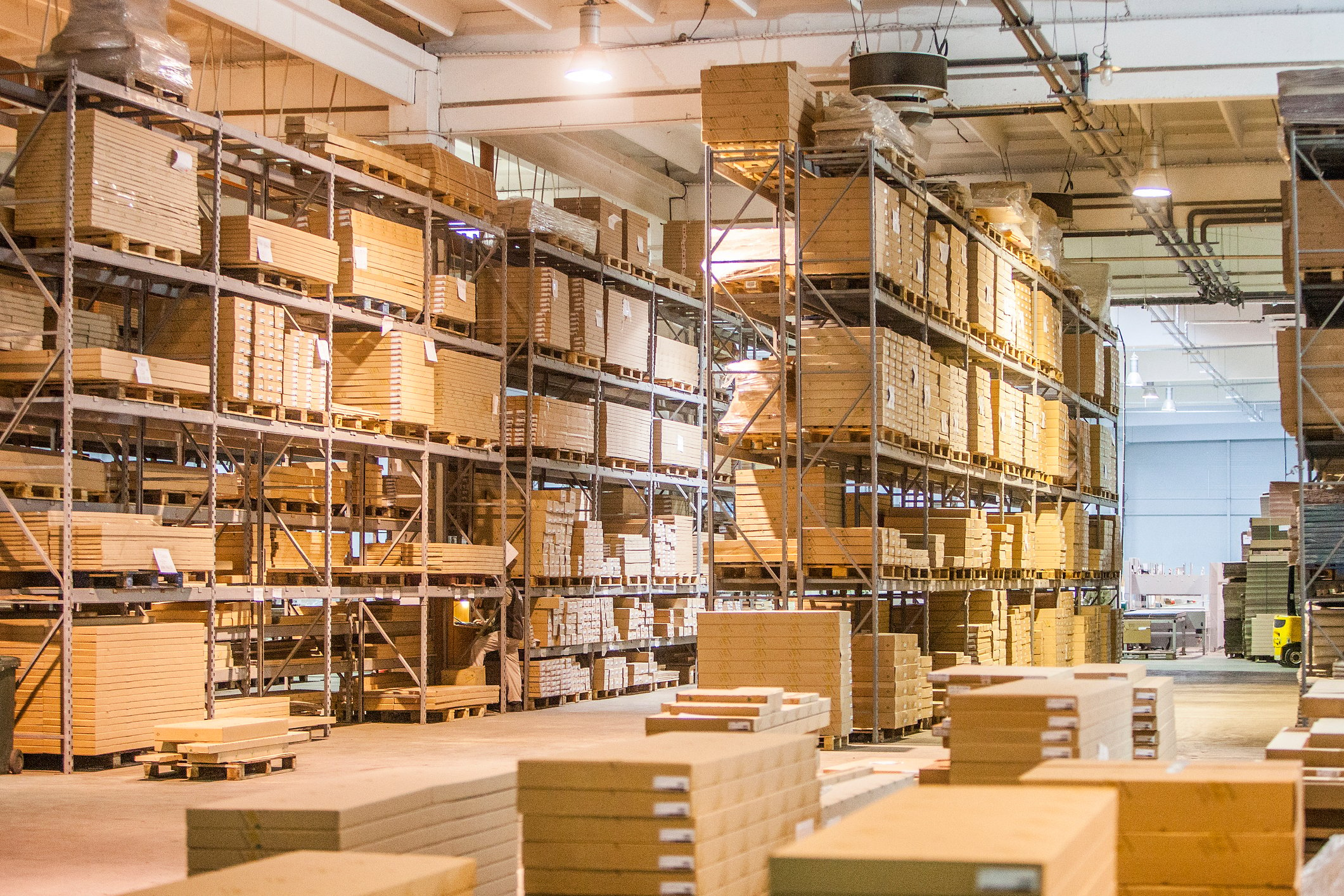
Anyone in the business of selling things comes to this crossroads at some point: How much (if anything at all) should you set aside for a rainy day? This isn’t only a question of money; it also applies to the things themselves–the supply of goods, materials, and finished products that a business provides its customers.
