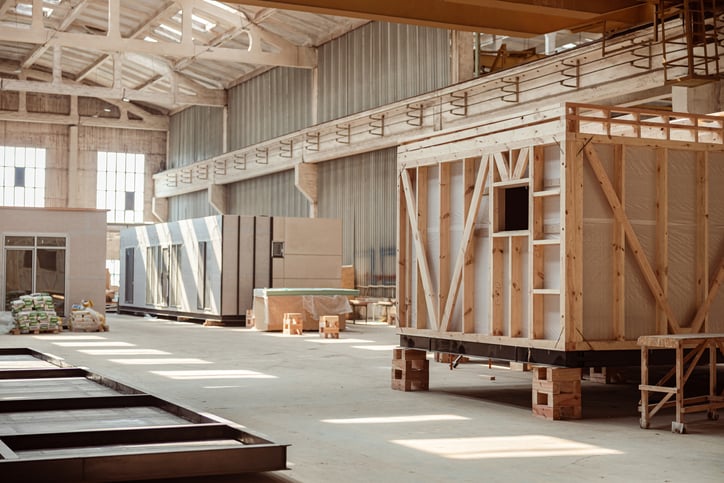
Editorial Note: This article was brought to you courtesy of Rose Morrison, managing editor of Renovated.com.
The U.S. housing crisis is making homes prohibitively expensive for many Americans, but new construction methods offer innovative solutions. From tiny homes to 3D printing, these building techniques are showing promise for resolving the situation and helping people in all income brackets. What is the current state of the crisis, and how can these innovative approaches address the challenges?
Jump Ahead:
The Current State of the Housing Market
The housing crisis is one of today’s most concerning national issues. Over the past few years, costs and availability have grown increasingly challenging, particularly for low-income people.
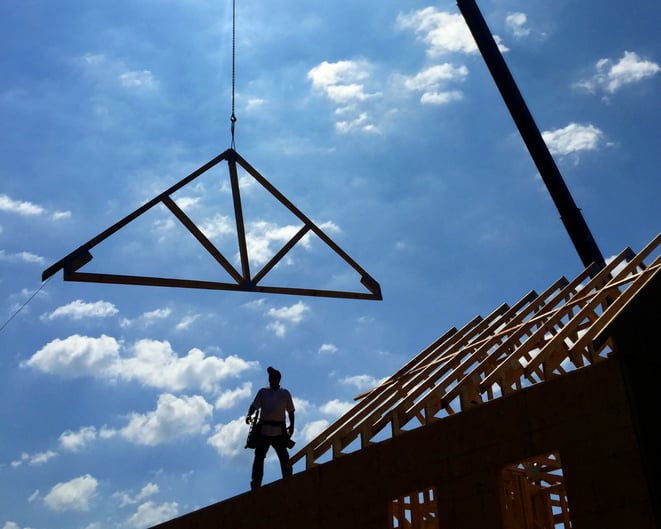
In 2020, an estimated 30% of Americans paid more than 30% of their monthly income on housing. An estimated one in seven households spent more than half of their monthly salaries. Americans making $30,000-$45,000 were hit hardest, particularly Black families.
For some, housing is not accessible at all. As of 2022, there are an estimated 580,466 homeless people in America, 30% of which are families with children. California and New York have the highest populations of homeless people in the U.S., followed by Washington and Oregon. These states are home to some of the nation’s largest urban areas, where homelessness is more prevalent than in rural regions.
The obvious solution to the lack of affordable housing is to build more housing. Unfortunately, this is more challenging than it sounds. There are a few factors preventing construction from meeting demand.
The Construction Labor Shortage
The construction industry has been struggling with a labor shortage for years now, which means there is a minimal population of skilled workers available to build new housing. Associated Builders and Contractors estimates that the industry is over 650,000 workers short as of 2022.
Construction companies can launch ambitious hiring campaigns, but if young people are not interested in working in the industry, there is little they can do to resolve the workforce shortage. Surveys show that only 3% of 18- to 25-year-olds are interested in working in the construction trades. As a result, the workforce is aging without adequate new hires to replace retiring workers. This puts a cap on the number of housing projects that can be in progress at any given time.
Related Articles:
Housing Construction Supply Chain Delays
Another critical challenge for housing construction is the lack of available building materials. Surveys by the National Association of Home Builders reported shortages of essential materials, including appliances, framing lumber, plywood, windows and doors. The 95% shortage of appliances reported in 2021 was the highest home construction-related shortfall on record.
