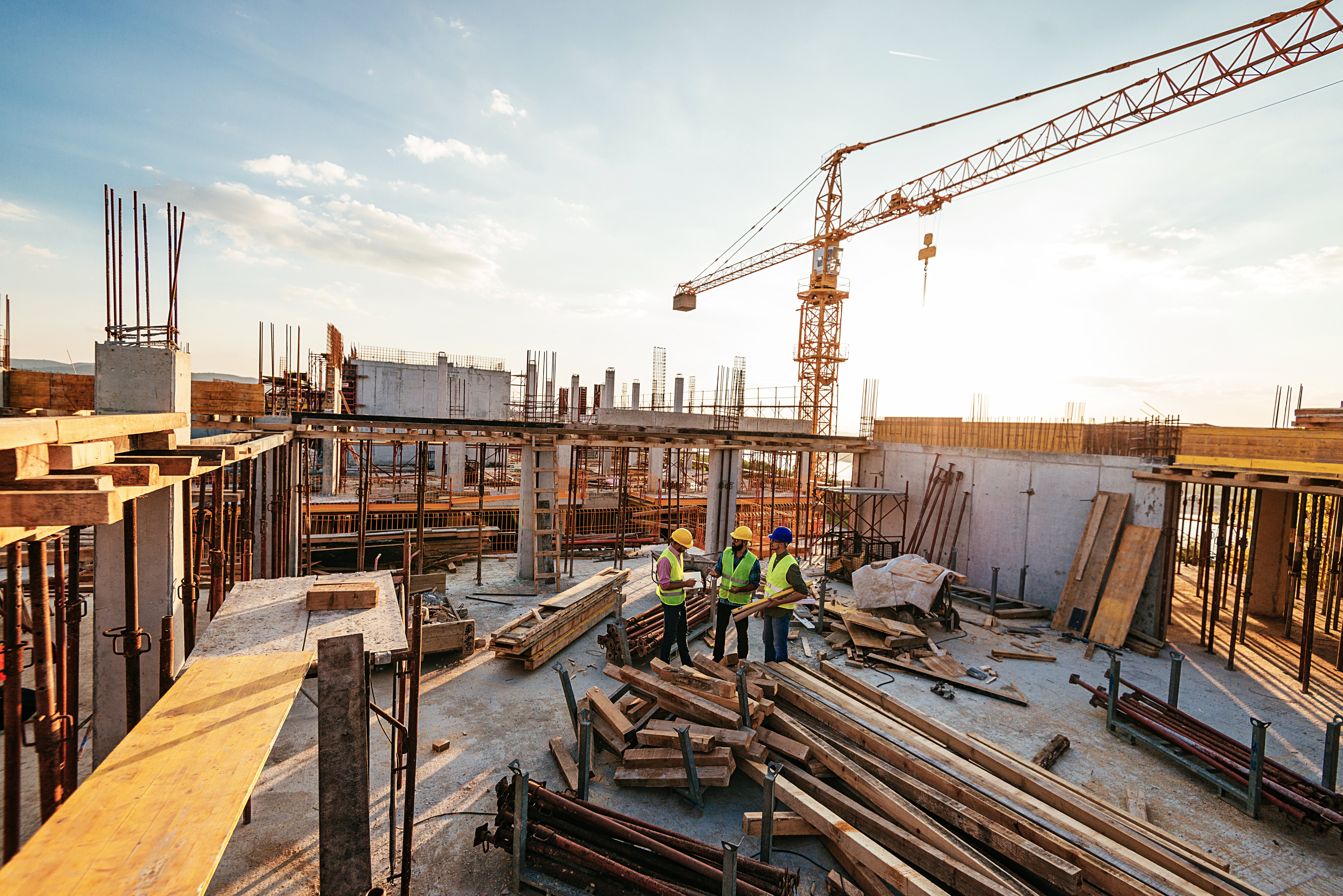
Editorial Note: This article was brought to you courtesy of Rose Morrison, managing editor of Renovated.com.
Commercial and residential construction has been through the wringer these past few years. Pandemic lockdowns, high unemployment, and economic turmoil reverberated throughout the building sector in 2020 and 2021, but the cracks in its foundation began to appear well before. Today, the nation feels the aftershock of mass disruptions in construction labor and supplies as industry professionals and clients grapple with rising materials and equipment costs.