So, is it a good idea to factor in some amount of surplus inventory, a safety stock, if you will, in case of emergencies? Ideally, of course, supply and demand are always thrumming along in perfect unison, eliminating the need for such questions. But it doesn’t take a master’s degree in economics or business administration to know that this isn’t how the world works, not all the time at least. Whether it’s due to an unforeseen crisis, a hiccup in international trade, or plain old bad planning, sometimes there just isn’t enough of one thing or another to go around. The question then becomes: Do you want to prepare for the unforeseeable, or are you happy to roll the dice?
In this article, we will discuss the concept of safety stock and its importance in logistics and inventory management. We will also lay out a roadmap for determining how much safety stock you should plan to hold back and provide a couple tips that might help you better manage your inventory.
Safety Stock Definition: What Is Safety Stock?
Safety stock is an extra quantity of supplies or resources that are deliberately set aside as a precaution against events that can’t otherwise be planned for. Also referred to as “buffer” or “reserve” stock, safety stock provides a cushion against a number of different situations that could lead to you running out of items in your inventory, a phenomenon otherwise known as a “stockout.”
The concept of safety stock isn’t specific to any one individual industry. Any entity that carries an inventory, be it a business, non-profit group, or governmental institution, is capable of creating its own safety stock.
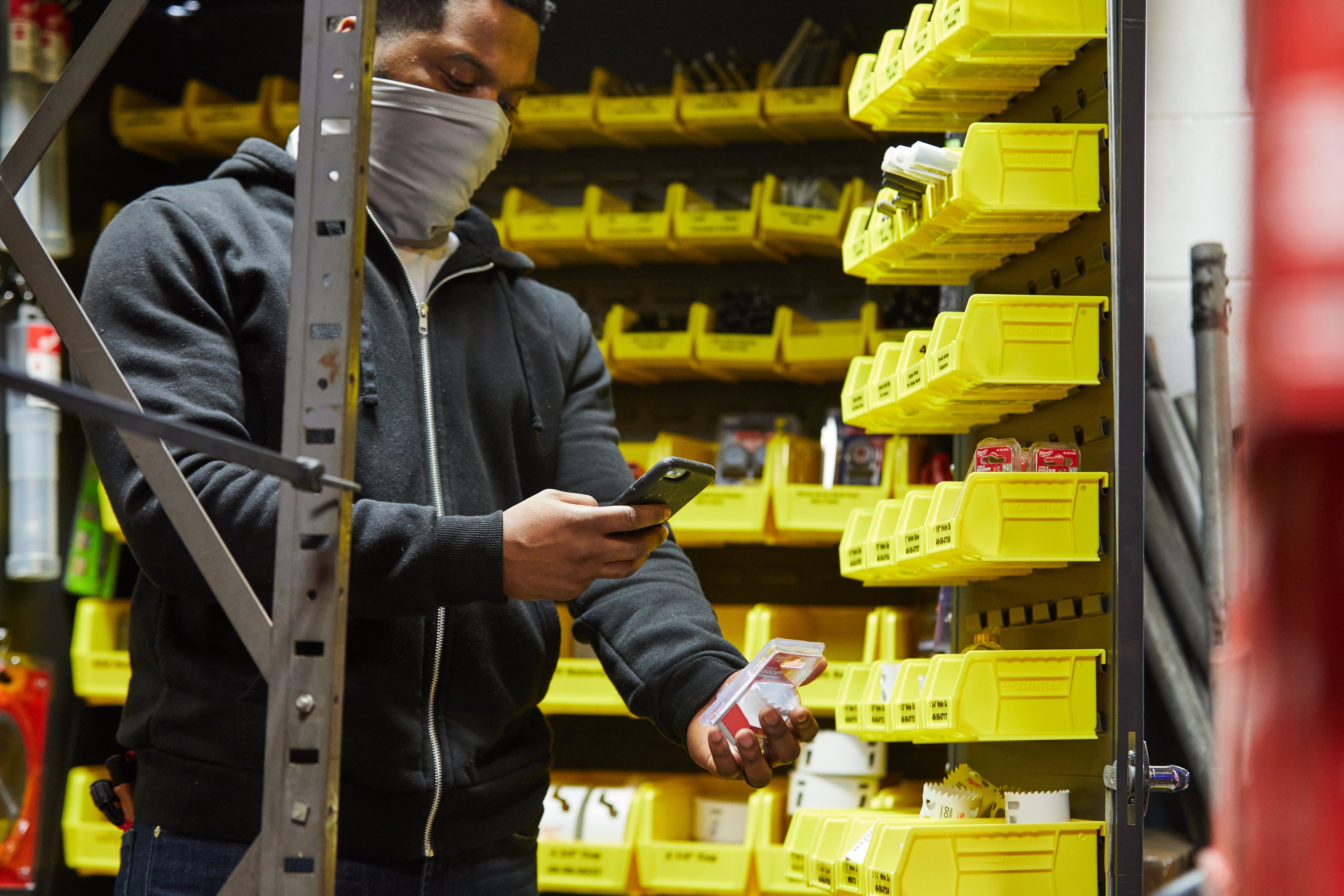
Safety stock can take many different forms depending on the context. The supply needs of a restaurant, for instance, aren’t going to be the same as those of an auto-manufacturer, yet both may benefit from stockpiling additional resources. In the world of construction, contractors might be compelled to create a safety stock of mission critical items like specialized tools and equipment in case of loss or theft; or perhaps a safety stock of essential materials like lumber or concrete in the event of demand outstripping supply–something that has happened on both counts in very recent memory.
Why Is Safety Stock Important?
