Josh Patrick
ONE-KEY™ was a life raft that helped VEC Inc. inventory manager Josh Patrick survive and thrive in the aftermath of a devastating ransomware attack.
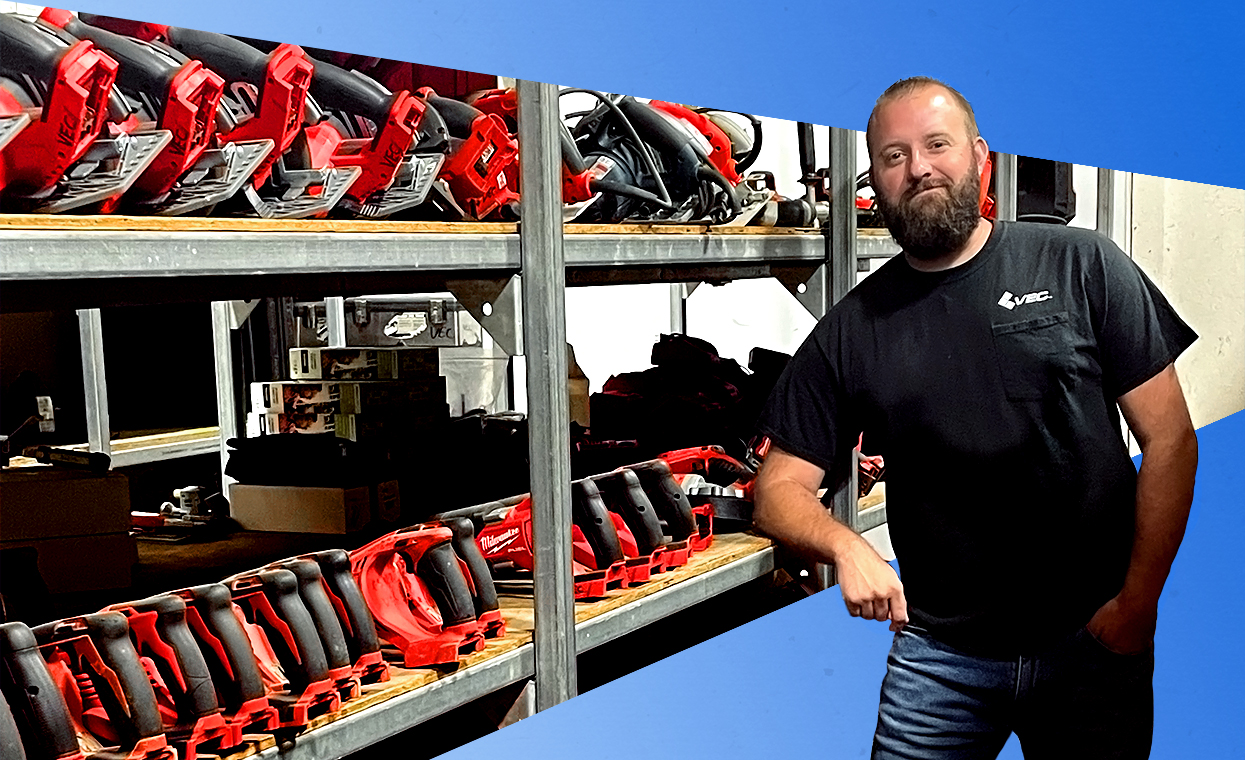
“It’s either we’re going to track our tools with One-Key or we’re not going to be able to track them at all.”
The attack came at 9:42 am on a cold Sunday in March, 2022.
Josh Patrick was at home in Girard, Ohio with his wife and child when he received the call from his boss at VEC.
Ransomware attackers had locked the company out of its entire computer system. Phones, internal emails, contracts, financial files —the hackers had seized and encrypted all of it. The ransom note displayed on the company’s server was sparse and to the point: pay up, or the data would be destroyed.
Patrick’s immediate reaction was shock and “sheer fright”. Among the captured data was VEC’s computerized inventory management system, which meant that all records of the statuses and locations of every single one of the company’s more than 15,000 tools—both in and out of the field—had vanished into thin air.
All eyes at VEC, Patrick said, were suddenly on him and his team members.
“At first I think everyone thought we’d be up and running by the next day,” he said. “Little did we know it would take several months to even get some of our systems back on line.”
Founded in 1965, VEC Inc. (formerly Valley Electrical Consolidated, Inc.) is a construction solutions company based in northeast Ohio that provides a wide range of industrial, civil infrastructure, energy utility, IT, and general contracting services to clients big and small across the US.