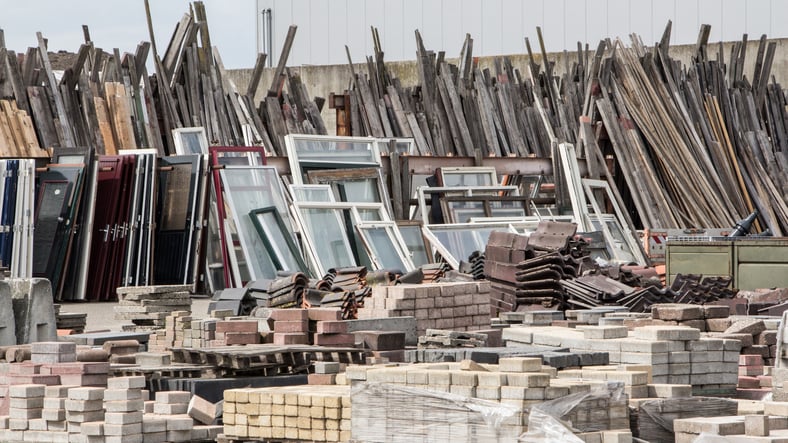
Related Content:
The onset of the COVID-19 pandemic in 2020 sparked widespread supply chain disruptions that unfortunately coincided with a housing boom. Construction companies became backlogged with incomplete projects that were delayed due to shipping delays or supply shortages. The high demand and low supply of critical building materials also increased prices, making housing even more expensive than it already was.
Financial Roadblocks
In 2022, a new challenge took center stage in the housing crisis: interest rates. Orders for new home construction declined, but companies are still working to catch up with delayed projects. Fewer people can afford new houses due to skyrocketing interest rates, making homeownership too expensive for many Americans.
Surveys show that 37% of homebuilders have cut their prices to keep new homes somewhat affordable. Unfortunately, in November 2022, mortgage rates spiked to the highest level recorded in over 20 years.
Surging interest rates are more a symptom of a larger problem than the cause of it. Demand for housing is clearly high, but fewer Americans can afford it. Renting is not a particularly affordable option, either. Studies show that rent continues to increase in many areas across the country.
For example, the average rent for a two-bedroom apartment in New York City was about $3,400 in 2017. In 2022, the price was over $4,000, peaking at $4,500 in August. This indicates that as people get pushed out of the housing market, they turn to renting, causing higher prices due to increased demand.
Promising New Building Methods
Despite the challenges facing the housing market today, several new building methods could provide relief. Conventional construction suffers from workforce and supply shortages, while prospective homebuyers can no longer afford traditional offerings. Innovations could resolve these issues, providing affordable, high-quality housing that can be constructed efficiently.
Prefabricated Construction
Prefabricated construction makes homebuilding more efficient by utilizing the assembly line strategy. This method uses a core set of standard parts to build various structures, and customers can customize their homes without causing production delays. There are a few different types of prefab homes.
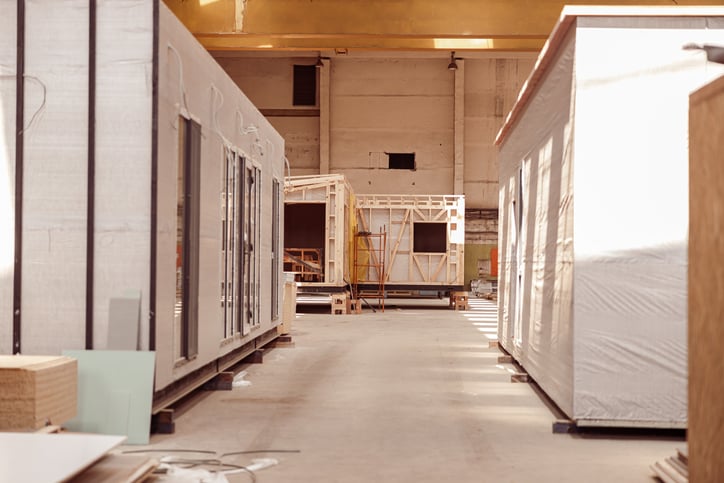
Modular prefab housing consists of “building blocks” that are already 60%-90% finished before arriving at the actual construction site. For instance, entire walls are produced and assembled in the factory and transported to the construction site, where the building can be rapidly constructed like a LEGO set. Modular construction can be used to build single and multifamily housing.
