The use of shipping containers in home design and construction has been on an upswing. A report estimates the global market size for shipping container construction will reach $73,070.5 million by 2025, up from $44,788.6 million in 2017. That’s a compound annual growth rate (CAGR) of 6.5% from 2018 to 2025.
Not too shabby.
This surge of shipping container architecture is well documented in the public eye.
Among countless construction-related TV shows, and YouTube videos on the subject, we’ve seen everything from prefab shops pushing out custom designs to pre-used shipping containers finding a new purpose—in keeping with the “reuse, reduce, recycle” sustainable construction mantra. Through these stories, we can live vicariously as environmentally conscious home buyers with the means and determination live simply and off-grid. We can even turn to some of the best construction video games, like The Sims “eco lifestyle,” to find striking shipping container designs amid entertaining, hands-on gameplay, and simultaneously meld environmental perseverance with inspired architectural eclecticism.
Despite being quite compelling in theory, in practice shipping container construction raises some important questions. We will answer each of these important questions throughout this article:
- Is it cheaper to build a house or a container home?
- Are container homes safe?
- What are the pros and cons of building a shipping container home?
- How long do container homes last?
- How might you incorporate shipping containers and prefab into your builds?
Is It Cheaper to Build a House or a Container Home?
The question on everyone’s mind: Are container homes cheaper than traditional houses?
At face value, yes. But there are plenty of factors that could drive the price of a container house to be similarly priced with a traditional house, and in some cases even more.
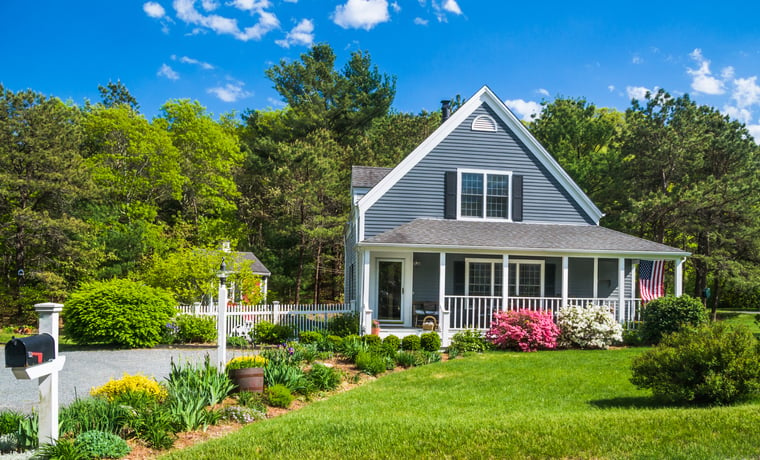
For reference, Forbes estimates the average cost to build a house to be $300k, excluding the cost of land. Similarly, Realtor quotes $296,652, and Rocket Mortgage quotes $290,314 with the national average for the absolute lowest being $15k and the high being $750k per Home Advisor (via Rocket Mortgage).
So, how much do shipping container homes cost?
Purchasing a used or recycled shipping container will set you back around $1,500-$5,000 on average, though the cost of a container may widely vary depending on your geographical location, the condition of the container, size requirements, modifications, and delivery cost.
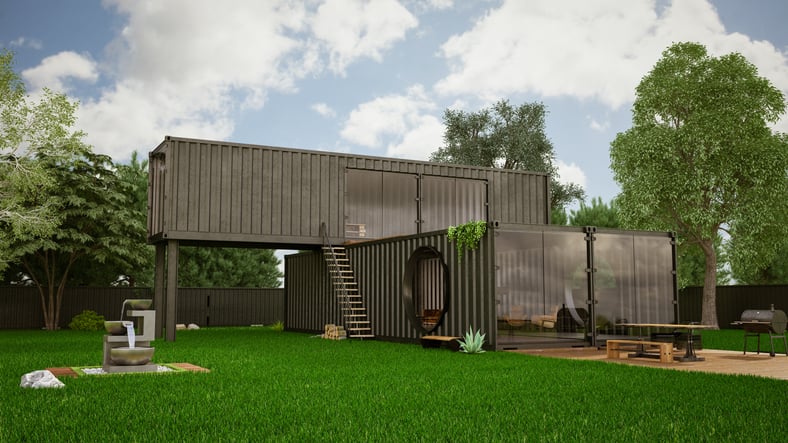
By contrast to traditional houses, completed shipping container homes cost far less than a traditional home, typically ranging between $10k and $35k, and a far cry from the average $300k of building a traditional home; however, there are many factors that could lead container house to a ballooning budget and the dreaded cost overrun, such as modifications and structural engineering necessary to make a highly modified container home structurally sound (and we’ll discuss this a bit later).