Those involved in commercial and residential projects might question when or if construction materials will ever come down in price. However, to predict the outcomes of recent cost hikes, you must understand how we got to this point in the first place.
Catalysts for Rising Construction Costs
It would be easy to blame the astronomical construction costs solely on COVID-19, but other catalysts have also played a part in driving the price of materials to its peak. The construction industry isn't exactly recognized as the fairest employment sector in the United States, as workers have long advocated for wage hikes and better working conditions.
According to the Associated Builders and Contractors, the industry needs to hire an additional 650,000 workers than usual in 2022 to meet building demand. However, today's labor shortage isn't simply a result of shaky pandemic rebounds.
The last decade had already experienced an 8% drop in skilled workers between 25 and 54 years old — primarily due to retirements and those changing industries for higher pay. Unfortunately, the lagging labor market has vastly hampered productivity and supply chain operations, making it difficult to meet project deadlines and source inexpensive materials.
Related Content:
In 2021, the National Association of Home Builders found 90% of builders reported significant lumber, plywood, oriented strand board, copper wiring, and appliance shortages. With fewer workers and essential construction materials, lumber prices nearly doubled from $35,000 to $71,000, causing a ripple effect across other materials prices and adding $16,000 to the cost of building a single-family home.
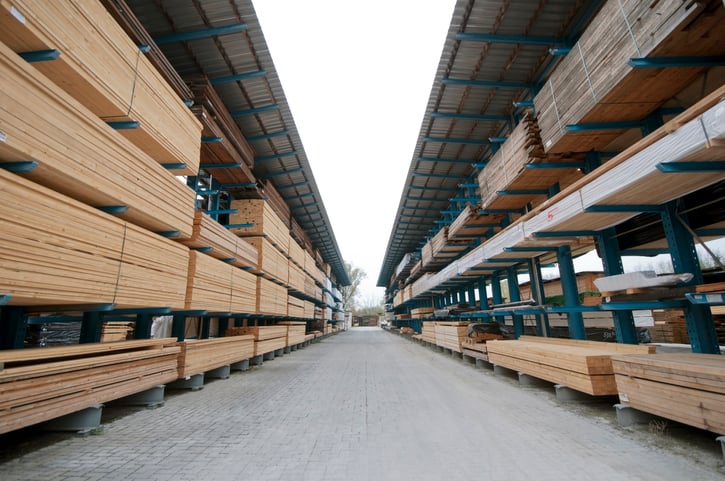
According to the March 2022 Producer Price Index by the U.S. Bureau of Labor Statistics, there has been an 8% increase in building materials and equipment costs since the beginning of the year. This is a 20.4% year-over-year increase and 30% higher than in 2020. Whereas many had hoped prices would've dropped at this point, it's apparent that projects will require re-budgeting to cover the expenses.
7 Ways to Save on Building Materials
While the saying goes, "What goes up must eventually come down," the rules don't seem to apply to construction materials costs — at least for now. In the meantime, builders and clients might consider these seven tips for saving money on construction projects.
- Modify Building Projects
According to Executive Vice President and General Contractor Michael C. Brown of Skanska USA, more clients have chosen to modify their projects rather than wait until market trends improve. Other clients heading developments like hospitals and schools know it's impossible to put these essential projects off any longer.
Communication is critical between builders and clients. Daily discussions should comprise current materials costs, estimated prices, and fluctuations in construction timelines to make the best modification decisions.
Careful planning will also ensure there's little impact on the desired outcomes. For example, you could budget materials by reconfiguring light positioning on a commercial outdoor lighting project. Without compromising occupant safety with fewer installations, simple changes in lighting location and type can reduce energy consumption and improve light pollution in the completed project.
- Purchase Prefabricated Materials
Prefabricated or modular construction materials are manufactured offsite in a factory, then transported and assembled at the jobsite. You might think modular pieces are more expensive since they're custom-made, but prefabrication takes less time, labor, and raw materials than conventional processes. The method also speeds up the timeline since it avoids potential weather setbacks.
While many homeowners opt for modular homes, prefabrication might be best suited for commercial developments. Modular construction is essentially mass production, meaning pieces are somewhat uniform with limited variation for customized spaces. As such, multifamily housing developments, hotels, and hospitals may be better candidates for prefabricated construction.
- Buy in Bulk or Wholesale
Most construction materials are purchasable in bulk or wholesale, allowing you to stock your inventory at a much lower price. Unlike single retailers, there usually isn't a minimum quantity of goods you must buy at wholesale before discounts kick in. Considering the number of construction materials needed for most projects, you'll be able to save plenty of money.