Manufactured prefab homes are built almost entirely off-site before being shipped to the build site. It works similarly to modular construction, except more of the building process happens in the factory, with very little left to do on-site. Conventional site-built houses can be three times more expensive than the average manufactured home, making this one of the most affordable construction methods.
Prefab building methods ease the strain on construction crews and significantly reduce the duration of on-site work. Additionally, the assembly line manufacturing process results in lower home costs since every component has been built in a highly optimized, resource-efficient manner. Building prefab houses in a factory allows assembly teams to rapidly create a new structure without worrying about the weather. All these factors make prefab homes one of the most promising solutions to the current housing crisis.
Tiny Houses
Tiny homes are one of today’s biggest trends in housing. Their potential goes far beyond cute Instagram pictures, though. Tiny houses could be the solution to America’s homelessness crisis.
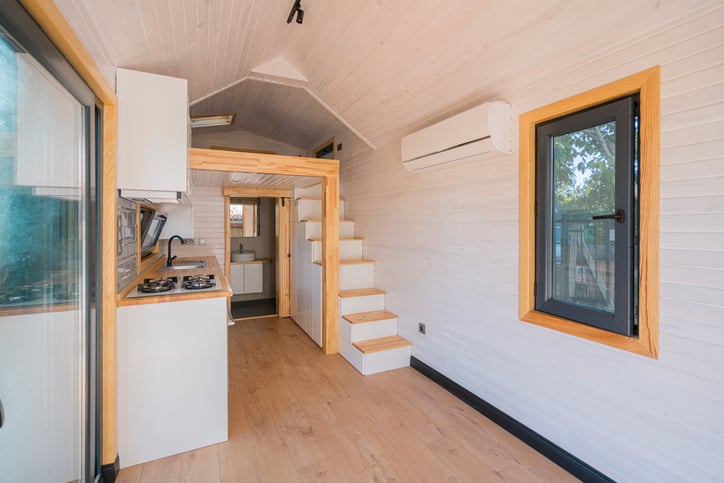
Homelessness is a multifaceted issue that has long-term effects on individuals. The CDC has identified homelessnessas a public health and legal issue. People who are homeless are at higher risk of chronic illness, injuries, HIV infection, alcohol and drug abuse, and mental illness. Getting out of homelessness and poverty can be extremely difficult. It’s even criminalized in some cities, meaning people forced to sleep outside can be arrested for doing so.
Access to housing can truly transform the lives of homeless people, giving them the safety they need to find a job and regain financial stability. Over the past few years, tiny homes have taken off as a solution to homelessness. For example, the nonprofit Occupy Madison builds villages of tiny houses for people in the Madison, Wisconsin, area. Its shelters give the homeless safety and privacy and even allow them to keep pets, which can be highly beneficial for mental health.
Tiny homes aren’t just a solution for the homeless, though. They have also become popular among older adults and young people. These houses offer a great alternative to retirement communities. They can often be moved or built wherever the retiree wants and give the privacy and independence of a traditional home with fewer maintenance needs and lower living costs.
Young people are showing interest in tiny homes for similar reasons. Millennials and Gen-Z are plagued by millions of dollars in debt, making conventional homes prohibitively expensive for many. Tiny homes give them the independence of living alone and owning a house at a much more accessible price. Plus, the lower environmental impact of tiny homes compared to conventional ones appeals to younger generations’ desire to promote sustainability and reduce waste.
The more affordable price bracket of tiny homes could help relieve strain on the rental market. The average cost of a traditional house is over six times more than that of a tiny home. People who might otherwise turn to renting can invest in a tiny home instead, which often offers the same amount of space as an apartment but with more natural light and privacy. Plus, their small size makes construction quick and easy.
3D Printed Construction
3D printed construction is today’s most innovative, cutting-edge building method. It uses giant 3D printers to rapidly “print” the walls of a house, typically using a concrete mixture. Only one or two people need to be on-site to supervise the printing process. Afterward, construction crews come in for a couple of days to add the roof and interiors.
