Nixon in 1970, OSHA was created in direct response to the alarmingly high rate of workplace deaths that occurred in the 1960s and previous decades. Since its founding, safety on construction sites in particular has been one of OSHA’s top priorities. So much so in fact that OSHA maintains a discrete set of safety standards—Part 1926—that applies specifically to construction as opposed to general industry. This set of standards covers everything from personal protective gear and power tools to best practices for dealing with ionizing radiation. It’s the job of a safety manager to have a deep level of understanding of OSHA’s standards, to see that they’re enforced, and to make sure that workers are aware of their rights to a safe and healthy workplace.
Uphold building and environmental regulations
Safety isn’t just a concern for workers. It’s also a concern for the people who end up using the finished structures that those workers are tasked with building. This is where building codes come in. Sets of locally enforced laws and regulations, building codes are what govern the standards by which structures are designed, built, and maintained to ensure the safety of human occupants. They cover everything from fire alarm and emergency exit placement to the quality and configuration of plumbing and electrical fixtures. Different building codes apply to different situations and often vary from one region to the next, but most municipalities in the US currently use some version of the International Building Code (IBC) developed by the International Code Council (ICC). It’s a safety manager’s job to make sure construction unfolds in accordance with these codes. This part of the job is not only essential to weaving safety into the DNA of a building project, it’s also key to avoiding costly and time consuming delays caused by the correction of violations that might be caught when the building inspector comes around.
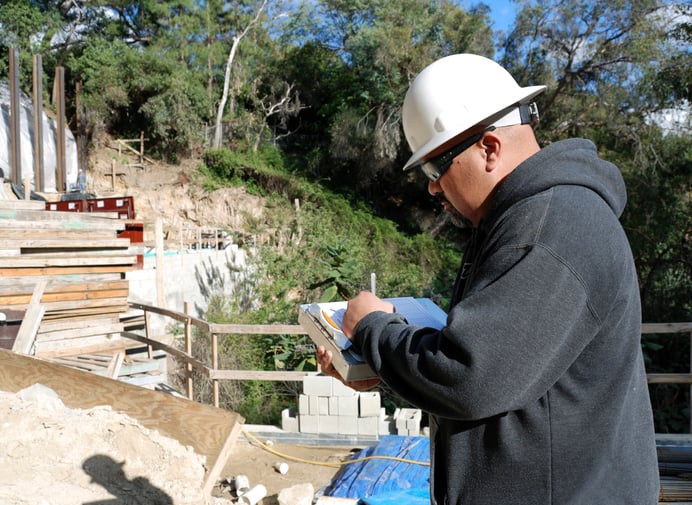
And let’s not forget that safety extends to the wellbeing of the natural world as well. While there is currently no widely enforced “green” building code, a number of codes and ratings systems exist that project developers can choose to adopt in order to make their end-products more sustainable and less environmentally destructive. Some examples include the International Green Construction Code (IgCC), Leadership in Energy and Environmental Design (LEED), and Green Globes. This is another role that construction safety managers perform: working closely with project managers to keep sustainable building projects safely within the green.
Create safety plans
Tailoring a plan to prevent fatalities and accidents is one of the most important parts of a safety manager’s job. No two construction projects are exactly alike. Each one comes with its own unique set of hazards. Workers should be confident that whatever the project may be, their safety, health, and wellbeing is the number one priority. Required by OSHA, the safety plan is where the rules and structures of accountability are laid out. While everyone needs to be mindful of their own and everyone else’s safety, it’s the supervisors and project managers who are ultimately responsible for enforcing it. In drafting these plans, safety managers ought to enshrine OSHA guidelines but also endeavor to go above and beyond them to create the highest safety standards possible. Specificity is key: If the project is a commercial skyscraper, the safety plan ought to provide clear strategies and precise precautionary measures for how large numbers of workers can safely labor with and around each other at great heights. What happens if someone trips, falls, or drops a tool from high up? The safety plan is where these and many other questions are answered. Safety plans should also be adaptable to changing circumstances and conditions. If the weather suddenly takes a turn and the job site is buffeted by 40 mile per hour winds, the safety plan should change to incorporate updated guidelines for securing loose materials and providing even greater protections for personnel from falling debris. Safety managers need to instill a strong culture of safety at every layer of the workplace. The first step toward accomplishing this is to create a clear, concrete, comprehensive, and actionable safety plan.
