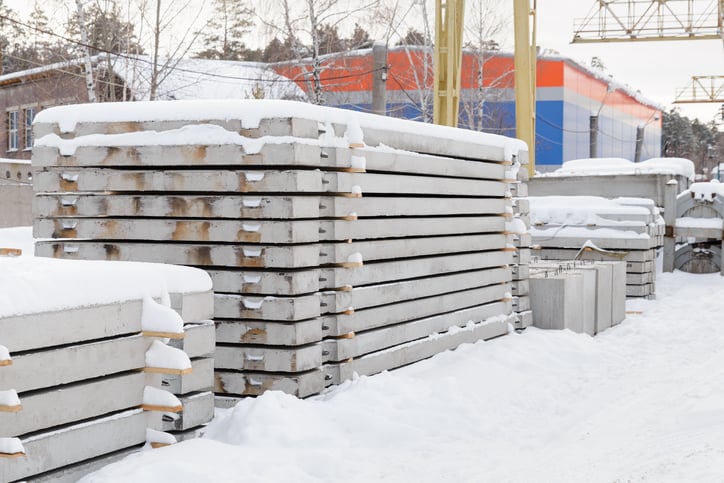
Editorial Note: This article was brought to you courtesy of Rose Morrison, managing editor of Renovated.com.
The holiday season isn't just about gifts and glitter — it's a bustling time for the construction industry. As consumers prepare for festive home improvements and businesses gear up for year-end projects, the demand for construction-related supplies remains steady.
Handling Inventory Issues
Efficient inventory management is essential for construction sites to function smoothly. The holiday supply chain surge can disrupt the regular flow of materials, creating challenges in maintaining optimized inventory levels.
The holiday season brings about increased traffic on roads and heightened logistic activities. Construction projects often rely on the timely delivery of materials, and the congestion caused by holiday-related traffic can affect the transportation of goods.
If a product or service is unavailable, 70% of customers will choose a different store or brand, so implementing practical solutions is critical:
- Real-time tracking systems: Invest in a real-time inventory tracking system that offers instant visibility into stock levels. These systems provide data-driven insights, allowing you to monitor inventory in real time and respond promptly to fluctuations or shortages during the holiday rush.
- Predictive analytics: Leverage predictive analytics to forecast potential inventory issues. Analyzing historical data and industry trends helps anticipate increased demand and adjust inventory levels accordingly. This proactive approach lets you stay ahead of shortages and make informed decisions.
- Safety stock and buffer inventory: During holidays, it's prudent to maintain a safety stock of buffer inventory. This extra supply safeguards against sudden spikes in demand or unexpected delays in material deliveries. Having a reserve ensures you can continue construction activities smoothly even if external factors disrupt the regular flow of materials.
- Collaborative supplier relationships: Foster solid and collaborative relationships with suppliers. Regular communication and transparently exchanging information help create a supportive network. Keep suppliers informed about your project schedules and stay updated on their holiday plans. This collaboration enhances mutual understanding and facilitates smoother transactions during challenging periods.
By addressing the cause of delays head-on and implementing these proactive strategies, you can navigate the complexities of the holiday season in the construction industry with resilience and efficiency.
Dealing With Late Deliveries and Project Delays
The holiday season's spike in consumer demand is one of many factors causing delays in deliveries and project timelines. Construction projects often operate on tight schedules, and any disruption in the supply chain during the holiday season can lead to setbacks. Several challenges contribute to this, including increased traffic congestion, overwhelmed shipping carriers and potential closures of suppliers or manufacturers for holidays.
Businesses say 80% of their supply chain costs have gone up, and over 40% of them cite freight costs.
To navigate these challenges effectively, consider the following strategies:
- Early planning and communication: Anticipate the heightened demand by planning your projects well in advance. This allows you to set realistic timelines and manage expectations with your construction crews and clients.
- Alternative delivery options: Explore alternative delivery methods — such as off-peak hours or weekends — to bypass traffic congestion. Many suppliers and manufacturers may shut down or operate with reduced staff during the holiday period. Collaborate with suppliers to create flexible delivery schedules that align with your project timelines while accommodating the challenges of the holiday season.
- Diversifying suppliers: Relying on a single supplier during holidays can be risky. Consider diversifying your supplier base to increase the chances of timely deliveries. This also provides more options in case one supplier faces unexpected challenges.
Balancing Work and Holidays for Construction Crews
Construction projects often require a skilled and reliable workforce. However, the holiday season introduces availability challenges. Managing construction crews during holidays can be challenging, as half the workforce is expected to decrease for two weeks around Christmas and New Year.
During this time, intelligent tools can make scheduling easier. For example, consider using project management software like Trello or Asana that allows you to visualize tasks and allocate resources efficiently.
Specialized crew management tools like Deputy or When I Work help create schedules while considering individual preferences. These tools ensure you have the right people on the job without slowing down the project. Clear communication about holiday policies and involving your team in scheduling decisions can create a positive work environment and minimize disruptions.
Taking Care of Tools During Busy Times
Tools face extra pressure when construction projects are booming. However, 70% of businesses expected a shortage during last year’s holiday shopping season. Managing and maintaining your tools effectively prevents breakdowns and saves time and money. Use tool management systems with real-time tracking features like ToolWatch or Dewalt Tool Connect to monitor tool usage and identify potential issues.
Set up regular maintenance schedules using software like Fiix or UpKeep, allowing you to address wear and tear before it becomes a problem. Additionally, innovative tools like Milwaukee ONE-KEY™ or Hilti ON! Track are equipped with sensors providing real-time data, enabling predictive maintenance and reducing downtime. By staying on top of tool management and supervision with these tools, you can keep operations running smoothly during the busy holiday period.
