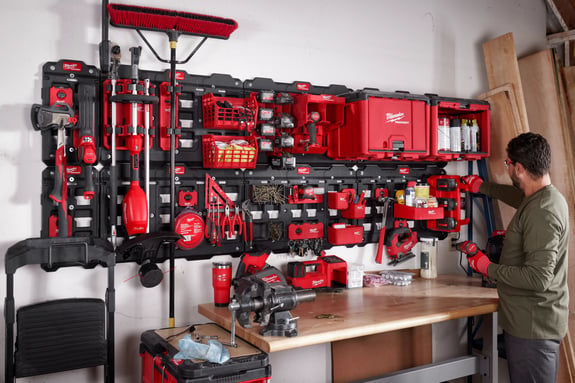
As a construction professional, you know all too well how much your ability to do your job safely and efficiently depends on the tools in your belt. There’s just one small problem: Not every essential tool can fit on your belt at the exact same time.
Imagine laying them all at your feet, each and every tool you use in your work every day—from the smallest screwdriver and lightest power drill to the heaviest duty pieces of equipment in your possession. The sum total of all these items spread out in front of you is your tool inventory.
What to do with it all? Surely you don’t intend to keep all these mission-critical objects laid out on the floor! Too much hazard of tripping or of some of them up and vanishing while you’re back is turned (as tools sometimes tend to do). Best then to secure your inventory someplace safe, be it in a warehouse or work truck. To ensure that every tool is always at your fingertips within a moment’s notice, you’re going to need to organize and keep track of them. This is what’s called tool inventory management.
And here they are! Each tool now neatly labeled, recorded in a written log, every single one organized by type, slotted into the racks, or stowed away cozily within a modular storage container (like Milwaukee Tool’s state-of-the-art PACKOUT system). At last, everything is in its right place…
…Or is it?
There’s really only way to know for sure. You need to compare your written records to the physical tools themselves, checking to see if they match up, if your accounting remains true, and that everything really is in its right place after all. In other words, you need to conduct a tool inventory audit.
In this article, we will explain what inventory audits are, why they’re important, how to conduct them, who conducts them, and how ONE-KEY ™ makes the tool inventory audit process easier than ever.
What Is An Inventory Audit?
Also referred to as a “stock audit,” an inventory audit is the process of observing and verifying physical inventories of items to ensure that they align with the written records that are used to track and coordinate their status, location, and financial impacts on your business.
Fittingly, the practice of inventory auditing sprang from something going wrong— specifically, a case of mass inventory fraud. In the early 1900s, a conman by the name of Philip Musica gained control of pharmaceutical company McKesson & Robbins, the coffers of which he and his family proceeded to plunder to the tune of roughly $19 million, according to SEC estimates. What they'd do is forge false purchase orders, buying drugs cheap, logging them in the inventory at inflated prices, and pocketing the difference. They got away with this scam over a period of many years. A simple inventory audit would have revealed their crime instantly, but checking records against inventories of physical stock wasn’t yet a common practice back then.
Today, inventory audits are one of the most fundamental components of a robust inventory management practice, no matter the industry involved. If inventory management is a system of organization, then inventory audits are the method for ensuring that system remains accurate and up-to-date over time. In construction, inventory audits can be used to verify the status of building material stocks or—as we’re primarily concerned with here at One-Key—tool and equipment inventories.
We’ll explore a few of the ways to conduct an inventory audit in a moment, including how the free One-Key app has made inventory audits easier than ever before.
Why Are Inventory Audits Important In Construction?
So why should you, dear reader, care about inventory audits?
As Max Muller writes in his book, Essentials of Inventory Management, “Because inventory is money.”
It’s worth lingering with Muller for a moment to quote him at length on the relation between your inventory and your bottom line:
“Even if you do not have a financial background, it is important to understand and appreciate that inventory information on financial statements can be useful in the operation of your business. A basic understanding of how inventory appears on the balance sheet and its impact on the income statement and cash flow statement will improve your ability to have the right item in the right place at the right time.”
Put another way: Understanding the connection between your inventory and your finances creates a positive feedback loop. That is, by observing the positive effects that a well-managed tool inventory has on your cashflow and balance sheets, you are more likely to prioritize the tracking and management of said tool inventory as a result, thereby leading to more positive financial effects downstream.
Tool inventory audits are important for many reasons. Discrepancies between your records and your inventory can and inevitably will occur, so it’s critical that you have a process for getting the two in alignment. Inventory audits are that process, keeping you regularly appraised of the status and location of every tool in your possession. Depending on your industry, timely and effective inventory audits can help you avoid stockouts, build a safety stock, practice “lean construction”, and even lower your embodied carbon footprint—if only by a little bit.