It turns out there are a lot of reasons why it’s a good idea to factor at least some amount of safety stock into your inventory management plan. Here’s a few that come to mind:
1. Safety stock prevents sales losses
This one is pretty straightforward: If you run out of an item in your inventory, then you can no longer sell that item to your customers, which means less–maybe even significantly less–money flowing into your business. A brief stockout is one thing, but what if it drags on and you’re unable to replenish your supplies in a timely fashion? This can be an especially frustrating place to find yourself when demand for an item is abnormally high. What’s more, the negative repercussions can extend far beyond the duration of an individual incident, resulting in once loyal customers migrating to other more dependable suppliers. With a safety stock in place, you can avoid these pitfalls and always be ready to match demand with supply.
2. Safety stock in times of crisis
Whether it’s a natural disaster, a global pandemic, or the sudden eruption of war, the first decades of the 21st century have shown that crises can strike at any time, causing massive unpredictable disruptions to the supply chains we all rely on. The early days of the COVID-19 pandemic in particular were a harsh lesson in why it’s a good idea to maintain a healthy amount of safety stock.
Like many industries and businesses over the last several decades, the American healthcare system has subscribed to what’s called the Just-in-Time (JIT) approach to inventory management. Pioneered by auto-manufacturer Toyota, the idea behind JIT is that costs can be kept low when supplies arrive “just in time” to meet demand. This philosophy of a “leaner” and “more efficient” supply chain proved deadly, however, when hospitals all across the nation experienced unexpected shortages of essential medical supplies and personal protective equipment. Everything from surgical masks, hand sanitizer, and ventilation machines were suddenly nowhere to be found. As a result, frontline medical workers were left unprotected and it’s likely that some patients were unable to receive the lifesaving care that they needed. With the global supply chain already strained to the breaking point by the pandemic, some industries–even auto-manufacturers – are beginning to question their over reliance on the Just-In-Time approach.