On the other hand, an even more cost-effective solution may soon be a 3D-printed home.
Are Container Homes Safe?
From a structural standpoint, shipping containers (in their existing state) are made from strong industrial materials, making them very strong and able to withstand harsh offshore weather conditions.
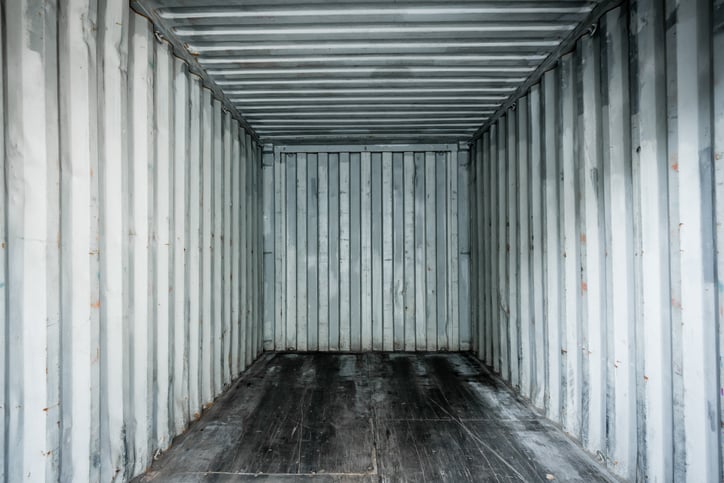
This, of course, changes when you start cutting holes in them.
However, the more pressing safety issue that presents itself with using recycled shipping containers as building materials is the very real possibility they’ve transported toxic chemicals in their former life. To avert this unknown entirely, you can opt to purchase a single-use shipping container; that way, you’ll be able to more precisely verify where the shipping container has been, and what it’s transported.
Pros and Cons of Building a Shipping Container Home
Building a container home purely out of recycled shipping containers may be more of an uphill battle than what meets the eye. Despite having the mystique of sustainability, clients seeking this kind of build may be unaware of certain illuminating factors, like how insulating a shipping container will typically be more effective when using a less eco-friendly method such as spray foam over more sustainable options like recycled cotton or wool insulation.
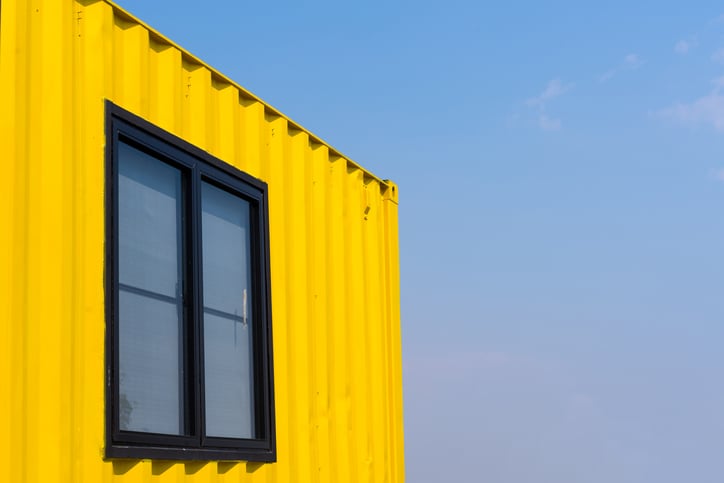
It’s worth noting that other offsite construction methods like modular construction may deliver on client needs with a greater degree of customization.