Patrick joined VEC as a warehouse coordinator in 2014. His wife, father, an uncle, and a cousin also work at the company. Once promoted to director of field services, it became Patrick’s job to manage VEC’s fleet of construction vehicles, as well as the vast inventories of tools, materials, and equipment stored at the company’s three warehouse facilities.
The ransomware attack sent his world into a tailspin.
“Every department scrambled to see what they had lost,” he said.
Unable to access their company emails, VEC’s employees quickly set up gmail accounts to get basic back-and-forth communications between themselves and the outside world back online. Mission critical contact lists had to be re-entered into Excel spreadsheets, and for the first several months of the crisis, all finances were handled with hand-written checks.
Including the work of tracking the company’s tools.
When the ransomware attack hit, it knocked out the in-house computer system that Patrick and his team used to manage VEC’s extensive tool and equipment inventories. Keeping tabs on the locations and conditions of tools using this system— what Patrick calls “the old way”—had always been a long and arduous process. So much so that he often joked with his boss about the improbable dream of someday having an inventory management platform that he could use from his phone.
Under the old way, warehouse coordinators armed with clipboards would comb through the racks, writing down individual serial numbers, then tromping back to the computer terminal to enter them into the database manually. With the computers down and the old way out of commission, VEC’s inventory management process had suddenly gone from not great to completely untenable.
They tried their best to write everything down on paper, but the undertaking proved too vast.
“Within the first week we pretty much gave up,” Patrick said.
Thousands of tools worth millions of dollars were in the wind, completely unaccounted for. For Patrick, the pressure was on.
“Every day we waited, our equipment transfers skewed even more, making more of a mess for us,” he said. “At the end of the day, you have all eyes on you, with the entire company asking ‘what are you going to do to keep track of all these of tools?’”
A solution soon suggested itself.
“They worked with us like we were partners...We were in a bad spot at a bad time, and we received a lot of support from One-Key.”
For several months prior to the attack, Patrick had been experimenting with a variety of alternative inventory management systems, including an app called ONE-KEY™. The app was fast, intuitive, and fulfilled his blue-sky dream of being able to manage his inventory from his phone. One-Key also came loaded with a wide range of user-friendly features that stood out to him, including rapid digital tool transfers, job-costing, Bluetooth Tracking, tool-kitting, calibration, and overall ease of customization. Best of all, One-Key was free to use—the subscriptions to some of the other systems that he was considering would have cost VEC thousands of dollars per year.
Knowing he had to act quickly, Patrick and his team took One-Key to the owners of VEC. His argument for adopting it was simple:
“It’s either we’re going to track our tools with One-Key or we’re not going to be able to track them at all.”
Having received the greenlight, Patrick and his team got to work as fast as they could.
Every morning for months at a time they would fan out to the company’s warehouses and various job-sites, where they would spend all day scanning tools into One-Key, affixing TICKs and Bluetooth Tracking Tags as they went.
“Between five of us, we were each transferring between 200 to 500 tools a day,” Patrick said. “We’d start off with our phones until our phones would die, then spend the second half of the day scanning tools with our iPads.”
The job of restoring the company’s inventory goes on. Working around the clock for a little more than a year, Patrick and his team have successfully added more than 10,000 tools into One-Key. They have another 5,000 or so to go.
One-Key is lightyears faster in comparison to the old computer system. Without it, Patrick said, his job in the aftermath of the attack would have been 100 times worse.
“Unfortunately, this ransomware attack was a blessing in disguise because we were able to get to a much more modern system,” he said. “If the attack hadn’t happened, I think we may still be using the old system.”
It’s been a long and winding road, but VEC is on the path to recovery, with an IT system that’s stronger than ever. With the ransomware crisis firmly in the rearview mirror, One-Key continues to play a major role in the company’s success. Accessible to multiple team mates, every tool is now neatly displayed in the app with a photo, serial number, and pertinent documentation of warranties and upcoming service dates. Conducting yearly audits is as quick and simple as walking through the warehouse and scanning each tool with a phone. The tool kitting feature has streamlined the organization of tool bins in the company’s work trucks, and project managers routinely use the app to generate torque reports. And just recently, a foreman at VEC was able to use One-Key’s Bluetooth tracking capabilities to pinpoint the location of a $5,000 power tool that had gone missing.
There’s room for improvement, Patrick said, but his positive experience has made him confident that the One-Key team cares and is willing to listen.
“They worked with us like we were partners,” Patrick said. “We were in a bad spot at a bad time, and we received a lot of support from One-Key.”