Related article: At Milwaukee® Tool, we use agile methodology that is not dissimilar to lean manufacturing principles in order to get features in the app built faster and into the hands of end users through beta tests. This helps us intelligently prioritize development resources and time, and ensures features are field-tested and approved before final versions are unleashed.
Planning for supplies to arrive only as needed can certainly save money and reduce waste in the short term, but as we’ve seen, this only works if everything else is running smoothly. When the next crisis arrives, who knows which supplies will be needed most or what disruptions may occur to hamper their arrival? In some sectors, it’s better to be prepared and adopt a Just-In-Case mentality instead, where vital resources are stockpiled for a rainy day.
3. Protection from fluctuating prices
Markets go up and down in a global economy, and safety stock can help absorb the shock of unexpected price hikes. To illustrate this point, let’s return to our example of the contractor with their safety stock of lumber. As it happens, the United States has been in the midst of a massive lumber shortage for the last two years and running. This has been driven by a number of factors, including labor scarcity and supply chain failures caused by the pandemic, as well as the destruction of roads and timber stands during widespread flooding in British Columbia; which accounts for 16 percent of North America’s lumber supply. The result? Skyrocketing prices: As of this writing, the price of lumber sits within the range of $1,272 per thousand board foot, which is actually down from the dizzying height of $1,500 that was reached in the spring of 2021. For comparison, in January 2016, the price was as low as $240 per thousand board foot. Put another way: Any notions of efficiency or coloring within the lines of your budget tend to evaporate pretty quickly in the face of massive price spikes like these. That is unless you’re the contractor who, anticipating a sharp curve in the economic road, set aside some of their inventory of lumber, just in case.
4. Safety stock as part of a strategic plan
The best laid plans are the ones that anticipate their own failure. It’s just a matter of statistical probability that there will come a day when even your most sophisticated projections for how much you need in the moment don’t perfectly align with reality. What’s more, as we’ve already covered, unexpected events can negatively impact your inventory management plan at the drop of a hat. The causes of a breakdown need not be so dramatic, however. Maybe there’s a delivery delay. Or maybe you just made a mistake. A stray decimal here, one too many or too few zeroes there, and suddenly you’re staring at empty shelves. With safety stock built-into your overall strategy, you can rest easy in the knowledge that you have a plan for every possible contingency.
Related article: How Contractors Should Navigate Supply Chain Issues
How Much Safety Stock Should You Plan For?
Okay, so safety stock sounds like a pretty good idea by now. What is a good safety stock? How much should you set aside? There are many variables that affect this calculation. There’s no one-size-fits-all answer, but there are a few common denominators that anyone who’s thinking about safety stock should consider.
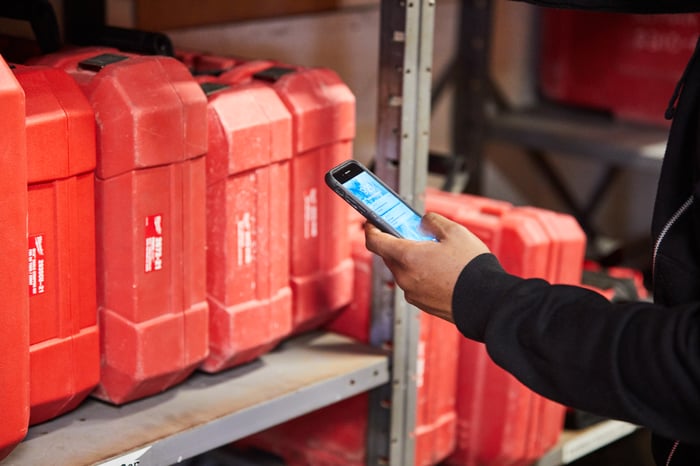
To get a rough picture, a good starting point is to ask yourself some basic questions. How much supply do you need to meet average demand? Is demand easy or difficult to predict? How long does it usually take for your supplies to arrive, and how long does it take for you to sell them? What kind of supply chain do you rely on? Is it composed of global or local suppliers? Do you rely on more than one supply chain? What are the vulnerabilities in your supply chains, and what external safeguards are currently in place to protect you from shortfalls? How volatile is the market you’re in? What opportunities are available to purchase while prices are low? Do you deal in perishable or non-perishable goods? What’s your storage capacity and in the case of perishable items, what amount of that storage capacity is climate controlled?
