Meet Brianne: A ConTech Manager Moving the Industry Forward
In our next installment of our employee spotlight series, we highlight Brianne Stewart, a Senior Construction Technology Manager at Milwaukee Tool.
Brianne Stewart packs her bag—readies her PowerPoint slides—and her ski goggles as she prepares to board a plane west, MKE to DEN. She’s embarking on a journey to the AEC Integration Summit in Denver, hosted by the Construction Progress Coalition, where she’ll lend her trusted voice and contribute to one of these critical dialogues about how the industry can come together, improve, and move forward into a smarter future. That event took place on February 8-10, 2023, and Brianne has the photos to show it, a room full of ConTech professionals held in rapt fascination and spirited dialogue.
A University of Iowa-trained mechanical engineer, Brianne started her career in manufacturing as a process engineer at Procter & Gamble before shifting into new product development (NPD) at John Deere, working in diesel engines. These two experiences in her career she credits as being instrumental in giving her the tools to propel herself to the position she now occupies within the industry.
“I consider myself very fortunate to have learned the ropes of manufacturing at Procter & Gamble. They have a great process for operator training, automation development, preventive maintenance, lean initiatives,” Stewart says, adding, “Similar at Deere, getting the experience with a very formalized product development process at an international company was a great introduction to the space.”
Working for John Deere, she tells me, gave her the opportunity to “work with factories and suppliers all over the world and get an understanding of how an international corporation can continue to develop new products every year.” At John Deere, Stewart worked with both hardware and software products, setting her up for success to later collaborate with the ONE-KEY™ team at Milwaukee Tool.
She’s now a trusted industry voice. She was featured on BuiltWorld’s coveted Adoption Leaders 50 List for the past two years (in 2022 and in 2021), has been profiled by the same organization, and recently spoke at their E&C tech adoption leaders forum. She’s also recently spoken at ABC on building a connected jobsite, spoken about the labor shortage in partnership with Procore at Industrial Grade Innovation, and spoken at the Last Mile at AGC’s IT conference, among countless others.
Stewart started her career at Milwaukee Tool in 2017. Since then, she says the company has experienced rapid growth. “We’ve almost tripled in growth since I started,” she says. She tells me, having the opportunity to be part of that growth is a privilege, but “having the [previous] experience of being part of large companies that had already experienced comparable growth phases makes it feel a little more manageable.”
After joining Milwaukee Tool, Stewart worked for three years in accessories engineering, holding project management roles on the company’s advanced engineering and new product development teams before joining the construction technology team.
What Is a Construction Technology Manager?
Construction technologist is an emerging job title within the industry. Within construction companies, they research emerging technologies and pilot viable solutions that help improve their companies’ workflows, from offsite construction and lean construction to wearables and construction drones to smart tools that can deliver faster installations with greater accuracy and consistency.
At technology-forward power tool solutions providers like Milwaukee®, construction technology managers work alongside internal stakeholders and contractors alike to understand industry trends & identify opportunities where technology may be leveraged in the solutions we put in the hands of our end users.
I had the opportunity to sit down with one such: Brianne Stewart is a Senior Construction Technology Manager at Milwaukee Tool, and I had the privilege of asking her about her role as a ConTech professional within the industry and as a leader within the organization.
What’s a “Day in the Life” of a Construction Technology Manager Look Like?
“At a high level, the purpose of my role is to drive an external understanding of Milwaukee Tool as a technology solutions provider, and an internal awareness of technology trends in the industry that impact our product roadmaps. That translates into a wide variety of day to day activities”
“I maintain touchpoints internally and externally within the company,” Stewart says. “I attend the tech-focused events in the construction industry and have been fortunate to make a lot of great connections there.”
“We lean on those forward-thinking technology adopters in construction for our internal research. I facilitate that outreach and discussion between our advanced research teams and contractors,” she says.
During a typical day in the office, Stewart says, her day can consist of Microsoft Teams meetings with external teams as well as internal partners, with a large part of her job playing a role in the company’s integrations strategy. “I spend time each week meeting with external companies that may want to partner with Milwaukee Tool through software integrations and developing the strategy and roadmap there.”
“I am Milwaukee Tool’s technical support for our trade org partnerships,” she adds. “That’s a big part of my job. Trade org and labor organizations are investing in technology; I get to be the person at Milwaukee Tool to really walk hand-in-hand with them and facilitate how we can support them.”