Train personnel
Another critical part of the safety manager’s job is to conduct safety trainings. It won’t matter how thoughtful and well written your safety plan is if no one knows what’s in it or how to put it into action. Everyone needs to be on the same page to create a safe work environment and it’s the safety manager’s job to make sure that happens.
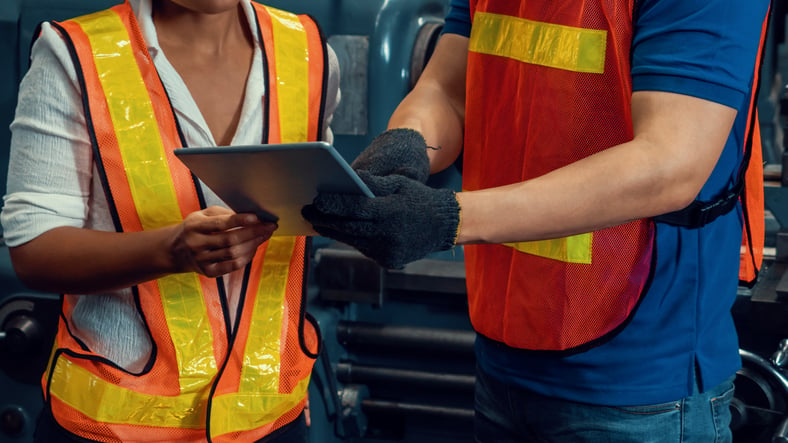
Safety managers are responsible for crafting and conducting presentations pertaining to specific safety related topics. A good place to start is to talk with employees about their concerns. Is there some aspect of their work that frightens them or that they feel endangers their safety? Are there areas where protocol is lacking or where employees are uncertain how to proceed? Each of these questions is a great springboard for identifying safety training opportunities. Once this is completed, the safety manager must then create a training program that educates employees and engages them in hands-on learning activities. Power tool safety, accident response, how to communicate with team mates on a dangerous job site—all of these are fodder for safety trainings. Practice makes perfect and there’s nothing like regular training sessions for ensuring that the best possible protections are in place for everyone at the table.
Conduct inspections
Accidents don’t happen by themselves. It’s up to the safety manager to regularly inspect tools, equipment, materials, and the construction site itself for conditions that could lead to injuries or death.
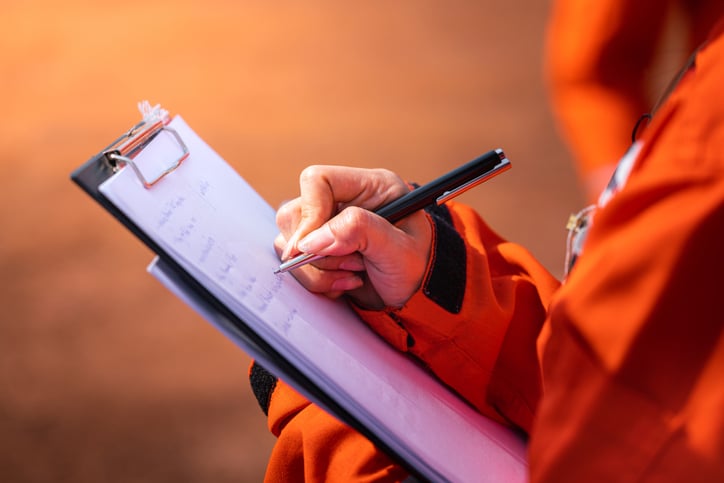
Construction sites are dynamic environments that are constantly in motion. Some of the hazards are obvious, while others are less so. A safety manager must have a keen and ever watchful eye for catching things that might endanger the lives of other workers. Once spotted, a safety manager must take swift action to eliminate threats and set in place preventative measures to avoid future incidents.