Pros of Shipping Container Homes
- Cost-Effective, to a degree: Provided that you are building a relatively simple shipping container home, the cost will be generally much lower than building a traditional home from the ground up. As we discussed previously, you can, on average, source a pre-used shipping container for around $3,250. Adding the cost of land, say $3,160 for an acre (reported in the United States Department of Agriculture August 2019 report), and labor costs and architectural drawings, that’s still a far cry from the above-mentioned $300k. However, it’s important to note there are many variables that may drive this initial price through the roof (which we’ll discuss more in the below “cons” section). Going with a prefab shipping container home over a recycled shipping container home can offer clients additional benefits of what you would expect with prefab: predictable costs, in-factory installation (quality control), onsite delivery and preparation, etc.
- Faster build times: Similar to prefabricated construction, building a house with a shipping container can take as few as a couple days to construct modest designs or months to piece together more intricate builds, still a far cry from doing it the old fashioned way. An important thing to keep in mind: Working with a prefab shop versus sourcing perused shipping containers, while not necessarily in line with that “reuse, reduce, recycle” mentality in a literal sense of giving a windswept shipping container a new life, can help solve some of the issues we’ll discuss below that shipping containers pose, such as health risks and QA concerns.
Cons of Shipping Container Homes
Belinda Carr, a YouTuber, architect, and building scientist, outlines in her video titled “7 reasons why shipping container homes are a SCAM” the general problems with creating a home out of a shipping container:
- Size constraints: Standard shipping containers come in two sizes. Smaller shipping containers measure 20 ft long, 8 ft wide, and 8.5 feet tall, while larger shipping containers measure 40 ft long, 8 ft wide, and 8.5 ft tall. While you can custom order taller 9.5 ft tall shipping containers, Carr notes the modifications needed to make a shipping container livable significantly cut into the living space available in what’s already so narrow and awkward: adding insulation, mechanical systems, plumbing, electrical systems, sprinklers, and flooring.
- Possible structural problems: Shipping containers are structurally sound in their existing state. But when cuts are made—to add doors, windows, roof openings and skylights, large hollows to conjoin multiple containers, etc.—the original strength of the shipping container becomes compromised. Clients seeking a container build, thus, should be made aware that reinforcements with metal or wood will need to be made, and necessary framing with traditional drywall will significantly cut into the overall living space.
- Expensive reinforcements if adding cantilevers: The most inspired of shipping container architecture solves the inherent size constraints of building with these narrow modules by bridging multiple shipping containers together in unique configurations that maximize space and adding balconies and wrap-around porches that seamlessly blend indoor and outdoor living. While certainly inspiring, accomplishing these novel architectural feats naturally come with expensive steel reinforcing beams. Prospective clients selecting shipping containers purely as an “affordable alternative” to traditional building should thus be made aware of the limited space and architectural customization of a shipping container build.
- Thermal conductivity of steel: As Carr notes, steel is not a good insulator, thus when using corrugated metal shipping containers as your primary structure, you’ll likely want to insulate the outside of the shipping container and add cladding to avoid mold and rot.
- Health risks with buying old shipping containers: If you’re buying a pre-used shipping container for your build, tracking down where it’s been may be a challenge, and you won’t necessarily know if it was used to carry general consumer goods or toxic chemicals that could cause a health risk. Carr notes that some states like California only allow one-use containers for residential reuse, so you can verify what has been transported in the shipping container. Heavy duty paints on the exterior of the shipping container, she adds, which are added to withstand harsh ocean conditions, contain carcinogenic elements like phosphorus and chromium.
- Cost to transport, depending on the location, may not be logical, especially considering that building with native materials is “the most eco-friendly and cost-effective method.”
How Long Do Container Homes Last?
According to All States Containers, the average life of a container is 25 years with minimal maintenance.