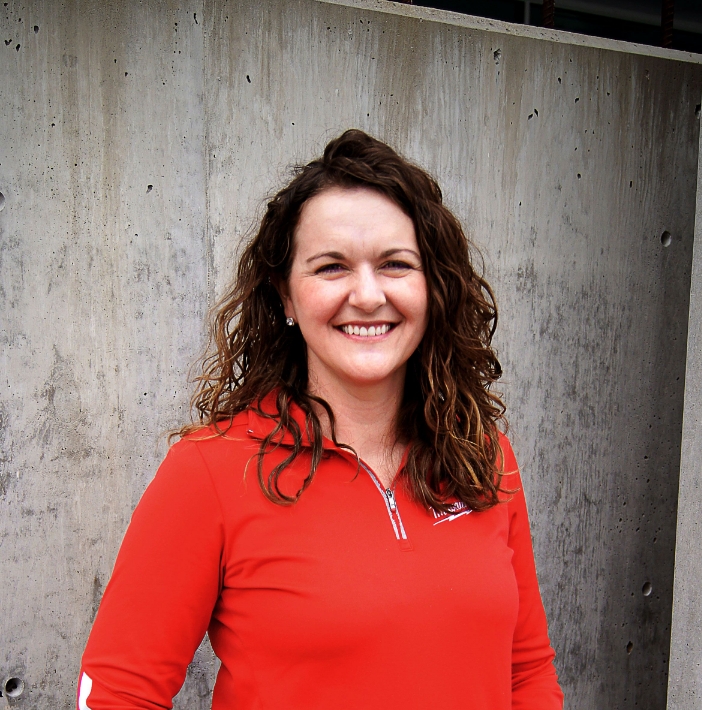
I think the construction industry is facing incredible challenges with not only the workload we’re facing but the requirements on those projects, the complexity, the scheduling, the material shortages, the labor concerns. Adopting technology in a really effective way and incorporating it and really thinking about it as ‘people process technology’ is the only way we’re going to be able to keep moving forward as an industry with the workload that we have coming up.
Brianne Stewart, Senior Construction Technology Manager·Milwaukee Tool
An Interview with Brianne Stewart – Senior Construction Technology Manager at Milwaukee Tool
LM:
Tell me about how you started at Milwaukee Tool.
BS:
5 years ago, in 2017, I had the opportunity to move to the City of Milwaukee to work for Milwaukee Tool, where I worked for three years in accessory engineering.
I held project management roles in our advanced engineering and new product engineering teams. In advanced engineering, I led projects for machine design, for our prototyping and testing machines that we use internally.
For the new product development role, I took on some new and growing categories for our circular saw blades, and then oscillating multi-tool blades after our Imperial Blades acquisition.
LM:
How does Milwaukee Tool differ from previous workplaces?
BS:
For me, Milwaukee Tool is a good middle ground of the very regulated auto industry and the Silicon Valley software style.
For me, it’s very fast-paced, there’s a lot of autonomy, opportunities to lead within, but we’re still making hardware products that build the world, so you get to have that tangible impact on the world around us—which is what I liked about Milwaukee Tool.
LM:
Where does a construction technology manager role fit within Milwaukee Tool’s org chart (e.g., what does collaboration look like between product management, engineering, user research, manufacturing & process improvement, etc.)?
BS:
At Milwaukee Tool, product managers serve as the voice of the customer and are expected to be the interface between our end user-focused sales team and the internal development teams.
Contech fits into there as well, just focused on what’s the 3–5-year roadmap, and technology trends that will impact the end user, and how can we internally make sure we are educated, we understand the risks and opportunities, and have incorporated those findings into our long-term roadmap.
LM:
What are some of the challenges you face in your role, and how do you approach overcoming them?
BS:
I think one of the challenges within construction is that the need to meet timelines sometimes drive decisions on what can be implemented. It’s very rare to find someone who’s against using technology, but it can be hard to pilot, evaluate, and effectively implement with limited resources. There’s so much risk around building buildings where people live, work, and operate. There can be some disillusionment with when you think you’re going to move forward at a faster pace than the industry is really ready for.
For me, I like to look even where we were five years ago, even way more than 10 years ago, I’ll regularly run into foreman that are upset if they don’t have an iPad to work with their day-to-day tasks. I do think technology is getting more in our daily culture, sometimes it’s just hard to lift your head above and appreciate the gains we have made instead of focusing on the gaps in adoption we see.
Organizationally, I think anyone you talk to, balancing initiatives with project deadlines and making a profit that keeps the light on is always a tradeoff discussion.
LM:
Can you speak to how you’ve rose to become such a powerful voice in the construction technology space, and summarize why contractors, tradespeople, and business owners should take construction technology adoption seriously?