Similar titles
- Construction safety manager
- OSHA safety manager
- Site safety manager
- Construction safety inspector
- Safety coordinator
Related careers
Salary Info: How Much Money Does a Site Safety Manager Make?
A wise man once said, “with great responsibility comes higher than average compensation.” Jokes aside, construction safety managers really do earn more per year than most of their colleagues in the world of construction. According to the BLS, the median annual salary for a construction safety manager is $74,550. You’re not getting rich with those wages but the pay looks pretty good when you compare it to the average $41,950 annual salary earned by most other occupations in the US job market. Even safety managers on the lowest end of the payscale make more than that. In 2020, the lowest 10% of safety managers earned somewhere in the range of $44,000. Meanwhile, the top earners made as much as $112,850 per year.
What’s the Job Outlook of a Construction Safety Manager?
Not much to see here. The good news is that the number of job openings for safety managers is expected to rise over the next decade. The bad news...well, there isn’t really any bad news, other than that the rate of growth just isn’t anything to write home about. Overall, the BLS expects a 7% bump in the safety manager job market between now and 2030. This may seem like a low number, but it’s actually in line with what’s projected for most other occupations in the rest of the US job market. Again, this is good. Just not spectacular. If, on the other hand, you’re looking for a career with a skyrocketing growth trajectory, you should think about becoming a wind turbine technician or a solar photovoltaic installer.
Typical Construction Safety Manager Skills
If you’ve made it this far, by now it should be clear that safety managers perform a wide range of functions, each requiring a variety of hard and soft skills. Deep knowledge of occupational health and safety is of course a must, and we’ll get into how you can go about acquiring that knowledge in a moment. The devil is in the details when it comes to creating and maintaining a safe work environment and a safety manager above all else needs to have a sharp eye for catching those details. Once a problem has been identified, a safety manager needs to be able to find and operationalize a solution, whether it’s a temporary fix for an immediate crisis or a multi-layered series of tried-and-true safeguards. More to the point: creativity and problem-solving skills are key to this line of work. A competent safety manager ought to also have a certain amount of tech savviness. There are so many software packages and digital tools these days that can aid a safety manager in their mission, including Milwaukee Tool’s very own One-Key inventory management platform. How better to keep track of large sets of potentially dangerous tools and equipment than with a state-of-the-art Bluetooth tracking system? Of all the skills that a safety manager must possess, however, the most important is communication. A safety manager’s extensive knowledge of workplace safety is useless unless they can clearly get it across to those who need it most. Patience and a proven ability to convey complex sets of information are essential qualities in this profession. Safety managers are like teachers in this regard: strong listeners, engaging communicators, and deft improvisers.
Required Education and Certification for Safety Managers
You’re going to need a high school diploma and a bachelor’s degree to be considered for most jobs as a construction safety manager. When choosing a degree, stick to occupational health and safety or another technical field such as engineering, biology, or chemistry. Workplace health and safety is a serious matter, so some jobs may also require a master’s degree in a field such as industrial hygiene or health physics, with an emphasis on written communications or accident prevention. Health and safety certification can be pursued through an OSHA Training Institute Education Center or through the Board of Certified Safety Professionals. While not necessarily required, it’s also a good idea for safety managers to pursue continued education throughout the course of their careers, whether in the form of attending formal in-person trainings or staying apprised of developments in the field through online research and webinars.
What Does the Future Look Like for Construction Safety Managers?
The construction industry is changing. Advances in technology and a shift toward sustainability are just two of the major factors at play. Along with those changes will come new and unforeseen dangers. How construction gets done may look different in years ahead but one thing that isn’t going away is our need to protect workers, everyday people, and the natural world from the dangers inherent in this line of work. The presence of AR headsets, drones, robots, and large-scale 3D printers on construction sites will present new and unique challenges that will call for talented safety managers to overcome. No matter what the future might bring, the health and safety of people must always remain the number one priority. As long as that axiom holds true, there will be a need for construction safety managers.