Most importantly, however, inventory audits are one of the best ways to gain those critical insights into the inextricable connection between your tools and your company’s financial health, thereby empowering you to optimize the turnover of your assets and help your construction business flourish.
How To Conduct An Inventory Audit
As you can probably imagine, there are many ways to conduct an inventory audit. How you do it ultimately is a matter of preference. It can be as simple, for instance, as doing a walk-through of wherever your tools are stored with a pen and paper, counting and checking items off the list as you go. This old-school method might (emphasis on “might”) be feasible for businesses with smaller inventories, but quickly becomes impractical where larger quantities of tools and equipment are involved.
There are many excellent digital inventory management platforms on the market today that make the process of conducting large-scale inventory audits much easier, whether it’s Oracle’s warehouse planning software or the ERP offerings of Procore, for example. Combining these powerful back-office solutions with the in-field insights of One-Key can elevate your inventory management game to a whole new level.
We’ll take a closer look at how One-Key streamlines the inventory audit process in a moment. For now, here are some tips to help you start thinking about how you want to conduct your own inventory audit.
- Be Prepared: Only you know the size of your tool inventory and the snags that may occur during the inventory auditing process. Be mindful of the obstacles that might hinder your ability to complete an accurate and efficient inventory audit, and take steps to mitigate them before they snowball into larger barriers downstream.
- Use the Right Tools: How to conduct a tool inventory is largely a question of what tool is appropriate for the job. After all, you wouldn’t use a boxcutter to accomplish a task that calls for a SAWZALL ®. This doesn’t mean you need to pick one and only one tool—you can have a variety of inventory management tools in your arsenal. Indeed, we recommend that you do, as different tools are ideal in different situations.
- Establish an Inventory Auditing Pattern: There’s no right or wrong answer to how often you should conduct an inventory audit. Some companies conduct an inventory audit once a year. Others conduct an inventory audit every quarter, or even more frequently. It’s up to you, or your inventory manager, to decide. Whatever your answer, it’s best to establish a reliable pattern so as to ensure a steady rhythm of actionable insights about the inner-workings of your tool inventory.
- Audit Smart: Like spring cleaning, every inventory audit is an opportunity to improve your process and revisit the principles by which your inventory is managed and organized in the first place. Experiment with different inventory management strategies, from the classic physical count to the ABC analysis, to figure out which inventory audit method is right for you.
Who Conducts Tool Inventory Audits?
There are no hard-and-fast rules about who is allowed to conduct an inventory audit. And as we’ll see in the next section, the inventory audit process can be surprisingly simple—especially with the power of modern technology.
At the same time, inventory management is an involved and important job that’s worth doing right every time. So, while there’s nothing keeping you or anyone on your team from conducting an inventory audit, it’s advisable that you entrust this task to someone who has training and is worthy of your confidence (especially when you consider what can happen when your inventory falls into the wrong hands). That person can be a third party auditor or a designated in-house inventory manager.
Inventory managers (who get referred to by a variety of job titles, including warehouse and crib managers) are responsible for directing the allocation, storage, and flow of all the physical assets needed for construction work—everything from building materials, tools, vehicles, equipment, and more.