BS:
I think the construction industry is facing incredible challenges with not only the workload we’re facing but the requirements on those projects, the complexity, the scheduling, the material shortages, the labor concerns. Adopting technology in a really effective way and incorporating it and really thinking about it as ‘people process technology’ is the only way we’re going to be able to keep moving forward as an industry with the workload that we have coming up.
Really understanding your people and your processes and how technology can support your business goals and project delivery is the only way it’s going to actually be successful.
LM:
What would you say your specialty area(s) is in the ConTech space? What are the topics that get you excited to come to work, generally, and is there anything you’re particularly interested in as of recently?
BS:
I always like to think of myself as a really tech-forward, techy, but where I tend to gravitate is the people-side of tech adoption and how from an organizational structure you can effectively understand your people and your processes and identify where the opportunities are to effectively implement technology in a way that makes sense for you—not just doing something because someone else is doing it.
LM:
Can you name some of the people you admire (could be industry figures as well as leaders in other industries) – and what you admire about these individuals?
BS:
In the broader industry, I really admire Mary Barra, CEO at General Motors (GM).
She’s a great example. How she has taken the helm at General Motors and focused on people, culture, and technology; businesses of any size can take note of that.
While it may be cliché, my top role model in the industry & life is my mom. She was an IBEW electrician before she had me, and she was one of the first female electricians in our area, coming into the industry during the start of affirmative action. After having kids and unfortunately not finding success in our family dairy farm, she put herself back through college while working part time and raising three kids. She’s now about to retire after 20 years teaching woodworking & construction at my local high school.
Elsewhere in the construction industry, I really admire Angie Simon & Sonja Rheaume. They have both established themselves as respected leaders in the industry through their specialty contracting companies, Western Allied Mechanical & Christenson Electric. While that would have been enough for many people, both Sonja & Angie have dedicated themselves to improving and advancing our industry. They have both served in leadership roles for their respective trade organizations, ELECTRI & SMANCA. Additonally, they have used their voice to spearhead initiatives promoting change in our industry for under-represented communities. Sonja created Building Women (https://www.buildingwomen.us/) and Angie created the Heavy Metal Summer Experience through SMACNA (https://hmse.org/) which will enable 400 students this upcoming summer to explore opportunities in the trades.
In construction technology, Tauhira Ali has been a mentor. She really paved the way for me to move from engineering into construction technology and absolutely facilitated my entrance and acceptance within the contech space. Everybody that I could name now that I consider friends and mentors within the broader construction technology space was facilitated by Tauhira in the work she did setting construction technology up for Milwaukee Tool.
LM:
Milwaukee Tool is a technology forward organization, and we often say we’re more than just a “tool company” but also a solutions provider. Put another way. We often strive to provide solutions that meet end users at every stage of their process, aiming to meet them when they start their morning, all the way until they finish their day. Can you speak to where a construction technology manager fits into the organization’s commitment to moving the industry (as well as the company) forward, but also how your role fits into driving comprehensive solutions for end users?
BS:
My role can serve two functions within that. One, externally, is to drive that high-level message and understanding of how Milwaukee Tool is a solution provider. It’s not just a battery and a power tool company; we are impacting the overall productivity, safety, and quality of a jobsite when you use our products across the board. We’re driving those high-level sustainabe goals in alignment with contractors’ goals regarding productivity, quality, safety.
Internally, the goal of my position is to drive clear understanding of the industry trends and where the construction industry is going so that our individual product categories are able to incorporate that into their roadmaps and drive our future product strategy and our relationships there.
LM:
Favorite podcasts and resources you’d recommend to an end user looking to stay up to date on the industry and construction technology?
BS:
The ConTech Crew podcast is such a fixture and establishment within the space, and I really appreciate that it’s a weekly podcast.
Constructed Futures does a good job of digging into technology trends, and Hugh Seaton does a great job of finding good people to contribute to educational experience.
Shared Coordinates is another favorite. It also has a global perspective and provides the opportunity to have technology as Spanish-speaking podcast.
CEMEX’s ConTech Tacos, which is a great newsletter and also offers an international perspective.
LM:
If you weren’t a ConTech leader, what would you be (if you could be anything, no matter how probable or improbable)?
BS:
In college, I was really interested in college in getting an international studies/journalism degree and understanding the idea of how our world works.
LM:
What do you like most about your role?
BS:
The fun part for me is my day to day is different every day. Some days, I’ll have calls with contractors where I’ll bring in our teams and we’ll help guide them in spec’ing out the advanced equipment they’re buying for their prefab shop. Or I get to be out researching in the industry and understanding what are the technologies that are actually really impactful for construction.