These and other questions can help orient you in the task of figuring out what an adequate safety stock might look like. If you’re wanting to get out of the ballpark and drill into something more precise, there’s a variety of mathematical formulas that you can choose from to calculate a specific amount of safety stock that feels right to you.
Here’s an example of a fairly common safety stock formula used by small businesses:
(Maximum Daily Usage x max. Lead Time) – (Average Daily Usage x average Lead Time)
There are several other, more complex formulas than this one, each factoring in a number of different variables. The good news is that a lot of them can be executed with relative ease on Excel.
Two safety stock tricks
There’s no shame in admitting that math isn’t your strong suit or that you might need some extra help navigating the subtle intricacies of inventory management. For that reason, we’ve put together a couple tips to help guide you along the way.
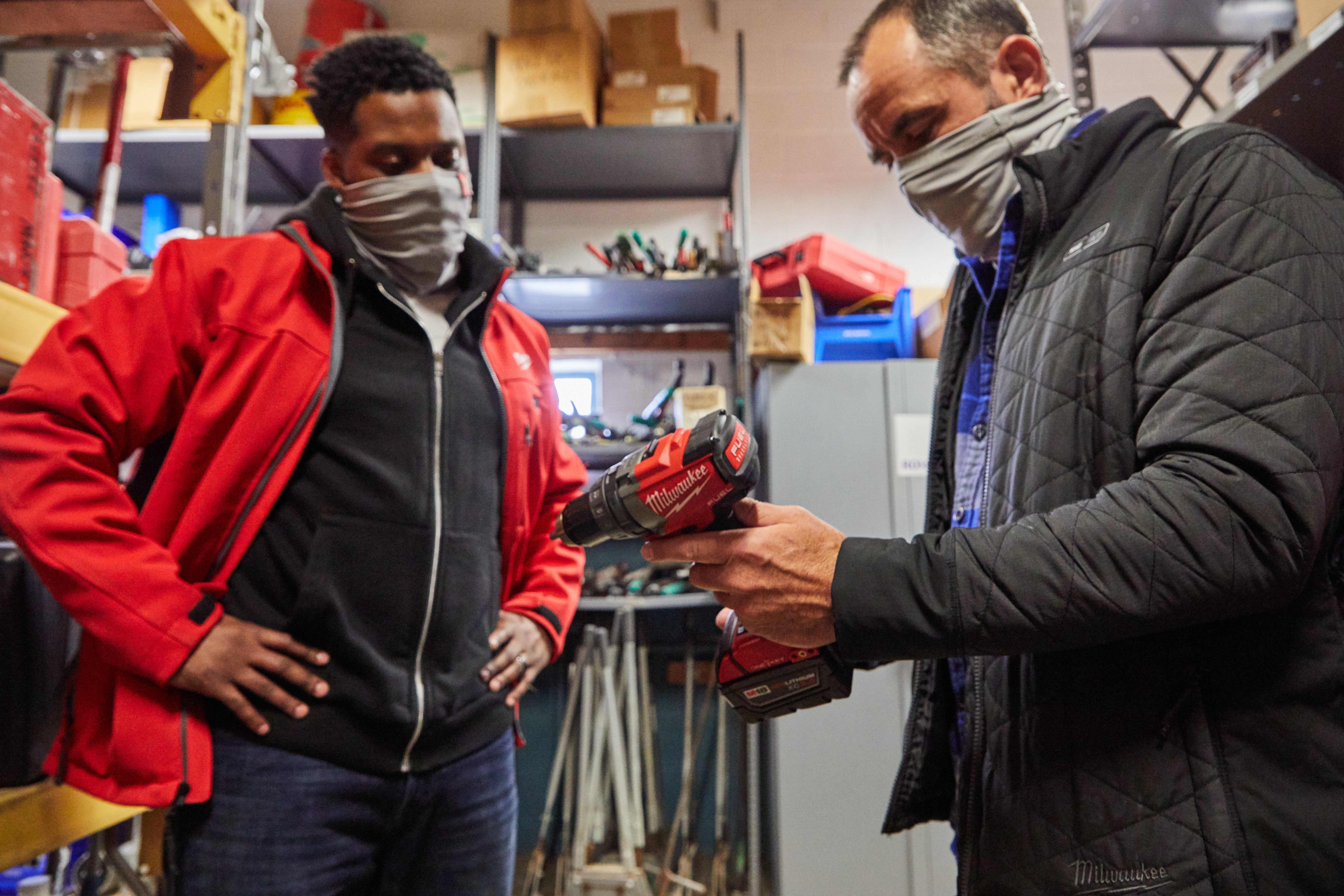
1. Use inventory management software
While running equations on Excel is a good starting point, there’s a whole host of software tools these days that make it easier than ever to figure out safety stock and other issues related to inventory management. These programs can be run on nearly any computer and come with a variety of useful features that can help you avoid stockouts, generate reports, and keep up with changes to your inventory from one moment to the next.
A Milwaukee Tool, we build the One-Key inventory management app specifically with contractors in mind. You can access One-Key from the back office, the tool crib, or on-the-go from the screen of a smartphone or tablet. One-Key provides a cloud-based digital space from which you can easily organize and track the physical locations of your tools, equipment, and essential building materials, enabling you to make informed decisions at a glance about how much of your inventory ought to be held back in reserve. Our small, durable line of Bluetooth Tracking Tags can be affixed to any surface to make it “smart” and have been designed to withstand the outdoor elements and harsh working conditions of a construction site. Additionally, our Asset ID Tags offer durable identification and provide location updates with every scan that can be useful to inventory managers. And have we mentioned that One-Key is free?