To understand what a highly-skilled inventory manager can accomplish when they have the right technologies at their fingertips, you need look no further than the story of Josh Patrick.
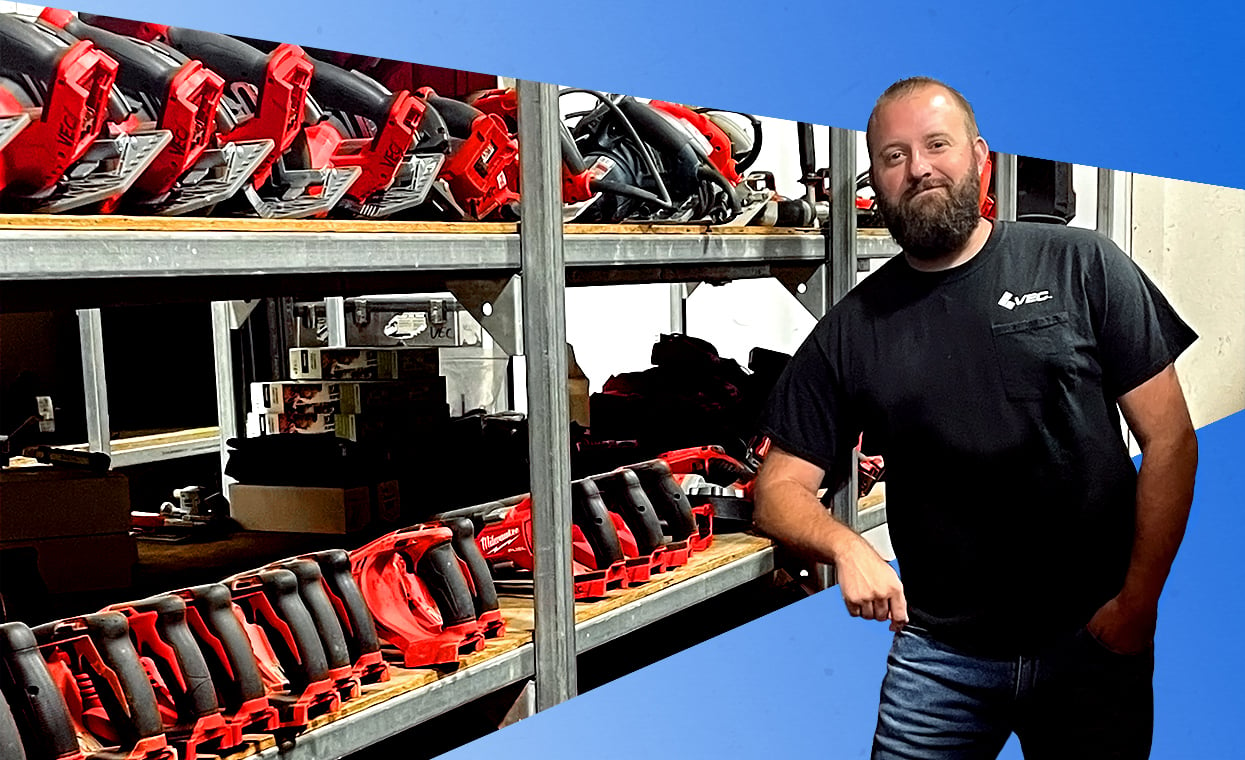
The short version goes a little something like this: The director of field services for VEC Inc. in Girard, Ohio, Patrick and his team of warehouse coordinators were instrumental in getting their construction company back on its feet after VEC suffered a crippling ransomware attack that wiped out all digital records of its vast tool inventory.
How did Patrick and his team restore VEC’s inventory? By digitally organizing all their tools and conducting audits with the Bluetooth functionality of a little app called One-Key.
How One-Key Streamlines Inventory Audits
One-Key is a free and easy to use inventory management app that leverages Bluetooth and IoT technology to wirelessly connect every tool in your possession, making it possible for you to conduct a speedy and comprehensive audit of your entire inventory—repeat: *your entire inventory*—with only a few taps on the screen of your phone or mobile device.
It really doesn’t get any easier than One-Key.
Here’s a brief primer on how it works:
Milwaukee’s ever-expanding line of One-Key power tools come embedded with Bluetooth Tracking Low Energy (BLE) technology. This means that if you own one of these smart tools, then you are able to use the onboard Bluetooth functionality to pinpoint its precise physical location within a 300-foot radius of any mobile device that has downloaded the One-Key app.
Curious about why we use Bluetooth instead of GPS? Watch the video below:
Don’t own any One-Key smart tools? Not a problem. You can make virtually any item trackable by One-Key by fitting it with a Bluetooth Tracking Tag. Small, lightweight, and highly durable, these tags are housed within a weatherproof shell that’s designed to withstand the harshest conditions on any jobsite. You can also log your tools into your digital One-Key inventory with a barcode or Asset ID Tag.
One-Key has a whole host of applications, from inventory management, tool tracking, tool kitting, geofencing, job costing, tool setting customization, remote tool lock-out, and more.
The feature we’re concerned with today is Inventory Auditing.
With One-Key’s inventory auditing feature, you can streamline the typically lengthy and arduous process of checking each physical tool one at a time by simply scanning them all at once.
Here’s how to conduct a rapid tool inventory audit with One-Key in just 5 steps. Before you begin, make sure that you’re mobile device’s Bluetooth settings are turned on and that you’re within the 300 ft range.
- Starting at the home screen of the One-Key mobile app, click the “Places” icon near the bottom of the display.
- From the “Places” screen, click on the “place” that you would like to audit, or scan.
- Now that the place of your choosing is selected, scroll to the bottom and click the “Audit Inventory” button. All your One-Key enabled tools and items in the area will now begin to display on the screen.
- Once the scan is complete, click the “View Summary” button for a breakdown of your results, including which items were detected and which ones weren’t.
- To send or share a report of those results with yourself or your other members of your team via email, click the “Send Summary” button.
It’s as easy as that.
Bottom Line
Strong inventory management is essential to safeguarding the future of your construction company, and no inventory management process is complete without a robust appreciation for the role of the inventory audit. Tracking and managing tool inventories is no small feat, but with technology like One-Key, the process of inventory auditing becomes a whole lot easier.