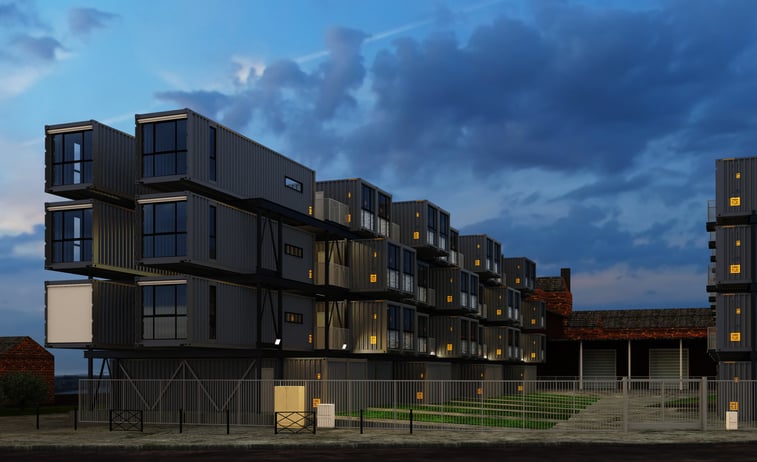
The main problem impacting the longevity of a shipping container home is rust. This could be addressed by adding external cladding, which as discussed above, can also help to insulate and protect against mold.
While the materials used to build a house ultimately help to impact its overall longevity—just as the legendary fable taught us that brick withstands wilder external forces than straw—user input is also important and maintaining a home, regardless of whether it’s made with traditional materials or shipping containers, will require a certain degree of continuous maintenance.
Which States Allow Shipping Container Homes?
All states technically allow shipping container homes. You’ll want to see your state and specific area zoning requirements with regard to building a shipping container home to ensure compliance.
California, for example as previously discussed, allows the use of shipping containers as a building material, but they stipulate ONLY single-use containers to be used.
Beside California, Texas, Tennessee, Louisiana, Missouri, Oregon, and Alaska are among the states that have a more lenient stance toward container homes. For a more complete list, YoungAlfred.com notes the states with “more lenient” zoning laws or “non-restrictive” building codes.
How Can Shipping Containers and Prefab Be Used in Your Projects?
Despite being relatively easy to transport by trailer bed, Belinda Carr notes that it might make the most sense to use recycled shipping containers “in coastal regions near port cities where shipping containers are readily available.” They may similarly be useful in areas where material shortages are common, or areas that are recovering from a natural disaster.
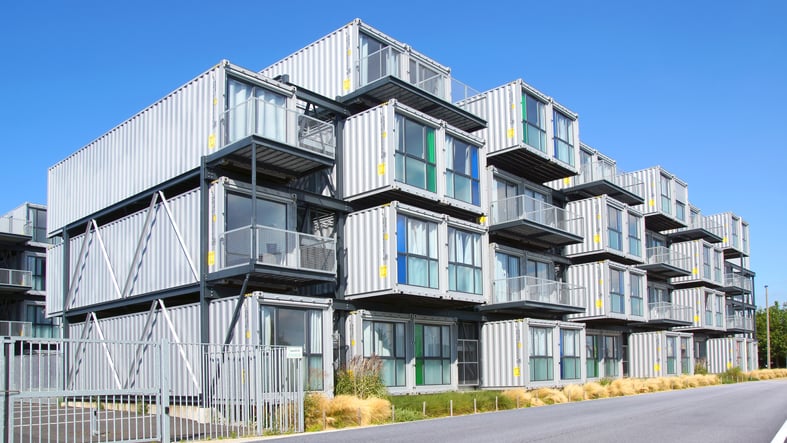
Working with prefab, or even better modular prefab, may drive the kind of outcomes your clients are looking for and provide even better sustainability outcomes.
Additionally compelling applications for this type of construction material may be explored on Hulu with Impossible Builds, where engineered “kit” houses are delivered to particularly challenging sites, like mountainous regions with harsh storms and intermittent, quickly waning opportunities to build.
Bottom Line: Do Shipping Containers Make Good Houses?
Are container homes worth it?
Of course!
As with any home, what you put into it is what you’ll get out of it. If homebuyers are simply after a more cost-effective solution, they can potentially achieve these ends through building a modest container home, quite possibly a “tiny home.” Additional modifications can drive the price to make the container livable and, if intricately designed, structurally sound.
Surely, container homes represent a unique architecture trend that will continue to inspire designers, engineers, and builders to incorporate various materials to design the most innovative and thought-provoking of projects.