And that’s one of the things that’s very common between construction and manufacturing—we don’t adopt technology just because it’s flashy and looks good, but there’s a burden of proof that you have to achieve before there’s wide-scale adoption, and that for me makes it even more exciting, because as we put out more products that are technology-advanced, we know our customers are seeing business value from it and we’re able to explore the pathway with them.
LM:
What has the process of transitioning from an engineer to a construction technology leader been like for you? For tradespeople, long-term, looking to sculpt their career journeys eventually transitioning from working in a skilled trade to becoming a business leader and, what’s more, a thought leader, what are some tips you can provide?
BS:
Being confident in my skillset but being able to acknowledge and admit it and ask for guidance in the areas I’m not as familiar with in the business world is key. In my experience, construction is open to people entering from different career paths, where they have more opportunity to move into new roles, and you’re given the runway to explore a new pathway and learn with it. Finding knowledgeable mentors within the industry and areas where I have gaps has been key to allowing me to transition into new roles.
You’re not expected to come in knowing everything. I think that was the big thing, understanding and leveraging the network you have to cover the gaps and the learning curve there.
LM:
Tell me about Brianne the person. What makes you tick? What are some of your hobbies, outside of work?
BS:
Similarly to within work, where I’m the happiest to work with people, doing different things every day, that extends to my personal life as well.
Anything really where I get out, be around other people, be active is where I’m in my happy place; going to concerts, restaurants, breweries, anything outdoors (I love rock climbing, mountain biking, hiking). The fun part now is my kids are getting old enough that I can share that them. I will be taking my daughter on her first backpacking trip this year.
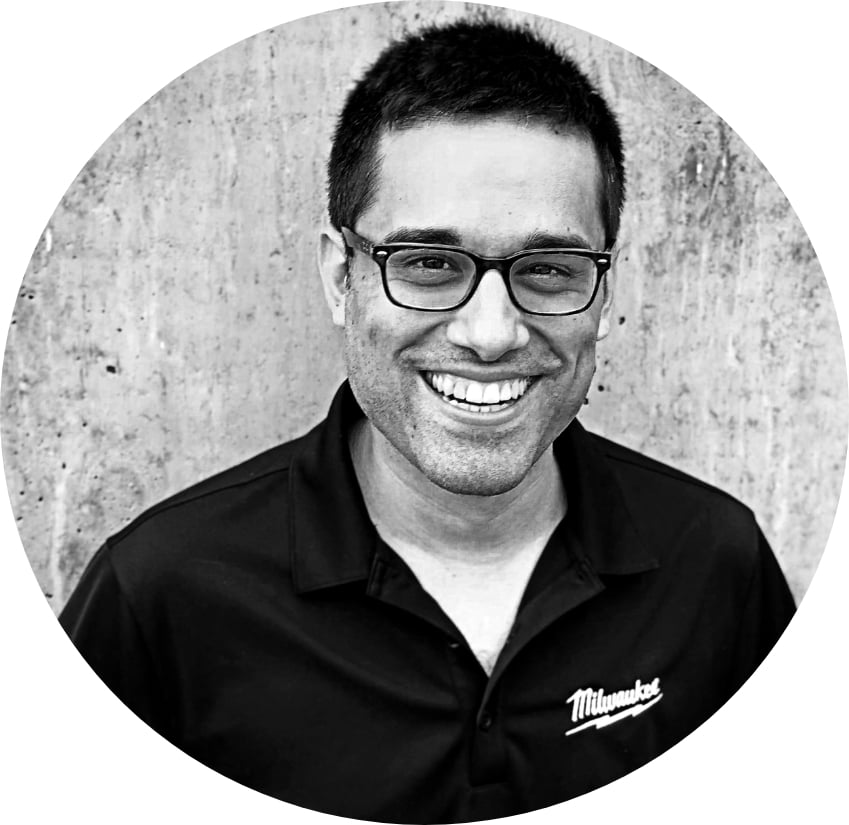
About the Author
Lucas is Content Marketing and SEO Manager for Milwaukee Tool, where he and his team raise awareness about the company’s digital products and educate users on best practices through a variety of content vehicles. More Content By Lucas MarshallSubscribe to Our Blog
Sign up to receive ONE-KEY™ news and updates.
Recent Articles
Essential Strategies for Balancing Work and Life in Construction
Editorial Note: This article was brought to you courtesy of Rose Morrison, managing editor of ...
Maximizing Efficiency: Do Roofing and Scaffolding Specialists Need Construction Software?
Editorial Note: This article was brought to you courtesy of Rose Morrison, managing editor of ...
11 Advancements Women in Construction Have Made So Far This Year
Editorial Note: This article was brought to you courtesy of Rose Morrison, managing editor of ...