Proactive Maintenance Tips
Use these ideas to keep your maintenance schedule on track during the holiday season:
- Regular inspections: Routinely check your tools for visible signs of wear, loose parts or damage.
- Cleaning: Keep your tools clean from debris, dust or any materials that might affect their performance.
- Lubrication: Apply lubricants to moving parts as the manufacturer recommends to prevent friction and wear.
- Calibration: Ensure your measuring tools are calibrated regularly for accurate results.
- Battery care: If your tools use batteries, monitor and charge them according to the manufacturer's guidelines to maintain optimal performance.
- Storage: Store your tools in a dry, secure space to prevent corrosion or damage.
- User training: Train your team on proper tool usage to minimize the risk of misuse or accidents.
Why should you use proactive maintenance? Here are just a handful of reasons:
- Longevity: Proactive maintenance extends the life span of your tools, reducing the need for frequent replacements.
- Reliability: Well-maintained tools are less likely to malfunction, ensuring reliable performance during critical projects.
- Cost savings: Regular maintenance prevents major breakdowns, saving you money on repairs and replacements.
- Efficiency: Properly maintained tools operate more efficiently, contributing to smoother workflows on your construction projects.
Related Article: Construction Guides (Infographic): Should I Repair or Replace My Power Tools and Equipment?
Embracing Sustainability in Construction
Being eco-friendly in construction is gaining importance. Consider using construction materials that are environmentally friendly and partnering with suppliers who follow green practices. This keeps up with industry trends and impresses clients who value environmentally conscious choices.
Consider using recycled materials like reclaimed wood or electric forklifts. Powered by batteries instead of fuel, these forklifts produce no carbon monoxide emissions and can have an operating life of up to 14,000 hours, approximately 4,000 hours more than diesel.
Following sustainable practices promotes a healthier environment for your employees, aligns your projects with environmental values and can lead to cost savings and a positive image in the industry.
Going green can offer construction companies many benefits:
- Client appeal: Clients who value sustainability may choose your services over competitors. Around 74% of consumers say sustainability is essential in buying decisions.
- Environmental impact: Using sustainable materials reduces the ecological impact of your projects.
- Cost savings: Some recycled materials can be more cost-effective than traditional options.
Technology for Efficiency
If you have an intermediate understanding of construction technology, it's time to work smarter. Advanced software for project management and inventory tracking can significantly boost efficiency.
Automation and data analytics streamline your work, making it easier to handle the challenges of the holiday season. Explore project management software like Procore or Buildtrend. These tools help you organize tasks, track progress and collaborate with your team.
Inventory tracking software such as ClearPathGPS, Sortly can ensure you're on top of material availability. Investing in these technologies improves efficiency and frees up your time for more critical tasks.
Editorial Note: At the same rate, Milwaukee Tool’s One-Key delivers incredible value through a free-to-use platform for inventory tracking and comprehensive jobsite management.
The benefits include:
- Efficiency boost: Advanced software automates repetitive tasks, saving time and reducing errors.
- Data-driven decisions: Analytics help you make informed decisions based on project and inventory data.
- Improved communication: Collaborative platforms enhance communication within your team.
Related Article: Construction Automation: How to Simplify Repetitive, Dangerous Tasks
Strategic Planning for the Holiday Season
Being proactive is critical during the holidays. Use past information, industry data and insights to craft a robust plan for dealing with the complexities of the holiday season. This strategic approach positions you ahead of potential problems and ensures a smoother ride during the festive period.
Dive into historical data to understand past challenges during holidays. Use project management tools like Gantt charts to visualize timelines and potential bottlenecks. Also, leverage industry insights from forums or associations to stay ahead of trends and challenges. Here are some steps you can take to plan strategically:
- Review past data: Review your historical project data from previous holiday seasons. Identify patterns, challenges and successful strategies that can inform your current planning.
- Assess supplier schedules: Understand your key suppliers' holiday schedules. Anticipate any closure or reduced working hours that might affect the material deliveries and plan accordingly.
- Collaborate with teams: Engage with your construction teams and subcontractors. Discuss their availability, potential time-off requests and any challenges they foresee during the holiday period.
- Utilize industry insights: Stay informed on industry trends and challenges during the holidays. Participate in forums or industry associations to gain insights into what others in the construction field are experiencing.
- Create contingency plans: Develop contingency plans for potential disruptions. Identify alternative suppliers, have backup crew arrangements and establish communication protocols for quick decision-making.
- Implement agile scheduling: Use project management tools to create flexible schedules. Agile planning allows you to adapt quickly to unforeseen challenges while ensuring project timelines are met.
- Communicate transparently: Maintain clear communication channels with suppliers, teams and clients. Keep all stakeholders informed about potential challenges, your proactive measures and adjustments to the project plan.
- Evaluate technology: Asses the use of construction technology to streamline operations. Consider if new tools or software can enhance efficiency, communication and project management during the holiday season.
- Monitor and adapt: Regularly monitor the progress of your projects during the holiday season. Be ready to adjust your strategies based on real-time data, addressing challenges promptly and ensuring minimal disruptions.
- Post-season review: After the holiday rush, thoroughly review your strategic planning effectiveness. Identify areas of improvement and document lessons learned to refine future holiday-season strategies.
Proactive planning helps you identify and mitigate potential issues before they become problems. Meeting deadlines despite holiday challenges enhances your reputation with clients. A well-crafted plan ensures smooth operations even during the holiday hustle.
The Holiday Supply Chain
The holiday supply chain poses both challenges and opportunities for the construction industry. As you face the festive season, may your projects be merry and your tools be ever-reliable. Happy building!
This is a guest post written by Rose Morrison, managing editor of Renovated.com.