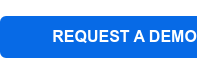
2. Hire an inventory manager
Let’s get real: You’re a busy person. Do you really have the time or the energy to fiddle with complicated equations and learn a whole new suite of software tools? If not, then maybe you should hire someone else to do it for you. An experienced inventory manager can take all the hassle and guesswork out of the safety stock question, freeing you up to focus on other parts of your business. Experts in computer technology, inventory managers are able to bring a whole arsenal of digital analytic tools to bear so you don’t have to. It’s their job to coordinate warehouse activities, maintain strong working relationships with all the key players in your supply chains, craft a sophisticated inventory management plan, and oversee the moment-to-moment in-and-out flow of your inventory, ensuring a smooth operation from top-to-bottom.
How Future Proof Is Safety Stock?
Safety stock is all about planning for an uncertain future, but it isn’t without its own set of risks. Having too much safety stock can put strain on your storage capacity, and introduces the possibility that stockpiled inventory might age or expire. If managed properly, safety stock can save money in the long term. Then again, it isn’t free. Warehouses have costs like rent, property taxes, and utilities, which says nothing of the wages for the staff who keep the whole operation afloat. Just as your inventory can be buffeted by the winds of the market, the expenses associated with holding some supplies in reserve are also subject to uncertainty and ought to be factored into the equation when contemplating the subject of safety stock.
At the end of the day, there is no one-size-fits-all approach, and the global economy will continue to be influenced by a mix of different inventory management strategies. Still, it’s not like there’s some revolutionary new paradigm on the horizon that’s poised to make safety stock irrelevant. That’s what the Just-In-Time strategy promised, and we’ve all seen how that’s turned out for everything from medical supplies to lumber and semiconductors in recent years. One thing is for sure: The future will continue to be uncertain, and setting aside some of your inventory for a rainy day will always be a wise decision.