Utilizing inventory management software can also help you stretch your budget even further. Digital tools allow you to track inventory across multiple projects and better prepare for low supplies and equipment stocks.
- Choose Cheaper, Easy-Install Materials
It's perfectly fine to include luxury items in building projects — but amid rising materials costs, it might be more cost-effective to select cheaper, easy-install materials instead. Cheap doesn't equate to low quality, though. When you use materials with easy installation, you can save money on time and labor. The development of easy-install products specifically aims to reduce the chance of making mistakes.
For example, homeowners might choose to install luxury vinyl tile (LVT) flooring in their homes instead of engineered hardwood flooring. LVT flooring is far more durable than traditional vinyl and is becoming increasingly popular for high-traffic rooms. Homeowners will discover that LVT comes in various finishes and tones and can, in some instances, resemble actual wood floors.
These easy-to-install floors cost between $3 and $18 per square foot. In comparison, actual hardwood costs between $6 and $12 per square foot. Also, LVT is much easier to install, with each panel seamlessly locking into the other.
You can reduce materials costs with cheaper, easy-install products in nearly every room. Other ideas to cut costs include kitchen countertops and cabinets, bathroom vanities, and hardware. Likewise, building materials like brick and reclaimed wood are usually more cost-effective than other materials.
- Establish a Supplier Network
Broaden your supplier network to acquire materials at a fair cost. Builders that work with a single supplier lock themselves into that supplier's quote. However, with a network, you create greater competition with lower offers on the materials and equipment you need.
Of course, you can always stick with a supplier that regularly offers a reasonable price, but it's better to do business with multiple distributors. This will also take negotiation skills on your part to get the best quotes. If you play nice but fair with your network, you could significantly cut costs on materials and equipment.
- Negotiate Delivery Fees
In addition to negotiating materials costs with suppliers, you should also negotiate the delivery fees. Construction materials are heavy and oversized, meaning shipping expenses are steep. Depending on how far they transport, you could see a chunk of your budget disappear just for them to show up at the jobsite.
Ask your suppliers for lower or free shipping — they could accommodate you, especially if you're a good customer. However, don't expect them to offer it to you on their own. If you fail to mention it yourself, you could end up paying far more than you need to.
- Avoid Change Orders
Change orders are sometimes necessary for building projects — however, too many will increase expenses, set the timeline back, and lead to construction overruns. Research shows one development project might have 13 change orders from start to finish. Yet, for every change order, there are additional purchasing and wait times for delivery and installation. Additionally, materials might need to be uninstalled before the new item goes in.
Contractors and clients should square away the details early in the building process. That means commercial investors and homeowners need to make crucial decisions quickly and stick to them. Choosing materials early also gives suppliers time to ship them to the site, preventing construction delays and scheduling issues to meet deadlines.
Looking Ahead: The Future of Construction Costs
Forecasting future construction trends is difficult, but most experts agree material costs won't come down in price anytime soon. In August 2022, economic indicators showed total U.S. construction spending reached $1,781.3 billion — about 8.5% higher than in 2021. Another recent report estimates construction costs will increase another 14.1% before the industry sees any glimmer of hope.
Labor and supply shortages, rising interest rates, and inflation will continue disrupting the industry, demanding that everyone throughout the sector. Investors and on-site workers will need to strategize to overcome materials distribution and logistics challenges.
Additionally, innovations and product digitization is expected to hinder an industry that's failed to keep pace with technological advances. According to insights found in one McKinsey study, 67% to 68% of survey respondents believe digitalization will have dire impacts on construction services.
However, at least one recent report by construction consultancy firm Linesight sheds a positive light on the direction commodity prices are headed.
Linesight points out that the cost of lumber has fallen dramatically and anticipates a 12% decline by the third quarter of 2022. Rising interest rates have also reduced copper prices by 12.8% and appear to be affecting other materials costs. Despite the costs of asphalt and bricks rising by mid-year, less-domestic demand will probably drive a downward trend again, as well.
Lower Construction Costs Could Be Coming
With the rising costs of construction materials, builders, investors, and homeowners must find ways to budget their current projects. For now, construction costs are likely to stay at an all-time high, but if projections are accurate, there could be better trends on the horizon.
This is a guest post written by Rose Morrison, managing editor of Renovated.com