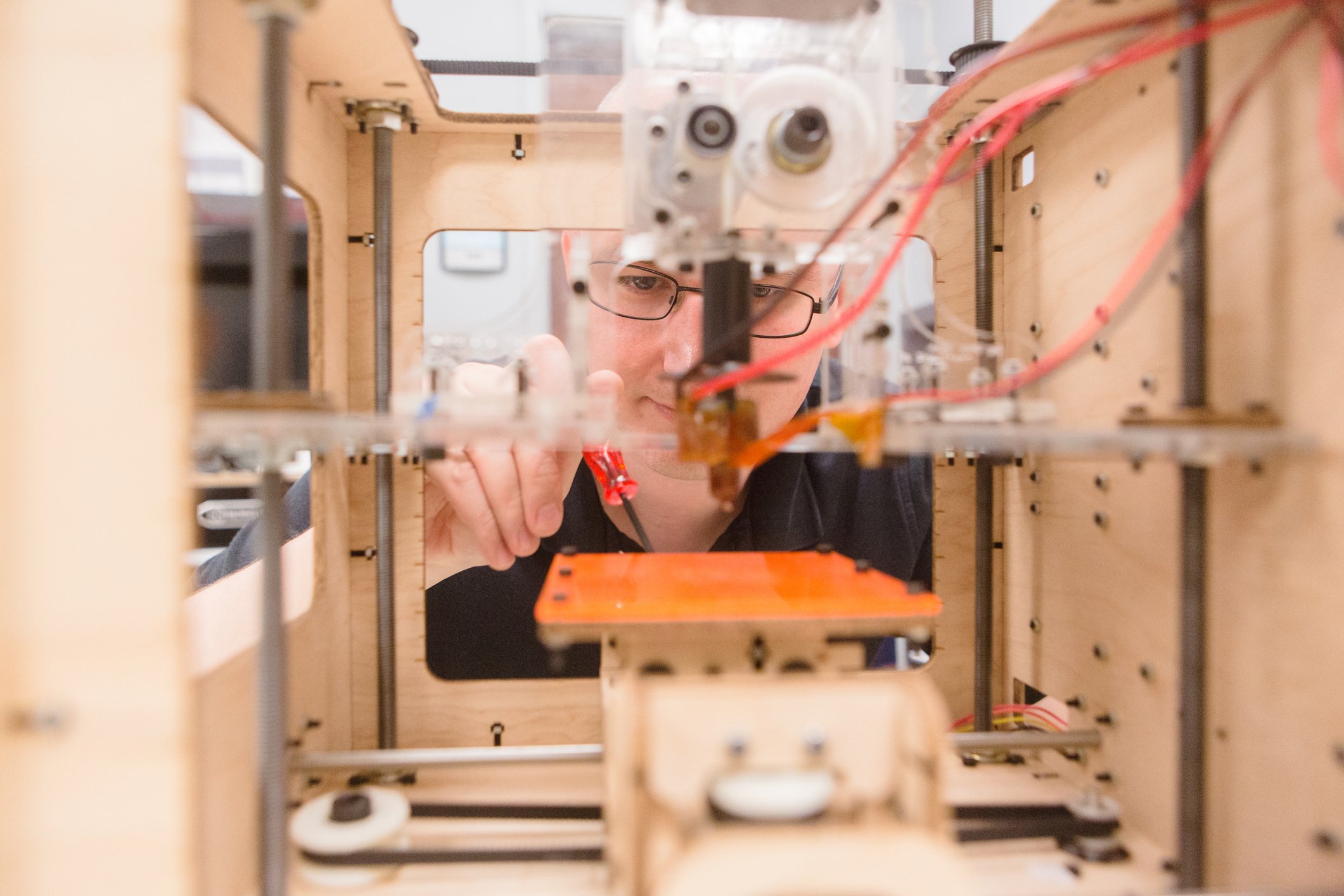
Additive manufacturing is a highly promising construction method for several reasons. First, it minimizes waste and cost by only using the minimum building materials necessary. Any leftover material in the printer can be used on the next project. A typical 3D-printed home can often be made in a few days, with significantly less waste and disruption than conventional methods.
These traits make 3D printing a great solution for the housing crisis. 3D-printed homes can be built in various styles and many look just like a conventional home, only built with stronger concrete walls. The time and resource efficiency of 3D printing also make it a great candidate for the homeless. In fact, the first person to live in a 3D-printed tiny house in the U.S. is a formerly homeless man, Tim Shea, the first resident of the Community First! Village in Austin, Texas.
3D printing has potential in all price ranges. As of late 2022, the largest neighborhood of 3D-printed houses in the world is under construction in Austin, Texas. They are designed for an upper-class market, all sustainably built with solar panels included on every roof. These homes go up to four bedrooms and three bathrooms, with the largest model measuring 2,112 square feet. This neighborhood may be too expensive for the average middle-class American, but it serves as a proof of concept that will likely lead to less costly 3D-printed homes in the future.
This is a guest post written by Rose Morrison, managing editor of Renovated.com