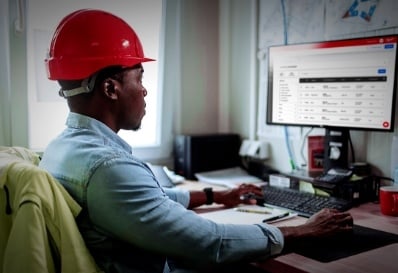
Whitepaper
Request a Demo
Interested in learning more about One-Key? Tell us about your business, and we’ll connect you with one of our team members.
One-Key User
Josh PatrickCompany Name
VECLocation
OhioSize of Tool Inventory
15,000One-Key User Since
2022Stay in the Know
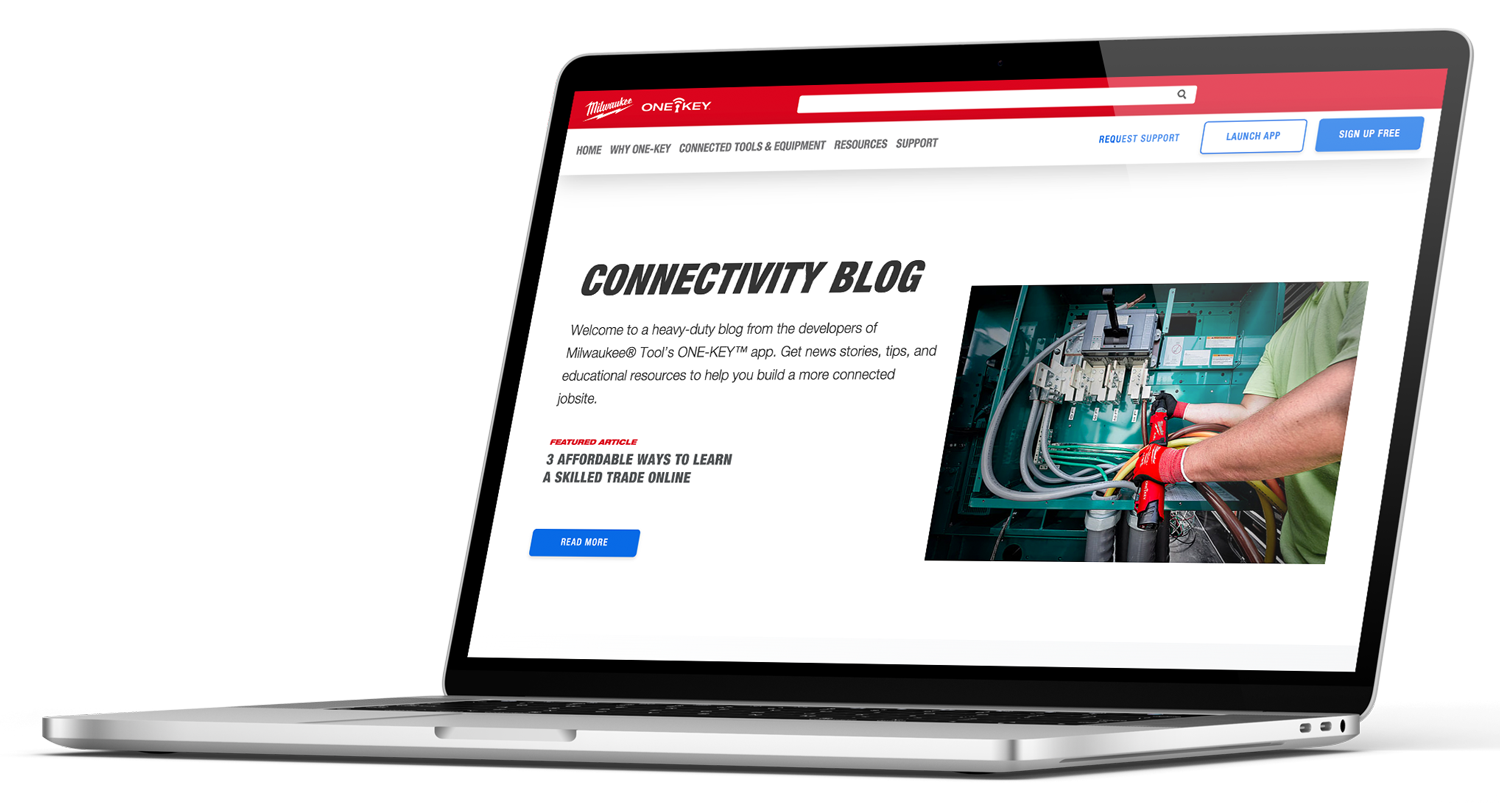